Implementing Industrial IoT in Packaging Manufacturing
The integration of Industrial Internet of Things (IIoT) has become a turning point, especially for Production Planners looking to achieve more efficiency, precision, and transparency. The modern packaging plant, with its intricate coordination of machines, materials, and labor, demands a data-driven approach that IIoT enables. When combined with advanced planning tools like PlanetTogether integrated with ERP systems like SAP, Oracle, Microsoft, Kinaxis, or Aveva, IIoT can empower Production Planners to achieve unprecedented levels of productivity, predictability, and efficiency.
This blog outlines the benefits of implementing IIoT in packaging manufacturing, the steps involved, and the role that integrated systems like PlanetTogether play in enabling a seamless IIoT-driven environment.
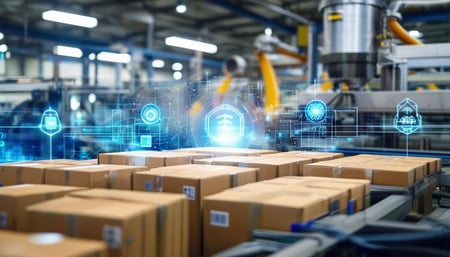
Industrial IoT in Packaging Manufacturing
Industrial IoT refers to the interconnectivity of machines, sensors, and devices within industrial environments, enabling real-time data collection, analysis, and action. In packaging manufacturing, IIoT leverages sensors and connected devices on equipment such as filling machines, labeling stations, and conveyor systems to collect valuable production data. This data can include machine performance, material flow rates, energy usage, and downtime events.
IIoT offers actionable insights, such as predicting when a machine might fail, monitoring production quality in real-time, or automatically adjusting production schedules based on real-time inventory levels. However, to fully harness these benefits, IIoT needs to work in tandem with planning and ERP systems to create a cohesive, data-driven production environment.
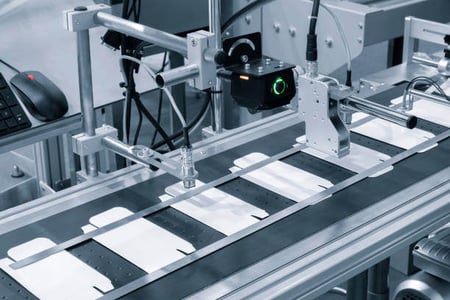
Benefits of IIoT for Production Planners in Packaging Manufacturing
For Production Planners, the adoption of IIoT brings multiple operational advantages:
Enhanced Predictive Maintenance
With IIoT-enabled sensors on critical machinery, maintenance needs can be anticipated, reducing unexpected downtime. Predictive maintenance allows Production Planners to adjust schedules proactively, ensuring uninterrupted production flow and minimal disruptions.
Real-Time Data Access and Transparency
IIoT provides real-time visibility into production metrics, inventory levels, and machine statuses. This transparency allows planners to monitor progress and make on-the-fly adjustments, aligning production schedules with actual factory floor conditions.
Improved Resource Allocation
By tracking machine and labor productivity data in real-time, Production Planners can make data-backed decisions to optimize resource allocation. For instance, if one line is running below capacity, planners can adjust schedules to balance workloads more effectively across production lines.
Quality Control and Traceability
IIoT can monitor quality in real-time, detecting defects as they occur. This ensures that only quality products move forward, reducing rework and waste. Additionally, traceability features in IIoT systems allow planners to track issues back to their source, making continuous improvement easier to implement.
Energy Efficiency
Many IIoT systems provide insights into energy consumption, which helps in identifying areas for reduction. Production Planners can then schedule energy-intensive tasks for off-peak hours or optimize production methods to lower energy costs.

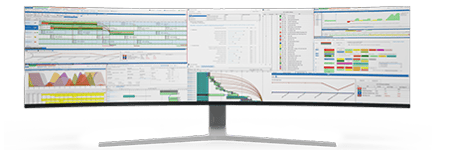
Integrating IIoT with PlanetTogether and ERP Systems
To unlock the full potential of IIoT in packaging manufacturing, integration with a robust Advanced Planning and Scheduling (APS) system like PlanetTogether is crucial. PlanetTogether, when linked with ERP systems such as SAP, Oracle, Microsoft, Kinaxis, or Aveva, offers a holistic view of production planning, scheduling, and execution. Let’s break down the integration benefits and how IIoT enhances these systems:
Synchronized Planning and Real-Time Adjustments
With IIoT data feeding directly into PlanetTogether, Production Planners gain a real-time, centralized view of production. For example, if a sensor detects an anomaly in a machine, PlanetTogether can adjust schedules and workflows to avoid bottlenecks or delays. When integrated with ERP, these adjustments are reflected in the broader supply chain, enabling seamless material and inventory management.
Automated Decision-Making
Integrated IIoT systems can automate routine decisions. For instance, if IIoT sensors detect low material levels, they can automatically trigger a replenishment request in the ERP system. PlanetTogether then adjusts the schedule accordingly to avoid a halt in production. Such automation minimizes human intervention and reduces delays, allowing planners to focus on more strategic tasks.
Enhanced Data Analytics and Reporting
The wealth of data from IIoT systems provides a foundation for advanced analytics. Through PlanetTogether’s integration with ERP, Production Planners can access detailed reports on cycle times, throughput, and yield variations. These insights facilitate better decision-making, whether it’s about optimizing resource usage or identifying areas for process improvements.
Adaptive Scheduling Based on Real-Time Conditions
In dynamic environments like packaging, unexpected events such as machine failures or urgent orders are common. With IIoT providing real-time insights, PlanetTogether can adapt schedules based on immediate conditions, while ERP integration ensures that materials and inventory align with the new plan. This adaptability helps Production Planners maintain agility without compromising efficiency.
Improved Communication Across Departments
Integration between IIoT, PlanetTogether, and ERP promotes seamless communication across teams, from production and maintenance to procurement and logistics. For instance, if production is running ahead of schedule, the ERP system can notify the procurement team to adjust material delivery dates. Similarly, the maintenance team can access IIoT-driven maintenance alerts through the same interface, ensuring that all teams work in unison.
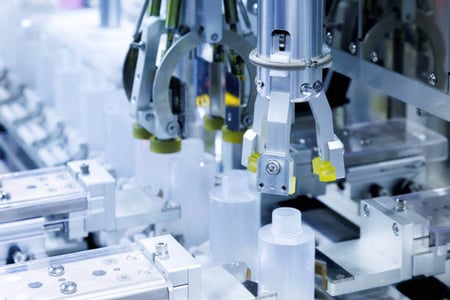
Steps to Successfully Implement IIoT in Packaging Manufacturing
Implementing IIoT in a packaging facility requires a clear, phased approach. Here’s a guide to ensure a smooth transition:
Step 1: Define Objectives and KPIs
Before implementation, it’s essential to establish clear goals for IIoT deployment. For example, are you looking to reduce machine downtime, enhance scheduling accuracy, or improve product quality? Setting Key Performance Indicators (KPIs) helps measure success and ensures alignment with broader business objectives.
Step 2: Assess Equipment Compatibility
Not all machinery in packaging facilities may be compatible with IIoT sensors. Conduct an assessment to identify which equipment can be retrofitted with sensors. This step helps Production Planners understand the scope of the implementation and allows for accurate budgeting.
Step 3: Select the Right IIoT Platform and Integrate with PlanetTogether
Choose an IIoT platform that aligns with the unique needs of packaging manufacturing. When selecting an IIoT provider, consider compatibility with PlanetTogether and ERP systems like SAP, Oracle, Microsoft, Kinaxis, or Aveva. A seamless integration across these platforms ensures that data flows smoothly, enhancing scheduling, planning, and real-time adjustments.
Step 4: Implement a Pilot Project
Start with a pilot project on a single production line or equipment to test IIoT capabilities. This approach allows you to evaluate the system's performance, identify any issues, and fine-tune configurations before full-scale implementation. During the pilot, focus on data accuracy, response times, and system interoperability with PlanetTogether and ERP.
Step 5: Train Staff and Foster a Data-Driven Culture
For IIoT to succeed, Production Planners, machine operators, and maintenance personnel need to understand how to use the system. Training staff on IIoT usage and encouraging a data-driven culture are crucial for gaining buy-in. Teams should understand how IIoT will benefit their roles, improve productivity, and make their workflows more efficient.
Step 6: Scale and Continuously Improve
After a successful pilot, scale IIoT across the facility. Regularly monitor performance against KPIs and gather feedback from stakeholders. With an iterative approach, Production Planners can continuously improve processes, incorporating new data insights into planning and scheduling.
Challenges to Consider
While IIoT offers numerous advantages, there are some challenges to address:
Data Overload: The sheer volume of data generated can overwhelm users. Leveraging an APS like PlanetTogether, which filters and prioritizes data, can help mitigate this issue.
Cybersecurity Risks: IIoT introduces potential vulnerabilities in the network. Implementing robust security protocols is critical to protect sensitive production data.
Integration Complexities: Integrating IIoT with existing systems may require custom configurations, especially in legacy setups. Working with experienced vendors and integration specialists can ease this process.
For Production Planners in packaging manufacturing, IIoT presents an opportunity to transition from reactive to proactive planning, improving productivity, reducing waste, and enhancing quality. By integrating IIoT with planning systems like PlanetTogether and ERP solutions like SAP, Oracle, Microsoft, Kinaxis, or Aveva, the benefits of IIoT become even more substantial.
Embracing IIoT is not just a technological upgrade; it’s a strategic imperative. When implemented thoughtfully, with a clear focus on goals and integration, IIoT can transform packaging manufacturing, allowing Production Planners to meet the demands of modern manufacturing with agility and precision.
Are you ready to take your manufacturing operations to the next level? Contact us today to learn more about how PlanetTogether can help you achieve your goals and drive success in your industry.