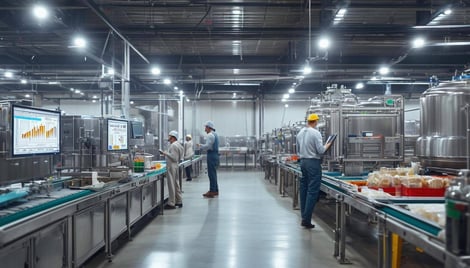
Inventory Tracking and Management in Food and Beverage Manufacturing: The Role of Advanced Integration Tools
Effective inventory tracking and management are at the heart of successful operations in food and beverage manufacturing. Plant managers face unique challenges, from dealing with perishable goods to navigating regulatory compliance, all while striving to minimize waste and maximize profitability. In this fast-paced environment, leveraging advanced technology can make a world of difference.
Integrating production scheduling platforms like PlanetTogether with enterprise resource planning (ERP) systems such as SAP, Oracle, Microsoft Dynamics, Kinaxis, or Aveva is emerging as a game-changer for inventory management.
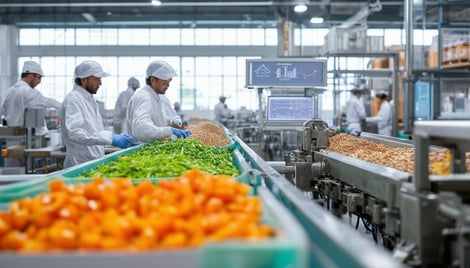
The Inventory Challenge in Food and Beverage Manufacturing
Managing inventory in food and beverage manufacturing is far from straightforward. Perishable goods demand precise tracking to ensure freshness, compliance with stringent food safety regulations, and the ability to respond quickly to market demand. Common inventory management pain points include:
Short shelf lives of raw materials and finished goods.
Complex production processes involving multiple ingredients and varying batch sizes.
Regulatory requirements that demand accurate traceability.
Customer expectations for high-quality, fresh products delivered on time.
Traditional methods of managing inventory often fall short in addressing these challenges. Manual tracking, disconnected systems, and reactive planning lead to inefficiencies and increased costs.

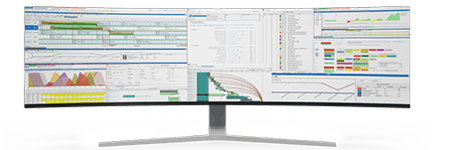
The Power of Integration: PlanetTogether and ERP Systems
Integrating advanced production scheduling tools like PlanetTogether with ERP systems such as SAP, Oracle, Microsoft Dynamics, Kinaxis, or Aveva enables plant managers to take a proactive approach to inventory management. This seamless integration offers several benefits:
Real-Time Inventory Visibility
Integrated systems provide up-to-the-minute data on inventory levels, helping managers make informed decisions. For example, combining PlanetTogether's detailed production schedules with SAP's robust inventory tracking ensures that raw materials and finished goods are always in the right place at the right time.
Enhanced Forecasting and Demand Planning
By leveraging historical data and real-time analytics, integration enhances demand forecasting. Kinaxis, known for its supply chain planning capabilities, pairs seamlessly with PlanetTogether to align inventory levels with anticipated production needs, reducing overstock and stockouts.
Streamlined Production Scheduling
PlanetTogether's advanced algorithms optimize production schedules to align with inventory availability, reducing downtime and waste. Integration with Oracle ERP ensures that these schedules account for procurement lead times and supplier constraints.
Improved Traceability and Compliance
Meeting regulatory requirements becomes simpler with integrated systems. Microsoft Dynamics, for instance, works with PlanetTogether to provide end-to-end traceability, ensuring that every ingredient can be tracked from receipt to finished product.
Reduction in Waste
Integration helps minimize overproduction and spoilage. Aveva's focus on operational efficiency aligns with PlanetTogether to fine-tune production runs, ensuring just-in-time inventory management.
Key Features of Integrated Systems for Inventory Management
When integrating PlanetTogether with ERP systems, plant managers gain access to features that revolutionize inventory management:
Centralized Data Repository: A single source of truth for inventory levels, production schedules, and supplier data.
Automated Alerts: Notifications for low stock levels, expired goods, or production delays.
Dynamic Reallocation: The ability to reassign inventory based on shifting priorities or demand.
Scenario Planning: Simulating different production and inventory scenarios to optimize operations.
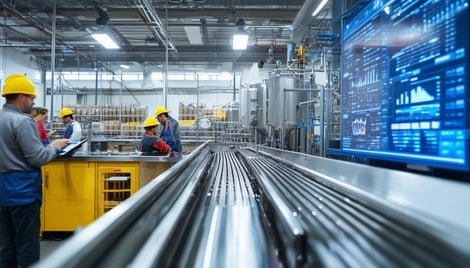
Best Practices for Successful Integration
To maximize the benefits of integrating PlanetTogether with ERP systems, plant managers should follow these best practices:
Define Clear Objectives: Establish goals such as reducing waste, improving forecasting accuracy, or enhancing traceability.
Involve Cross-Functional Teams: Engage stakeholders from production, procurement, IT, and quality control to ensure alignment.
Invest in Training: Equip your team with the knowledge to leverage integrated systems effectively.
Monitor and Optimize: Continuously analyze system performance and make adjustments to improve outcomes.
For plant managers in food and beverage manufacturing, inventory tracking and management are critical to operational success. By integrating PlanetTogether with leading ERP systems like SAP, Oracle, Microsoft Dynamics, Kinaxis, or Aveva, manufacturers can overcome traditional inventory challenges and achieve unprecedented levels of efficiency, traceability, and cost-effectiveness. Embracing these advanced integration tools not only enhances day-to-day operations but also positions facilities to thrive in an increasingly competitive and dynamic market.
Investing in integration is not just a technological upgrade—it’s a strategic move toward a smarter, more resilient manufacturing future. Now is the time to explore how these tools can transform your plant’s inventory management and drive long-term success.
Are you ready to take your manufacturing operations to the next level? Contact us today to learn more about how PlanetTogether can help you achieve your goals and drive success in your industry.
LEAVE A COMMENT