Integration for Batch Processing
In the dynamic world of industrial manufacturing, particularly within facilities that specialize in batch processing, the seamless integration of enterprise resource planning (ERP), supply chain management (SCM), and manufacturing execution systems (MES) is not just beneficial—it's essential.
This blog explores the advantages and methodologies of integrating PlanetTogether’s Advanced Planning and Scheduling (APS) software with prominent ERP systems like SAP, Oracle, Microsoft Dynamics, as well as SCM systems like Kinaxis and Aveva. We’ll look into the unique challenges of batch processing and how strategic integration can solve these challenges, thereby improving operational efficiency, reducing costs, and enhancing production timelines.
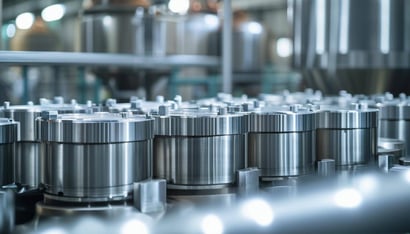
Understanding Batch Processing in Industrial Manufacturing
Batch processing involves manufacturing a quantity of a product in a single run, based on a specific set of orders. This method is common in industries where identical or similar items are produced in groups or batches. Key challenges in batch processing include managing variable production capacities, scheduling for multiple products, handling the intricacies of material requirements planning, and ensuring quality control across different production cycles.
The integration of robust IT systems plays a crucial role in addressing these challenges. By leveraging advanced IT solutions, manufacturers can gain real-time insights into their operations, optimize resource allocation, and ensure a smoother flow of information across departments.
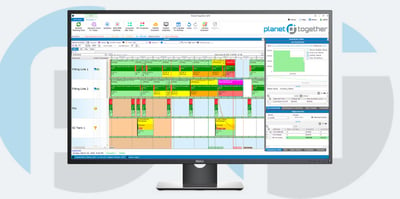
The Role of PlanetTogether in Batch Processing
PlanetTogether APS is a powerful tool designed to optimize production scheduling and increase factory throughput. It provides manufacturers with the agility needed to respond quickly to changes in demand, machine downtime, and workforce availability. The core advantage of integrating PlanetTogether with other IT systems is its ability to enhance visibility across all tiers of the manufacturing process, from raw material procurement to product delivery.
Integration with ERP Systems
SAP Integration: SAP, being one of the most comprehensive ERP systems, covers all core business functions. Integrating PlanetTogether with SAP allows for a bi-directional flow of information. For instance, production schedules created in PlanetTogether can be sent back to SAP to update the ERP’s material requirements planning (MRP), ensuring that materials are available when needed without excess inventory costs.
Oracle Integration: Similar to SAP, integrating PlanetTogether with Oracle ERP can streamline operations. Oracle’s robust database capabilities combined with PlanetTogether’s scheduling algorithms can significantly enhance batch production planning by providing detailed insights into each batch's status, required adjustments, and potential bottlenecks.
Microsoft Dynamics Integration: For facilities utilizing Microsoft Dynamics, integrating with PlanetTogether APS can centralize data management and facilitate real-time decision-making. This integration helps align production schedules with business analytics and inventory management in Dynamics, thereby improving order fulfillment rates and operational efficiency.
Integration with SCM and MES Systems
Kinaxis Integration: Integrating PlanetTogether with Kinaxis RapidResponse can transform how manufacturers respond to supply chain disruptions. This combination allows for rapid scenario planning that can recalibrate schedules based on real-time supply chain conditions, thus maintaining production continuity even under fluctuating supply circumstances.
Aveva Integration: Aveva’s software suite offers detailed insights into process data, which when integrated with PlanetTogether, can enhance the scheduling of batch processes in industries like chemicals and food production. This integration allows for better compliance with safety standards and quality control measures by ensuring that all process parameters are aligned with production schedules.
Best Practices for Effective Integration
Data Synchronization: Ensure that there is seamless data flow between systems. Regular updates and synchronization protocols are essential to maintain accuracy and timeliness of data.
Customization and Scalability: Customize the integration to meet the specific needs of the manufacturing processes. Also, ensure that the integrated system is scalable to adapt to business growth and changes.
Training and Support: Implement comprehensive training programs for all users. Continuous support and updates from both PlanetTogether and the ERP/SCM/MES providers are crucial to adapt to evolving manufacturing needs.
Integrating PlanetTogether with leading ERP, SCM, and MES systems transforms batch processing by enhancing flexibility, increasing transparency, and improving overall efficiency. As manufacturers continue to face pressures to increase productivity and reduce costs, the strategic integration of these IT systems is not just a competitive advantage—it is a necessity.
By adopting a thoughtful approach to integration, manufacturers can ensure they are positioned to meet the demands of the modern market efficiently and effectively. This not only streamlines operations but also supports sustainable growth and innovation in the manufacturing sector.
Are you ready to take your manufacturing operations to the next level? Contact us today to learn more about how PlanetTogether can help you achieve your goals and drive success in your industry.
LEAVE A COMMENT