Medical Manufacturing Supply Chains
With the increasing complexity of supply chains, the need for visibility, efficiency, and adaptability has never been greater. Supply chain managers in medical manufacturing facilities are constantly seeking innovative solutions to streamline operations, reduce costs, and enhance customer satisfaction. Enter digital supply chain solutions, revolutionizing the way businesses manage their supply chains.
In this blog post, we will look into the implementation of digital supply chain solutions, with a particular focus on integrating PlanetTogether, a leading advanced planning and scheduling (APS) software, with some of the industry's top ERP systems like SAP, Oracle, Microsoft, Kinaxis, and Aveva.
By exploring the benefits, challenges, and best practices of such integrations, we aim to provide valuable insights for supply chain managers striving to optimize their operations.
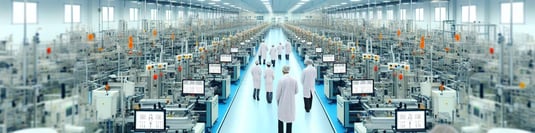
The Need for Enhanced Visibility and Efficiency
In the realm of medical manufacturing, where precision, compliance, and timeliness are paramount, the ability to forecast demand accurately, optimize production schedules, and manage inventory effectively can make or break a company's success. However, traditional supply chain management approaches often fall short in meeting these demands, resulting in inefficiencies, excess costs, and missed opportunities.
This is where digital supply chain solutions come into play. By leveraging advanced technologies such as artificial intelligence, machine learning, and big data analytics, these solutions offer unprecedented visibility into every aspect of the supply chain. From demand forecasting and production planning to inventory optimization and logistics management, they enable organizations to make data-driven decisions in real-time, driving efficiency, agility, and resilience.

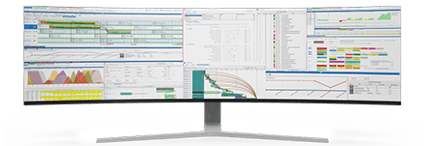
Integration of PlanetTogether with Leading ERP Systems
At the heart of the digital supply chain revolution lies the seamless integration of specialized software solutions like PlanetTogether with enterprise resource planning (ERP) systems, which serve as the backbone of organizational operations. By connecting APS capabilities with ERP functionalities, companies can synchronize their planning and execution processes, eliminate silos, and achieve end-to-end visibility across the supply chain.
Let's take a closer look at how PlanetTogether can be integrated with some of the industry's leading ERP systems:
SAP: With its robust suite of ERP applications, SAP offers a comprehensive platform for managing various aspects of the supply chain, from procurement and production to distribution and customer service. By integrating PlanetTogether with SAP ERP, medical manufacturing facilities can enhance their planning capabilities, optimize production schedules, and ensure seamless coordination between different departments.
Oracle: Another powerhouse in the ERP space, Oracle provides a wide range of solutions tailored to the needs of diverse industries, including healthcare and life sciences. By integrating PlanetTogether with Oracle ERP Cloud, organizations can leverage the combined strengths of advanced planning and scheduling with Oracle's rich ERP functionalities, enabling them to achieve greater agility and efficiency in their supply chain operations.
Microsoft Dynamics 365: As a leading provider of ERP and CRM solutions, Microsoft Dynamics 365 offers a unified platform for managing finances, operations, and customer relationships. By integrating PlanetTogether with Dynamics 365 Supply Chain Management, medical manufacturing facilities can streamline their planning processes, optimize resource allocation, and respond quickly to changing market dynamics.
Kinaxis: Known for its advanced supply chain planning capabilities, Kinaxis RapidResponse provides a cloud-based platform for orchestrating end-to-end supply chain processes. By integrating PlanetTogether with Kinaxis RapidResponse, organizations can achieve real-time visibility into demand and supply dynamics, improve decision-making accuracy, and mitigate risks proactively.
Aveva: With its focus on industrial software solutions, Aveva offers a range of tools for optimizing production processes, managing assets, and ensuring regulatory compliance. By integrating PlanetTogether with Aveva's manufacturing execution system (MES), medical manufacturing facilities can bridge the gap between planning and execution, minimize lead times, and maximize operational efficiency.
Benefits of Integration
The integration of PlanetTogether with leading ERP systems offers a multitude of benefits for medical manufacturing facilities:
Enhanced Visibility: By synchronizing planning and execution data, organizations gain real-time visibility into inventory levels, production schedules, and supply chain performance metrics, enabling them to make informed decisions and respond quickly to changing market conditions.
Improved Efficiency: With optimized production schedules, resource utilization, and inventory management, companies can reduce lead times, minimize stockouts, and improve on-time delivery rates, resulting in higher operational efficiency and customer satisfaction.
Better Decision-Making: By leveraging advanced analytics and predictive modeling capabilities, organizations can identify trends, simulate "what-if" scenarios, and optimize their supply chain strategies, enabling them to make more accurate forecasts and strategic decisions.
Cost Reduction: By eliminating inefficiencies, minimizing waste, and optimizing inventory levels, companies can reduce operating costs, improve profitability, and gain a competitive edge in the marketplace.

Challenges and Best Practices
While the integration of PlanetTogether with ERP systems holds immense potential, it also presents certain challenges and requires careful planning and execution. Some of the key challenges include:
Data Integration: Ensuring seamless data integration between PlanetTogether and ERP systems requires a thorough understanding of data structures, formats, and APIs, as well as robust data governance processes to maintain data integrity and consistency.
Change Management: Implementing new software solutions and processes can disrupt existing workflows and require buy-in from stakeholders across the organization. Effective change management strategies, including training, communication, and stakeholder engagement, are essential to overcoming resistance and driving adoption.
Scalability and Flexibility: As businesses grow and evolve, they need scalable and flexible solutions that can adapt to changing requirements and accommodate future expansion. Choosing modular, extensible platforms and adopting agile development methodologies can help organizations stay agile and responsive to market changes.
To address these challenges and maximize the benefits of integration, supply chain managers should follow best practices such as:
- Conducting thorough requirements analysis and stakeholder consultation to identify key objectives, priorities, and success criteria.
- Collaborating closely with IT teams, software vendors, and implementation partners to design and configure integrated solutions that meet business needs and align with industry best practices.
- Implementing robust data management and governance processes to ensure data accuracy, consistency, and security across the supply chain.
- Providing comprehensive training and support to end-users to facilitate smooth adoption and minimize disruption to daily operations.
- Continuously monitoring and optimizing integrated processes, leveraging analytics and performance metrics to identify opportunities for improvement and innovation.
The implementation of digital supply chain solutions, combined with the integration of PlanetTogether with leading ERP systems, offers unprecedented opportunities for medical manufacturing facilities to enhance visibility, efficiency, and agility across their supply chains.
By leveraging advanced planning and scheduling capabilities, organizations can optimize production schedules, improve inventory management, and respond quickly to changing market dynamics, ultimately driving greater competitiveness and customer satisfaction in the rapidly evolving landscape of medical manufacturing.
Are you ready to take your manufacturing operations to the next level? Contact us today to learn more about how PlanetTogether and integrated scheduling solutions can help you achieve your sustainability goals and drive success in the medical industry.