Inventory Optimization through Strategic Planning
Demand patterns are highly variable and shaped by factors like seasonality, consumer preferences, and stringent regulations. Production schedulers are on the front lines, tasked with ensuring smooth production processes and optimal inventory levels to prevent both stockouts and excess inventory. With strategic planning supported by technology integration, such as PlanetTogether with systems like SAP, Oracle, Microsoft, Kinaxis, or Aveva, schedulers can achieve inventory optimization, unlocking cost savings, waste reduction, and better customer satisfaction.
This blog looks into the essential components of inventory optimization and how strategic planning, supported by integrated systems, can empower F&B production schedulers to meet operational goals effectively.
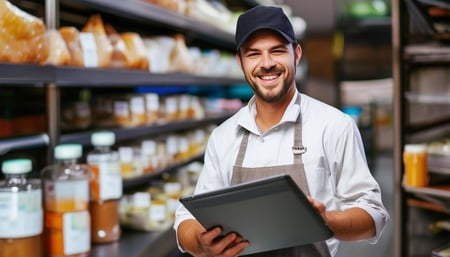
Inventory Optimization in the F&B Sector
Inventory optimization in the F&B industry involves maintaining the optimal balance between available stock and demand without compromising on quality or service. It’s a delicate balance—understocking can disrupt production and delivery timelines, while overstocking ties up capital and risks spoilage. Here’s what inventory optimization entails for F&B production schedulers:
Reducing Waste: Shelf life is a significant concern in F&B. Excess inventory can lead to expired products, resulting in waste and profit losses.
Enhancing Service Levels: Reliable stock levels enable schedulers to meet customer demand consistently, crucial for keeping contracts and growing customer loyalty.
Cost Efficiency: By balancing production with demand, inventory holding and management costs can be minimized, freeing up capital for other business needs.
An effective inventory optimization strategy in F&B involves strategic planning, real-time data integration, and collaboration across departments.
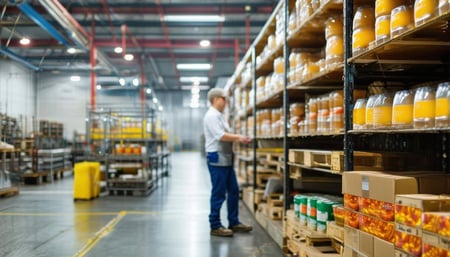
Strategic Planning in Inventory Optimization
Strategic planning empowers production schedulers to address both immediate and long-term inventory requirements. It includes demand forecasting, supply planning, and scenario analysis. Here’s how each element contributes to inventory optimization:
Demand Forecasting: By anticipating demand fluctuations due to seasonality, promotions, and market trends, production schedulers can better align inventory levels with expected sales.
Supply Planning: Coordinating with suppliers to manage the inflow of raw materials, packaging, and other inputs, supply planning ensures that production schedules can run smoothly without excess inventory.
Scenario Analysis: Running different “what-if” scenarios allows production schedulers to assess the impact of sudden changes, such as supply chain disruptions or unexpected demand spikes.
When production schedulers integrate strategic planning with inventory management, they gain control over their stock levels and production flows. For this, robust planning tools and data integration become critical.

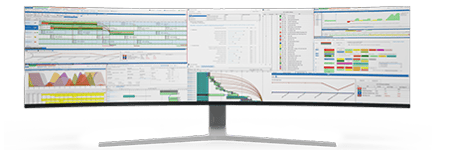
Leveraging PlanetTogether with ERP Systems for Inventory Optimization
PlanetTogether provides F&B production schedulers with Advanced Planning and Scheduling (APS) capabilities that seamlessly integrate with ERP systems like SAP, Oracle, Microsoft, Kinaxis, or Aveva, enabling real-time data flow and collaborative decision-making.
SAP: When integrated with SAP, PlanetTogether provides a comprehensive view of production schedules and inventory data, helping schedulers make data-informed decisions. For example, SAP’s demand forecast can directly feed into PlanetTogether’s scheduling engine, adjusting production to match projected needs while keeping inventory lean.
Oracle: Oracle’s Inventory Management, coupled with PlanetTogether, supports optimized stock levels by adjusting production schedules based on supply chain fluctuations. Production schedulers can avoid overproduction by syncing Oracle data with PlanetTogether, which allows for more agile responses to demand changes.
Microsoft: Integration with Microsoft Dynamics allows for efficient data sharing across scheduling, procurement, and warehouse management. PlanetTogether’s real-time production insights, combined with Microsoft’s ERP functionalities, empower schedulers to make proactive inventory decisions.
Kinaxis: PlanetTogether's integration with Kinaxis allows schedulers to model inventory scenarios under various demand and supply constraints, providing insights that ensure optimal stock without excess.
Aveva: Integrating PlanetTogether with Aveva enables a digital twin of the production environment, allowing schedulers to simulate production schedules and inventory needs virtually. This can identify potential bottlenecks and inventory misalignments before they impact real production.
By harnessing these integrations, production schedulers can view end-to-end supply chain data in one platform, enabling timely, informed inventory adjustments.
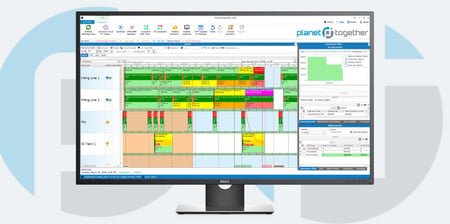
Key Features of PlanetTogether’s APS for F&B Production Scheduling
To optimize inventory, production schedulers need features that support both day-to-day and strategic decisions. PlanetTogether’s APS solution includes capabilities designed specifically to improve inventory management for F&B:
Real-Time Scheduling: Changes in demand or supply can trigger immediate adjustments in the production schedule. This flexibility minimizes the likelihood of stockpiling or stockouts.
Scenario Planning: PlanetTogether allows schedulers to model multiple scenarios, aiding in identifying the best production strategy for inventory control under various demand conditions.
Order Prioritization: Orders are prioritized based on delivery deadlines, minimizing the need to carry excess stock and ensuring a steady flow of finished goods.
Waste Reduction Algorithms: PlanetTogether’s algorithms consider product shelf life and expiration dates, ensuring that perishable items are produced just-in-time for optimal freshness.
These features support the strategic aspects of inventory optimization, allowing schedulers to focus on maintaining the perfect balance of materials and products.
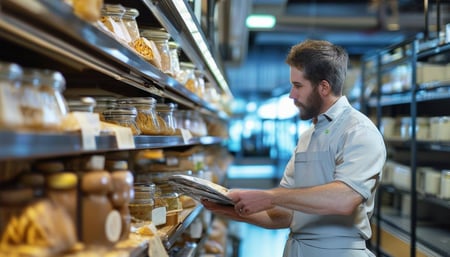
Best Practices for Inventory Optimization in F&B through Integrated Systems
To make the most of PlanetTogether’s APS integration with ERP systems, production schedulers can implement several best practices:
Continuous Data Monitoring: An integrated system means real-time data availability. Production schedulers should monitor this data to stay agile, making production adjustments as demand or supply changes.
Collaborative Planning: By involving procurement, production, and sales in inventory planning, schedulers can avoid communication gaps that lead to either overproduction or shortages.
Proactive Demand Management: Through integration with ERP demand forecasting modules, schedulers can prepare for peak demand periods, such as holidays or seasonal events, by adjusting production schedules and inventory plans in advance.
Regular Scenario Analysis: Scenario planning allows schedulers to adjust for variables like transportation delays or raw material shortages, keeping inventory levels optimal under various conditions.
These practices provide schedulers with the agility needed to adapt to market conditions, enhancing the overall efficiency of the production system.
The Benefits of Strategic Inventory Optimization for F&B
A well-planned inventory strategy, backed by integrated technologies, offers numerous advantages:
Lower Holding Costs: By maintaining optimal stock levels, schedulers reduce storage and holding costs, freeing capital for other business needs.
Enhanced Product Freshness: For perishable goods, a well-tuned inventory system minimizes waste, ensuring that products reach customers at peak quality.
Reduced Production Downtime: By having the right materials on hand when needed, production lines can run smoothly, preventing costly downtimes.
Greater Resilience to Supply Chain Disruptions: Integrated systems offer visibility across the supply chain, enabling production schedulers to pivot quickly in response to disruptions.
Ultimately, strategic inventory optimization is more than a cost-saving tool; it enhances the reliability, efficiency, and sustainability of the entire production process.
In the F&B industry, production schedulers play a crucial role in maintaining the balance between inventory and demand. By utilizing strategic planning tools and integrating PlanetTogether with ERP systems like SAP, Oracle, Microsoft, Kinaxis, or Aveva, schedulers gain the insights needed to optimize inventory without compromising service levels.
The future of inventory optimization in F&B lies in smart integrations that provide a unified view of the production ecosystem. PlanetTogether’s APS solutions, when coupled with ERP systems, offer the real-time flexibility, data-driven insights, and strategic planning tools necessary for success. Embracing these technologies not only enhances inventory management but also builds a more agile, responsive, and sustainable F&B production environment.
Are you ready to take your manufacturing operations to the next level? Contact us today to learn more about how PlanetTogether can help you achieve your goals and drive success in your industry.