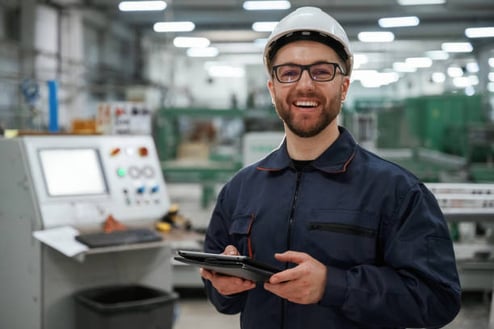
Interactive Production Scheduling: Boosting Efficiency in Packaging and Containers Manufacturing
In the competitive packaging and containers manufacturing landscape, efficiency isn’t just a goal—it’s essential. With fluctuating customer demands, frequent design changes, and tight delivery schedules, production schedulers must go beyond static planning methods. Enter interactive production scheduling—a dynamic, real-time approach to managing manufacturing operations.
By integrating PlanetTogether Advanced Planning and Scheduling (APS) software with enterprise systems like SAP, Oracle, Microsoft Dynamics, Kinaxis, or Aveva, packaging manufacturers are transforming how production is planned and executed.
This blog explores how interactive scheduling improves efficiency, the role of APS integration, and what Production Schedulers need to know to stay ahead.
The Challenge: Static Scheduling in a Dynamic World
Traditional scheduling methods in the packaging industry often rely on spreadsheets, manual inputs, or basic ERP modules. These tools lack the flexibility to quickly adapt to:
Sudden changes in order priority
Unplanned machine downtime
Variable lead times from suppliers
Customized packaging requirements
High-volume, low-margin production runs
In such a volatile environment, production schedules that are too rigid often lead to inefficiencies, excess inventory, or delayed deliveries. The consequence? Higher operational costs and diminished customer satisfaction.
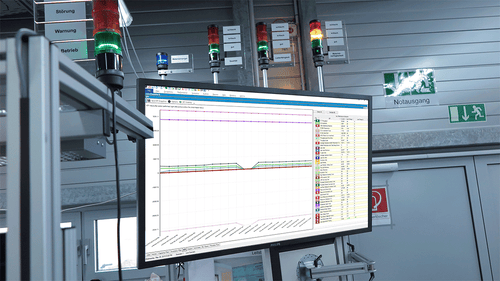
What is Interactive Production Scheduling?
Interactive production scheduling is a visual, real-time, and collaborative approach that allows schedulers to:
Simulate production scenarios
Evaluate multiple scheduling outcomes instantly
Drag and drop jobs across machines and shifts
View constraints like labor, materials, and machine availability dynamically
Receive immediate feedback on schedule feasibility and performance
It empowers Production Schedulers to become agile decision-makers rather than reactive planners.
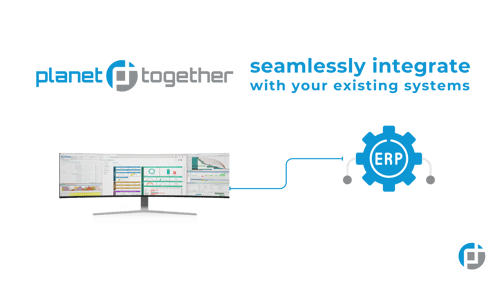
The Power of Integration: PlanetTogether + ERP Systems
While PlanetTogether APS provides powerful visualization and scheduling capabilities, its true potential is unlocked when integrated with ERP systems like SAP, Oracle, Microsoft Dynamics, Kinaxis, or Aveva. This integration enables:
Real-Time Data Exchange
ERP systems hold critical information about inventory levels, work orders, customer orders, and capacity. By connecting PlanetTogether with these systems:
Schedulers get instant access to accurate, up-to-date data
Production plans reflect actual shop floor conditions
Changes in ERP (like a rush order) automatically update the schedule
Constraint-Based Scheduling
PlanetTogether considers all constraints—material availability, machine capacity, labor schedules, and even packaging line capabilities—when generating a schedule. Integration with ERP systems ensures that these constraints are always current.
Enhanced Visibility and Collaboration
Integrated systems provide a shared view of production priorities to other departments—sales, procurement, and logistics—enabling better collaboration and proactive issue resolution.
Benefits for Production Schedulers
Faster Response to Change
Interactive scheduling significantly reduces the time it takes to respond to disruptions, allowing schedulers to re-optimize production quickly and confidently.
Improved On-Time Delivery
By aligning scheduling with real-time data and constraints, manufacturers reduce the risk of delays and enhance customer satisfaction.
Reduced Downtime
Schedulers can spot potential idle times and adjust the schedule in real-time, maximizing equipment utilization.
Lower Inventory Levels
Tighter control over production timelines leads to more accurate inventory forecasting and reduced carrying costs.
Scenario Planning
What-if analysis allows schedulers to explore different scheduling strategies before committing, making it easier to evaluate trade-offs.
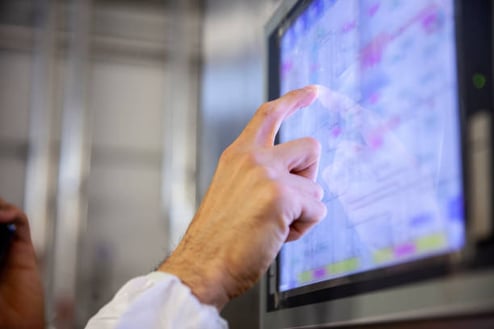
Building the Interactive Scheduling Ecosystem
To successfully implement interactive production scheduling in a packaging facility, here’s a roadmap:
Map Current Processes
Understand current scheduling practices and identify inefficiencies.
Choose the Right APS
PlanetTogether stands out for its intuitive interface, robust constraint engine, and ERP integration capabilities.
Integrate with ERP
Work with IT to connect PlanetTogether with SAP, Oracle, Microsoft, Kinaxis, or Aveva. Ensure bidirectional data flow for seamless operation.
Train and Empower Schedulers
Schedulers should not only learn how to use the software but also understand the business logic behind dynamic scheduling.
Start with Pilot Projects
Test the system on a high-impact production line before scaling to the entire plant.
Continuously Improve
Use KPIs such as OEE, on-time delivery, and schedule adherence to monitor success and iterate on the scheduling strategy.
Real-World Impact
Packaging and containers manufacturers that have adopted PlanetTogether integrated with Microsoft Dynamics or Oracle have reported:
20-30% reduction in lead time
15% increase in on-time delivery
10-25% improvement in machine utilization
Fewer expedited orders and last-minute schedule changes
These outcomes directly translate into increased profitability and stronger customer relationships.
Interactive production scheduling, especially when empowered by the integration of PlanetTogether APS with leading ERP systems, offers packaging and container manufacturers a pathway to smarter, faster, and more efficient operations.
For Production Schedulers, this means transforming from task executors to strategic planners who play a vital role in meeting business goals. By adopting interactive tools and leveraging real-time data, schedulers can navigate complexity, adapt quickly, and drive measurable improvements across the production floor.
Ready to unlock next-level efficiency with interactive scheduling? Contact us today to learn more about how PlanetTogether can help you achieve your goals and drive success in your industry.
LEAVE A COMMENT