Improving Operational Efficiency and Reducing Costs
Production schedulers play a pivotal role in streamlining operations, maximizing productivity, and reducing costs in chemical manufacturing. Today’s chemical industry is under increasing pressure to produce high-quality products faster and more cost-effectively, all while maintaining stringent safety and environmental standards. The integration of advanced production scheduling tools like PlanetTogether with ERP systems such as SAP, Oracle, Microsoft, Kinaxis, or Aveva offers a powerful solution, enabling schedulers to optimize workflows and navigate operational challenges with greater agility and insight.
This blog will explore how the integration of PlanetTogether with these robust ERP platforms empowers production schedulers to improve operational efficiency, minimize costs, and enhance decision-making in chemical manufacturing environments.
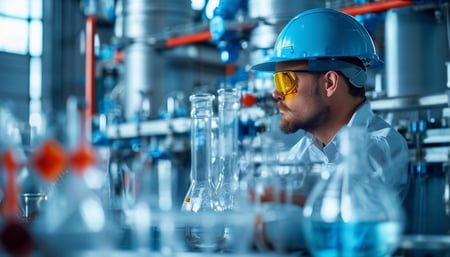
The Role of a Production Scheduler in Chemical Manufacturing
In chemical manufacturing, production schedulers must juggle various complex tasks, from balancing production timelines and managing resource allocation to forecasting demand and mitigating risks. Additionally, they must adhere to regulatory compliance and ensure adherence to safety standards. The intricate nature of the chemical industry, with its long lead times, intricate supply chains, and volatile raw material costs, makes the scheduler’s role especially challenging.
To address these demands, a well-integrated scheduling and ERP system is essential. With tools like PlanetTogether, production schedulers gain real-time insights, enabling them to make proactive adjustments that can lead to significant cost savings and improved operational efficiency.

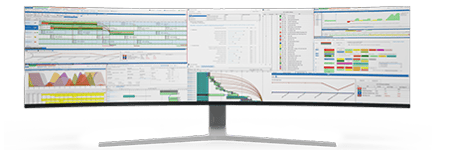
Understanding PlanetTogether Integration with Major ERP Systems
Integrating PlanetTogether with ERP systems like SAP, Oracle, Microsoft Dynamics, Kinaxis, or Aveva creates a unified environment where data flows seamlessly across production, scheduling, and management layers. Let’s examine some key advantages of this integration and how it impacts production scheduling in chemical manufacturing:
Centralized Data and Real-Time Visibility: Integration enables real-time data synchronization between the ERP system and PlanetTogether. This centralization provides production schedulers with a unified view of all relevant data—inventory levels, raw material availability, workforce capacity, and more—reducing the need for manual data entry and minimizing errors.
Enhanced Collaboration and Communication: A robust ERP integration fosters better communication between departments. Schedulers can work closely with procurement, supply chain, and production teams to respond swiftly to any changes, preventing costly disruptions.
Automated Scheduling Adjustments: With PlanetTogether's automation capabilities, schedulers can adjust production schedules based on real-time updates from ERP systems. This reduces the burden of manual adjustments, allowing schedulers to focus on strategic decision-making that enhances productivity.
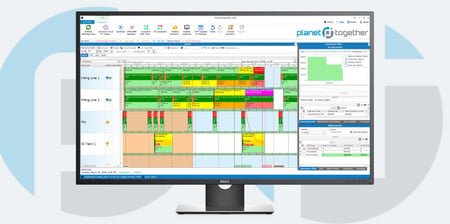
Key Benefits of PlanetTogether Integration for Chemical Manufacturing
1. Optimized Resource Allocation
Chemical production often relies on costly and specialized equipment, raw materials, and skilled labor. Poor resource allocation can result in downtime, waste, and lost revenue. By integrating PlanetTogether with ERP platforms, production schedulers can utilize historical data and demand forecasts to allocate resources more effectively. The integration allows schedulers to identify underutilized assets, balance workloads, and prioritize high-impact production tasks.
With optimized resource allocation, production lines operate more efficiently, leading to reduced waste and lowered operating costs. This level of strategic scheduling not only reduces overheads but also enhances the facility’s productivity by ensuring that all resources are used to their fullest potential.
2. Improved Inventory Management and Reduction in Holding Costs
One of the largest expenses in chemical manufacturing is the cost of holding raw materials and finished goods. Holding costs can accumulate rapidly, especially for chemicals with limited shelf lives or specific storage requirements. PlanetTogether’s integration with ERP systems allows production schedulers to monitor inventory levels in real-time, enabling just-in-time (JIT) production.
With accurate inventory data at their fingertips, schedulers can avoid stockouts and overstocking, reducing the associated holding costs. This efficient inventory management directly contributes to cost savings, as materials are ordered based on actual production needs rather than outdated forecasts.
3. Enhanced Forecasting and Demand Planning
In chemical manufacturing, demand planning can be highly unpredictable due to market fluctuations, seasonal variations, and regulatory impacts. ERP integration with PlanetTogether provides production schedulers with real-time access to sales forecasts, market trends, and customer demands, allowing them to adjust production schedules accordingly.
Improved forecasting capabilities not only help schedulers respond to changing market demands but also prevent excessive buildup of inventory, which is particularly important in an industry where raw materials can be expensive and difficult to store. This proactive approach helps reduce waste, lower costs, and ensure that production aligns closely with actual demand.
4. Reduction in Lead Times and Downtime
For chemical manufacturing facilities, unplanned downtime is costly, both in terms of lost productivity and the expenses associated with restarting complex chemical processes. PlanetTogether’s predictive analytics, when integrated with ERP systems, enables production schedulers to anticipate maintenance needs and schedule preventive measures at opportune times.
By incorporating equipment health data from ERP systems, schedulers can align maintenance schedules with production cycles, minimizing downtime. This approach not only reduces lead times but also lowers maintenance costs by preventing equipment breakdowns that could halt production.
5. Enhanced Regulatory Compliance and Safety Standards
The chemical industry operates under stringent regulatory requirements. ERP integration with PlanetTogether provides production schedulers with access to compliance data, safety protocols, and environmental regulations, enabling them to ensure that production schedules align with these requirements.
Schedulers can monitor batch production data and traceability in real time, quickly addressing any compliance issues that may arise. This integration is crucial in preventing costly regulatory fines, maintaining product quality, and ensuring safe working conditions—factors that collectively contribute to cost savings and operational efficiency.
Best Practices for Production Schedulers Using PlanetTogether Integration
For production schedulers looking to leverage the benefits of PlanetTogether integration, consider these best practices:
Leverage Real-Time Data for Proactive Scheduling: Use real-time insights to anticipate and respond to fluctuations in demand and resource availability, minimizing bottlenecks and avoiding costly delays.
Prioritize Preventive Maintenance: Schedule maintenance during low-demand periods to prevent unplanned downtime, thereby preserving equipment longevity and reducing repair costs.
Implement Scenario Planning for Better Decision-Making: Scenario planning allows schedulers to test different production scenarios and anticipate potential disruptions, leading to faster and more informed decision-making.
Use Analytics to Identify and Eliminate Inefficiencies: With access to analytics and performance metrics, schedulers can identify trends and areas for improvement, further enhancing operational efficiency.
Collaborate Across Departments for Cohesive Planning: Foster interdepartmental collaboration by sharing data insights across production, procurement, and supply chain teams. This shared approach enhances alignment and ensures that all departments work toward common goals.
As the chemical industry moves toward greater digitization, the integration of AI and machine learning with PlanetTogether and ERP systems will offer even more sophisticated tools for production scheduling. Machine learning algorithms could help predict demand patterns, optimize scheduling even further, and allow for hyper-responsive scheduling adjustments. These advancements represent an exciting opportunity for production schedulers to gain deeper insights and refine their scheduling practices.
For production schedulers in chemical manufacturing, integrating PlanetTogether with leading ERP systems like SAP, Oracle, Microsoft Dynamics, Kinaxis, or Aveva offers a competitive advantage in improving operational efficiency and reducing costs. By optimizing resource allocation, improving inventory management, and enhancing demand forecasting, production schedulers can drive both productivity and profitability.
In an industry where time, resources, and regulatory compliance are of the essence, this integration empowers schedulers to operate with agility and precision, ensuring that their facilities meet evolving demands efficiently and cost-effectively.
Through real-time insights and automated scheduling adjustments, PlanetTogether integration represents a transformative step in the journey toward operational excellence, positioning chemical manufacturers for sustainable growth and a stronger competitive edge in today’s dynamic market.
Are you ready to take your manufacturing operations to the next level? Contact us today to learn more about how PlanetTogether can help you achieve your goals and drive success in your industry.