Integration for Quality Assurance
Production schedulers face a multitude of challenges, from managing complex production lines to ensuring the highest levels of quality assurance in food and beverage manufacturing. To meet these challenges, integrating advanced planning and scheduling systems like PlanetTogether with enterprise resource planning (ERP), supply chain management (SCM), and manufacturing execution systems (MES) is no longer just an option—it’s a necessity.
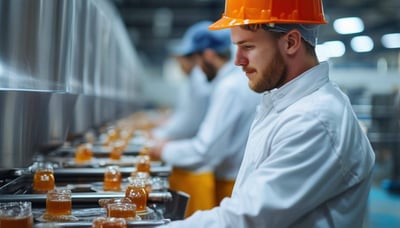
The Role of Production Schedulers
Production schedulers are pivotal in managing the manufacturing process efficiently. Their role involves planning, scheduling, and overseeing production activities to ensure that products are produced on time, within budget, and to quality standards. In the food and beverage industry, where product quality and safety are paramount, the stakes are particularly high.
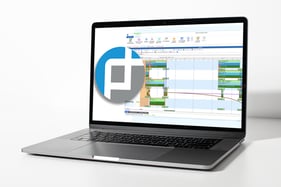
Why Integration Matters?
The integration of systems like PlanetTogether with ERP (such as SAP, Oracle, or Microsoft Dynamics), SCM (like Kinaxis or Aveva), and MES solutions provides a unified platform that enhances visibility, improves decision-making, and ensures a higher standard of product quality. Here’s how integration impacts the role of production schedulers and the broader manufacturing process:
Enhanced Visibility and Control
Integrating PlanetTogether with your ERP system, such as SAP or Oracle, allows schedulers to access critical data in real-time. This data includes inventory levels, workforce availability, machine status, and order details. With this information at their fingertips, schedulers can make informed decisions quickly, adapt to changes, and prevent production delays.
Streamlined Operations
Connecting PlanetTogether with an MES like Aveva enables the seamless flow of information between the shop floor and the scheduling software. This integration helps in tracking the production process at every stage, which is crucial for maintaining quality standards and identifying bottlenecks. By automating data exchange, production schedulers can focus on optimizing processes rather than managing data.
Improved Supply Chain Coordination
Integrating SCM systems such as Kinaxis with PlanetTogether provides a comprehensive view of the supply chain, enabling schedulers to anticipate problems, manage risks, and react to supply chain disruptions more effectively. This integration ensures that scheduling decisions are made with a full understanding of both supply capabilities and constraints, leading to more reliable production plans.
Data Accuracy and Quality Assurance
At the heart of quality assurance in food and beverage manufacturing is the accuracy of data regarding ingredients, production processes, and compliance with safety standards. By integrating ERP and MES systems with PlanetTogether, data from various points in the production and supply chain is consolidated. This integration ensures that all data used in production scheduling and decision-making is accurate and up-to-date, reducing the risk of errors that can lead to quality issues.
Advanced Analytics and Decision Support
PlanetTogether’s advanced analytics capabilities, when integrated with big data from ERP or SCM systems, provide powerful insights into production efficiency, waste management, and demand forecasting. These insights enable production schedulers to optimize schedules, reduce costs, and improve product quality by predicting potential issues before they affect the production line.
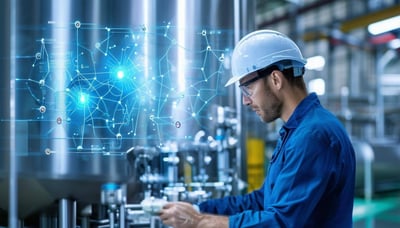
Best Practices for Successful Integration
Implementing an integrated scheduling system is a complex but rewarding endeavor. Here are some best practices to ensure successful integration:
Start with Clear Objectives: Define what you want to achieve with the integration. Whether it's reducing production time, minimizing waste, or improving quality control, having clear goals will guide the integration process.
Ensure Data Consistency: Data should be uniform across all systems to avoid errors and misinterpretations. Regular data audits and validations are crucial.
Train Your Team: Ensure that all users, especially production schedulers, are well-trained on the new integrated system. They should understand how to make the most out of the tools at their disposal.
Continuous Improvement: After integration, continuously monitor the system’s performance and make adjustments as necessary. This includes upgrading software, tweaking processes, and responding to new challenges.
Integration of PlanetTogether with ERP, SCM, and MES systems transforms the landscape of production scheduling in the food and beverage industry. It enhances operational efficiency, improves quality assurance, and provides the agility needed to respond to today’s dynamic market demands. For production schedulers, mastering these integrated systems is key to ensuring that their facility not only survives but thrives in this competitive industry.
Through strategic integration, your manufacturing process can achieve not just compliance with quality standards, but a new level of excellence that sets your products apart in the marketplace.
Are you ready to take your manufacturing operations to the next level? Contact us today to learn more about how PlanetTogether can help you achieve your goals and drive success in your industry.
LEAVE A COMMENT