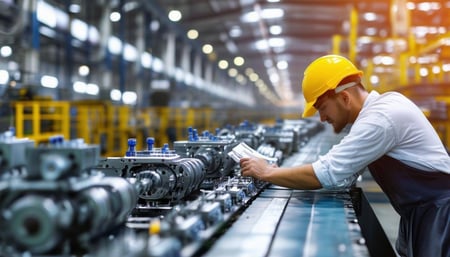
Implementing Lean Manufacturing Principles for Production Schedulers
As production demands in packaging manufacturing continue to rise, the role of a Production Scheduler becomes increasingly crucial. The scheduling process is a challenging endeavor, often requiring meticulous planning to ensure that materials, labor, and equipment are allocated effectively.
With the lean manufacturing philosophy gaining traction across industries, Production Schedulers are now turning to lean principles to enhance productivity, reduce waste, and streamline processes. Integrating scheduling software like PlanetTogether with systems such as SAP, Oracle, Microsoft, Kinaxis, or Aveva can be the catalyst for adopting lean principles, empowering production teams to achieve sustainable improvements.
In this blog, we’ll explore how Production Schedulers can implement lean manufacturing principles in packaging facilities and how integration with platforms like PlanetTogether helps manage the complexities of lean initiatives effectively.
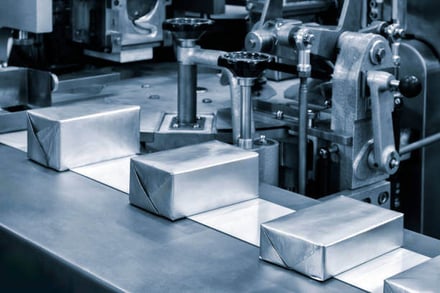
Lean Manufacturing in Packaging Manufacturing
Lean manufacturing is based on principles aimed at eliminating waste, enhancing efficiency, and delivering value from the customer’s perspective. For packaging manufacturing, lean practices can lead to reduced lead times, minimized inventory, and streamlined workflows. Implementing these practices requires a cultural shift toward continuous improvement and a structured approach to operations, often involving just-in-time (JIT) inventory, 5S organization, and kanban systems to regulate production flow.
However, for Production Schedulers, applying lean manufacturing principles can be particularly challenging. Managing multiple production lines, balancing shifts, adjusting for machine maintenance, and responding to customer demand shifts all demand a robust approach. Here is where technology integrations come into play.

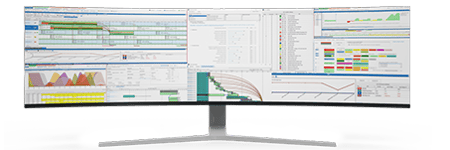
The Role of Technology Integration in Lean Implementation
To adopt lean practices successfully, production teams need to leverage real-time data for better decision-making. Integrating PlanetTogether with ERP and APS systems such as SAP, Oracle, Microsoft, Kinaxis, or Aveva helps synchronize workflows, identify bottlenecks, and automate repetitive scheduling tasks, all essential for a lean environment.
Key Benefits of Integration
Enhanced Visibility: PlanetTogether, when integrated with SAP or Oracle, consolidates data from multiple systems, providing Production Schedulers with a single view of production status. This real-time visibility helps identify where waste is occurring, be it excess inventory, idle machines, or unnecessary motion.
Efficient Resource Utilization: By connecting PlanetTogether with ERP systems, schedulers can optimize resource allocation in line with lean’s JIT principles. Integrated systems help Production Schedulers anticipate demand fluctuations and adapt schedules accordingly, ensuring minimal waste and maximal efficiency.
Streamlined Communication and Collaboration: Integration with Microsoft tools enables seamless communication and task tracking, ensuring that cross-functional teams remain aligned on lean goals. Alerts, notifications, and dashboards make it easier for teams to stay informed of changes in real-time.
Advanced Analytics for Continuous Improvement: Integrating with Kinaxis or Aveva enhances PlanetTogether’s analytical capabilities, allowing production teams to identify trends, monitor key performance indicators (KPIs), and continuously improve processes. This fosters a data-driven approach to lean, ensuring that changes are measured and optimized.
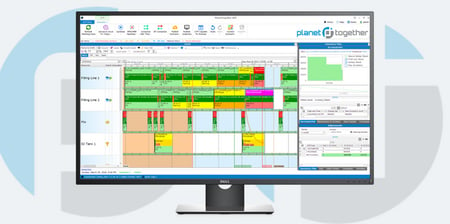
Implementing Lean Manufacturing Principles with PlanetTogether
Once integration is established, implementing lean manufacturing becomes a structured and feasible process. Below are steps a Production Scheduler in packaging manufacturing can take to integrate lean principles effectively using PlanetTogether with ERP and APS systems.
Value Stream Mapping (VSM)
Value stream mapping is essential in lean manufacturing as it visually represents the production flow, identifying both value-added and non-value-added activities. With PlanetTogether, schedulers can utilize data from ERP systems like SAP or Oracle to analyze each step of the packaging process, from raw materials to finished goods.
Action Steps:
Use data integration to create detailed maps of your production workflows.
Identify bottlenecks and waste-prone areas.
Align schedules to streamline these workflows, minimizing delays and non-essential activities.
By mapping out the value stream and linking it to real-time data, Production Schedulers can eliminate redundant steps, shortening lead times and maximizing efficiency.
Implement Just-in-Time (JIT) Scheduling
JIT is a core principle of lean manufacturing, ensuring materials and products are delivered as needed. Integrating PlanetTogether with ERP systems like SAP allows schedulers to predict and adjust for demand fluctuations accurately, reducing inventory levels without risking shortages.
Action Steps:
Analyze production demand data from your ERP system to schedule production as close to order fulfillment as possible.
Use PlanetTogether’s scheduling algorithms to optimize material flow and limit excess inventory.
Collaborate with procurement teams to align supply orders with production needs, reducing the need for storage and minimizing waste.
With JIT scheduling, Production Schedulers can maintain a lean inventory, directly contributing to reduced storage costs and quicker response times.
Optimize Production through 5S Methodology
The 5S methodology (Sort, Set in order, Shine, Standardize, Sustain) promotes an organized and efficient workspace. Integrating PlanetTogether with Microsoft tools, like Teams and SharePoint, allows teams to document and standardize scheduling procedures, promoting consistency across shifts and production lines.
Action Steps:
Standardize scheduling practices within PlanetTogether and document these standards for the team.
Establish a digital “command center” within Microsoft Teams to monitor and communicate schedule changes.
Regularly review and sustain these practices, ensuring adherence to lean principles.
With the 5S methodology in place, packaging facilities can reduce downtime caused by disorganization and improve response times to unexpected disruptions.
Implement Kanban for Workload Balancing
Kanban systems help balance workloads and prevent overproduction, aligning with lean’s focus on demand-driven production. Integrated with systems like Aveva, PlanetTogether can support electronic kanban boards that visualize production stages, enabling schedulers to balance workloads across lines and shifts effectively.
Action Steps:
Use kanban boards within PlanetTogether to track progress and identify bottlenecks.
Integrate kanban boards with your ERP to ensure accurate tracking of material availability and machine status.
Adjust production schedules dynamically based on kanban signals, ensuring efficient flow from one process to the next.
Using kanban boards in conjunction with scheduling software makes it easier to avoid overproduction and excess inventory, two primary sources of waste in lean manufacturing.
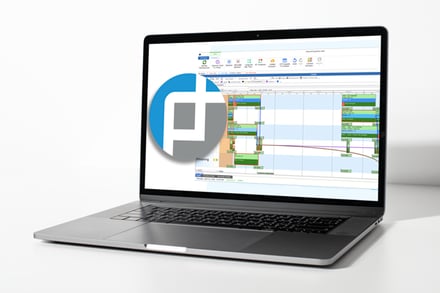
Overcoming Common Lean Implementation Challenges with PlanetTogether Integration
While lean principles provide a roadmap for efficiency, implementing them in a real-world setting involves certain challenges. Integrated platforms like PlanetTogether can address some common hurdles:
Challenge 1: Resistance to Change
Change can be challenging for teams accustomed to traditional processes. By integrating with familiar ERP systems like SAP or Microsoft, PlanetTogether makes it easier to transition to lean practices, providing users with familiar interfaces and a smoother adoption process.
Challenge 2: Balancing Lean with Flexibility
Lean manufacturing requires tight scheduling, which can sometimes limit flexibility. Integration with advanced APS systems such as Kinaxis allows PlanetTogether to offer predictive insights, enabling Production Schedulers to remain flexible and responsive to last-minute changes.
Challenge 3: Measuring the Impact of Lean
Continuous improvement requires measurable KPIs. Integrated analytics tools provide production teams with valuable metrics, helping to track improvements in waste reduction, downtime, and lead times. These insights allow schedulers to make data-driven decisions that align with lean principles.
The Long-Term Benefits of Lean Implementation
For a Production Scheduler in packaging manufacturing, adopting lean manufacturing principles with the support of integrated systems like PlanetTogether and ERP/APS platforms leads to lasting benefits:
Reduced Waste: Lean principles focus on eliminating unnecessary steps and materials, ultimately cutting costs.
Increased Productivity: Streamlined processes mean quicker turnaround times, allowing schedulers to maximize machine utilization and workforce efficiency.
Improved Customer Satisfaction: With shorter lead times and more reliable production, facilities can meet customer demands more effectively.
For packaging manufacturing facilities, lean manufacturing represents a path toward sustainable productivity and reduced operational costs. Production Schedulers are instrumental in this journey, managing the complexities of scheduling in alignment with lean principles. By leveraging PlanetTogether’s scheduling capabilities in tandem with ERP and APS systems such as SAP, Oracle, Microsoft, Kinaxis, or Aveva, schedulers can bring lean principles to life in a practical, measurable way.
The integration enables real-time data access, advanced analytics, and streamlined workflows—tools essential for eliminating waste, reducing lead times, and achieving continuous improvement. Embracing lean manufacturing with the right technology integration is not just an operational upgrade; it’s a strategic transformation that positions packaging manufacturers for future success.
Are you ready to take your manufacturing operations to the next level? Contact us today to learn more about how PlanetTogether and integrated scheduling solutions can help you achieve your sustainability goals and drive success.