Heavy Equipment Manufacturing: Flow Shop Scheduling with Parallel Machines and Sequence-dependent Setup Times
In the realm of heavy equipment manufacturing, where efficiency and precision are essential, the role of a Production Scheduler is pivotal. A Production Scheduler orchestrates the intricate dance of machinery, materials, and manpower to ensure seamless operations and timely deliveries. However, the complexities inherent in this industry, such as parallel machines and sequence-dependent setup times, pose unique challenges to scheduling processes.
In this blog, we look into the world of flow shop scheduling within heavy equipment manufacturing, focusing on managing parallel machines and sequence-dependent setup times. Additionally, we explore how integrating advanced scheduling software like PlanetTogether with leading ERP, SCM, and MES systems can revolutionize production planning and execution.
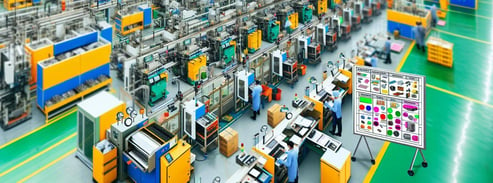
Understanding Flow Shop Scheduling
Flow shop scheduling involves arranging a series of operations (tasks) in a predetermined sequence across multiple machines or workstations. In heavy equipment manufacturing, where the assembly process often follows a linear flow, optimizing this sequence is crucial for minimizing idle time and maximizing throughput.
However, the presence of parallel machines introduces additional complexity. Instead of a linear progression, operations can occur simultaneously on different machines, offering opportunities for parallel processing but requiring careful coordination to avoid bottlenecks and resource conflicts.
Moreover, sequence-dependent setup times further complicate scheduling. These setup times vary depending on the sequence of tasks, necessitating strategic sequencing to minimize downtime and changeover costs.
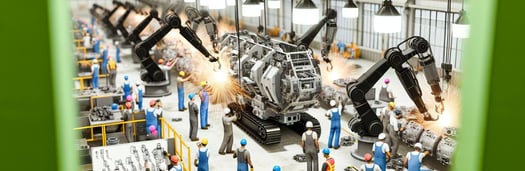
Challenges in Heavy Equipment Manufacturing
Heavy equipment manufacturing encompasses a diverse range of products, from construction machinery to agricultural equipment, each with its own unique manufacturing requirements. Common challenges faced by production schedulers in this industry include:
Variability in Production Processes: Heavy equipment manufacturing often involves customizations or variations in product configurations, leading to unpredictable production times and resource requirements.
Resource Constraints: Limited availability of machinery, skilled labor, and raw materials can constrain production capacity, making efficient resource allocation a critical concern.
Maintenance and Downtime: Scheduled maintenance, unexpected breakdowns, and changeovers contribute to downtime, disrupting production schedules and reducing overall efficiency.
Supply Chain Dynamics: Dependencies on suppliers for critical components and materials introduce supply chain risks, necessitating real-time visibility and proactive management.
Addressing these challenges requires a comprehensive approach to production scheduling, leveraging advanced techniques and technologies to optimize operations.
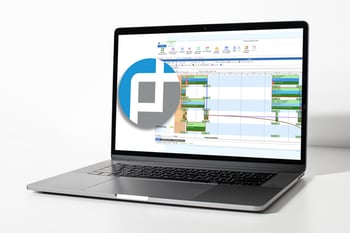
Integration of PlanetTogether with ERP, SCM, and MES Systems
Effective production scheduling relies on seamless integration between scheduling software and enterprise systems such as ERP (Enterprise Resource Planning), SCM (Supply Chain Management), and MES (Manufacturing Execution Systems). Among the leading software solutions in this space are SAP, Oracle, Microsoft Dynamics, Kinaxis, and Aveva.
PlanetTogether, a robust production planning and scheduling software, offers powerful capabilities for optimizing flow shop scheduling in heavy equipment manufacturing. By integrating with ERP, SCM, and MES systems, PlanetTogether enables end-to-end visibility and control across the production lifecycle.
-May-08-2024-04-36-12-8483-PM.png?width=313&height=50&name=logo%20(2)-May-08-2024-04-36-12-8483-PM.png)
Key Benefits of Integrating PlanetTogether with ERP, SCM, and MES Systems
Real-Time Data Exchange: Integration facilitates the seamless exchange of data between scheduling software and enterprise systems, ensuring that schedules are based on the latest information regarding orders, inventory levels, and resource availability.
Dynamic Resource Allocation: With real-time visibility into resource utilization and availability, production schedulers can dynamically allocate resources based on changing demand, priorities, and constraints.
Improved Decision-Making: By leveraging data analytics and predictive modeling, integrated systems empower production schedulers to make informed decisions regarding scheduling, capacity planning, and inventory management.
Enhanced Collaboration: Integration fosters collaboration between different functional areas within the organization, enabling cross-functional teams to align on production priorities and resolve issues proactively.
Adaptive Scheduling: PlanetTogether's advanced algorithms can dynamically adjust schedules in response to changes in demand, resource availability, or production constraints, ensuring optimal utilization of resources and minimizing disruptions.
Flow shop scheduling with parallel machines and sequence-dependent setup times poses significant challenges in heavy equipment manufacturing. However, by leveraging advanced scheduling software like PlanetTogether and integrating it with leading ERP, SCM, and MES systems, production schedulers can optimize operations, improve efficiency, and meet customer demands with agility.
In an industry where every minute counts, the ability to orchestrate complex production processes with precision is a competitive advantage that can drive success in heavy equipment manufacturing. By embracing integrated scheduling solutions, companies can unlock new levels of productivity, agility, and profitability in their manufacturing operations.
Are you ready to take your manufacturing operations to the next level? Contact us today to learn more about how PlanetTogether can help you achieve your goals and drive success in your industry.
LEAVE A COMMENT