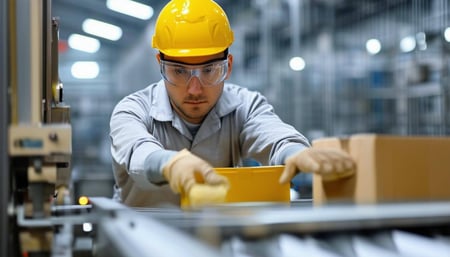
Improving Safety in Packaging Manufacturing
In the packaging manufacturing industry, where efficiency and precision are crucial to staying competitive, safety must always be a priority. A safe work environment doesn’t just protect employees; it also ensures stable production and supports long-term business goals. Many plant managers in packaging facilities are turning to integrated software solutions to create a safer work environment without sacrificing productivity. Integrating PlanetTogether with ERP systems like SAP, Oracle, Microsoft, Kinaxis, or Aveva can be a game-changer in this pursuit.
Let's explore how this powerful combination can bolster safety standards in packaging manufacturing, from reducing workplace hazards to creating proactive safety protocols that align with production goals.

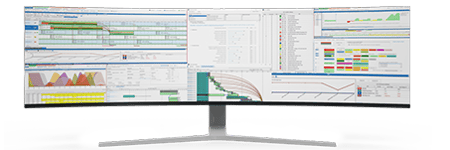
Integrating PlanetTogether with ERP Systems
Automating Safety Compliance Checks
Every packaging manufacturing facility has strict safety protocols, and one of the challenges plant managers face is ensuring compliance without disrupting production schedules. Integrating PlanetTogether with an ERP system can streamline and automate many of these compliance checks, helping plant managers identify and mitigate risks proactively.
Through real-time data synchronization between PlanetTogether and ERP systems, plant managers can automate safety compliance alerts and reminders. For instance, when certain machinery is due for maintenance, the system can flag this for attention, preventing potential breakdowns that could lead to accidents. Automated safety checks provide assurance that each piece of equipment meets safety standards, reducing the chance of unexpected hazards.
How it works: When PlanetTogether is integrated with SAP or Oracle, for example, the ERP can automatically pull maintenance records and machine health data. This integration ensures maintenance alerts are synchronized with production schedules, ensuring that safety checks do not conflict with production timelines. This leads to seamless scheduling adjustments and a significant reduction in potential safety issues.
Improving Worker Safety with Advanced Scheduling
One often-overlooked aspect of workplace safety is how production scheduling impacts worker health and safety. Overworked employees, or those handling repetitive tasks for long hours, are at higher risk of accidents. Integration between PlanetTogether and ERP systems like Kinaxis or Aveva can help optimize scheduling to prevent worker fatigue, reduce repetitive strain, and ensure shifts align with safety standards.
With a comprehensive view of both production demands and workforce capacity, plant managers can better schedule shifts that avoid burnout. For instance, PlanetTogether’s scheduling algorithms, when paired with Kinaxis’s workforce management modules, allow plant managers to plan shifts that minimize excessive overtime or repetitive task assignments, providing workers with adequate breaks and varied tasks. By reducing the chance of worker fatigue, the risk of human error, which can lead to safety incidents, is significantly decreased.
Why it matters: Not only does this reduce the chance of accidents caused by fatigue, but it also ensures that productivity is maintained. The integration helps balance workloads, ensuring a safer and more sustainable pace for employees, particularly in high-stress packaging environments.
Real-Time Monitoring for Hazardous Conditions
Packaging manufacturing involves equipment and materials that can pose risks if not properly monitored, such as heavy machinery, fast-moving conveyor belts, and hazardous materials. Real-time monitoring, facilitated by integrating PlanetTogether with advanced ERP systems like Microsoft Dynamics or Aveva, enables plant managers to respond swiftly to any changes in the production environment that might pose safety risks.
By linking PlanetTogether’s scheduling and resource planning capabilities with an ERP’s IoT-enabled monitoring, plant managers gain a real-time view of equipment status, production floor conditions, and environmental factors such as temperature and air quality. Alerts for potential hazards can be configured to automatically pause production, adjust equipment usage, or notify staff to address issues before they escalate.
Example in action: Imagine a scenario where machinery overheats, creating a potential fire hazard. When PlanetTogether is integrated with Microsoft Dynamics, real-time data from sensors can trigger an automatic alert. This might prompt an immediate shift change or adjust the production schedule to halt affected lines, allowing technicians to address the issue safely.
Reducing Risk with Predictive Maintenance
One of the main causes of accidents in manufacturing facilities is equipment failure. Predictive maintenance, enabled by the integration of PlanetTogether and ERP systems, is an effective way to prevent this. By analyzing historical performance data and leveraging machine learning algorithms, predictive maintenance identifies equipment at risk of failure and schedules maintenance before issues arise.
With an ERP system like SAP or Aveva, which can gather data on machine usage, performance trends, and wear-and-tear rates, PlanetTogether can incorporate this information into production schedules. This integration ensures that maintenance activities are scheduled at optimal times, minimizing disruptions while keeping equipment in safe, working condition.
How it prevents accidents: If a machine is showing signs of wear, the ERP can alert PlanetTogether to reschedule production around a maintenance window. This approach is significantly safer than waiting for a machine to break down during operation, which could lead to operator injury and unexpected downtime.
Creating a Safety-Centric Culture with Digital Training
Safety in a packaging manufacturing plant isn’t just about equipment and protocols; it’s also about creating a safety-first mindset. Integrated platforms make it easier to deliver timely and relevant safety training by using data-driven insights to identify areas where training is needed.
When PlanetTogether is integrated with systems like SAP or Microsoft Dynamics, data from both scheduling and production can reveal insights into specific risk areas, such as high turnover on certain tasks or accident patterns linked to specific shifts. This information enables targeted safety training, which can be automatically scheduled into employee workflows. Training can be directly related to tasks, such as handling a particular machine safely or knowing how to react in hazardous situations, making it more relevant and impactful.
Supporting ongoing training: By using ERP systems for automated scheduling, plant managers can deliver training in short, frequent sessions. This method, sometimes called “micro-learning,” is effective at keeping safety knowledge fresh and practical without pulling employees away from their work for extended periods.
Enhanced Communication for Safety Protocols
Effective communication is a critical component of safety in a fast-paced manufacturing environment. Integrating PlanetTogether with an ERP system like Oracle can streamline communication channels, ensuring that workers are informed of any safety-related changes in real-time.
Whether it’s a scheduled maintenance update, an equipment alert, or a shift change due to unforeseen events, an integrated system allows plant managers to send instant notifications to affected teams. This quick, centralized communication prevents misunderstandings and reduces response time in critical situations, enhancing overall safety on the production floor.
Communication in action: In the event of a hazardous material spill, plant managers can use PlanetTogether’s integration with Oracle to immediately notify the appropriate team members, adjust scheduling to relocate affected tasks, and even alert nearby personnel to the issue in real-time. This rapid communication capability is invaluable in maintaining safety standards in dynamic environments like packaging plants.
Data-Driven Safety Improvements
An often underutilized benefit of integrating PlanetTogether with ERP systems is the ability to analyze and act on safety data. Every safety-related event, whether it’s a near-miss or an actual incident, generates valuable data that can help improve future practices.
By capturing and analyzing this data, ERP systems can provide insights into patterns and trends, such as common causes of near-misses or areas where safety incidents are frequent. Plant managers can leverage this data to make informed decisions about safety improvements, such as adding safety guards, adjusting equipment settings, or revising training protocols.
The role of analytics: With ERP integrations, PlanetTogether can help plant managers establish KPIs related to safety, such as incident frequency, equipment downtime related to safety issues, or compliance rates for safety checks. This data can be analyzed over time to identify opportunities for safety enhancements, turning reactive safety protocols into proactive initiatives.
For packaging manufacturing plant managers, safety is a priority that must align with production goals. By integrating PlanetTogether with ERP systems like SAP, Oracle, Microsoft, Kinaxis, or Aveva, plant managers gain powerful tools to automate compliance checks, optimize worker schedules, monitor real-time conditions, and leverage predictive maintenance. Each of these capabilities not only improves safety but also contributes to smoother, more efficient operations.
Safety is an ongoing commitment, and with the right technology, plant managers can ensure they meet the highest standards. As the packaging industry continues to evolve, those who leverage integrated systems to build a safety-first culture will set themselves apart, providing a secure and productive environment that benefits everyone involved.
Are you ready to take your manufacturing operations to the next level? Contact us today to learn more about how PlanetTogether can help you achieve your goals and drive success in your industry.