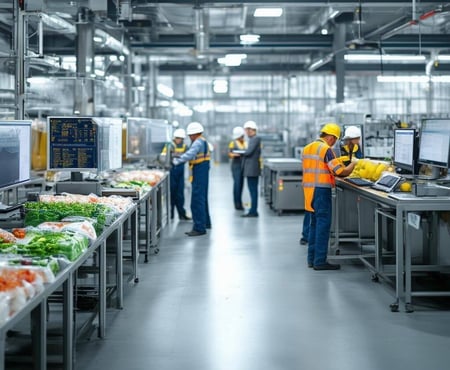
Implementing Compliance in Food and Beverage Manufacturing
In the highly regulated world of food and beverage manufacturing, compliance isn't just a matter of avoiding fines—it's a cornerstone of trust with customers and partners. As a Purchasing Manager, you play a pivotal role in ensuring that procurement practices align with stringent regulatory requirements, from sourcing high-quality materials to verifying supplier credentials. Implementing compliance in your purchasing processes can feel daunting, but with the right tools and strategies, it becomes a manageable and even value-adding endeavor.
One such approach is leveraging advanced manufacturing and supply chain solutions like PlanetTogether integrated with enterprise systems such as SAP, Oracle, Microsoft Dynamics, Kinaxis, or Aveva. This combination provides the transparency and control necessary to streamline compliance efforts while maintaining operational efficiency.
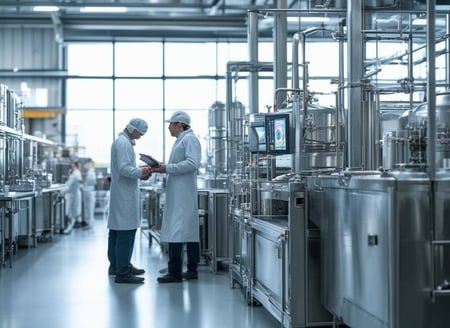
The Importance of Compliance in Food and Beverage Manufacturing
Food and beverage manufacturing is subject to numerous regulations designed to ensure product safety, quality, and sustainability. These may include:
Food Safety Modernization Act (FSMA) in the U.S.
ISO 22000 for food safety management systems.
Hazard Analysis Critical Control Point (HACCP) requirements.
Global Food Safety Initiative (GFSI) standards.
Non-compliance can lead to severe consequences, including product recalls, damaged brand reputation, and financial penalties. However, compliance isn’t merely about avoiding negatives; it can create a competitive advantage. Certifications and audits often act as trust signals to consumers and B2B partners alike.
As a Purchasing Manager, your role is crucial in ensuring that every ingredient and material sourced meets these regulations, from selecting certified suppliers to maintaining thorough documentation for audits.
Key Challenges in Compliance for Purchasing Managers
While compliance is essential, implementing it can be fraught with challenges:
Supplier Transparency: Verifying that suppliers adhere to regulatory standards can be complex, especially with a global supply chain.
Traceability: Ensuring full traceability of raw materials from origin to production is critical but resource-intensive.
Documentation: Maintaining up-to-date and easily accessible records for audits requires robust systems.
Cost Management: Balancing compliance with cost-efficiency can feel like a tightrope walk.
These challenges underscore the need for integrated solutions that streamline compliance while optimizing procurement practices.

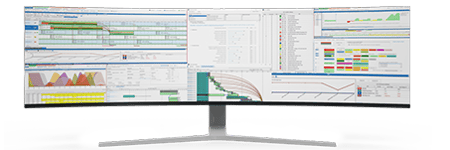
Leveraging Technology for Compliance: PlanetTogether and ERP Integration
To overcome these challenges, many food and beverage manufacturers turn to software solutions like PlanetTogether. When integrated with enterprise systems such as SAP, Oracle, Microsoft Dynamics, Kinaxis, or Aveva, PlanetTogether can revolutionize compliance management in procurement.
Enhanced Supplier Management
Integrated systems enable real-time tracking of supplier compliance. Through PlanetTogether, you can set up automatic alerts for certifications, audits, and expiration dates, ensuring you only source from approved suppliers. Integration with SAP or Oracle can extend these capabilities, pulling in supplier data and audit reports to provide a centralized view of compliance metrics.
Traceability Across the Supply Chain
With PlanetTogether and ERP integration, you can achieve end-to-end traceability for raw materials. For example:
Microsoft Dynamics can log every purchase order and track materials as they move through the supply chain.
PlanetTogether uses this data to ensure traceability during production scheduling, creating a digital trail that satisfies auditors and regulators.
Automated Compliance Documentation
One of the most time-consuming aspects of compliance is managing documentation. By integrating PlanetTogether with systems like Aveva, you can automate the creation and storage of compliance records. This ensures that every purchase and production activity is documented, reducing the risk of missing critical data during audits.
Cost-Effective Compliance
While compliance often involves additional costs, integrated systems can help you minimize these expenses. For example:
Kinaxis can model supply chain scenarios to identify cost-effective compliant suppliers.
PlanetTogether can use this data to optimize production schedules around those suppliers, ensuring minimal disruption.
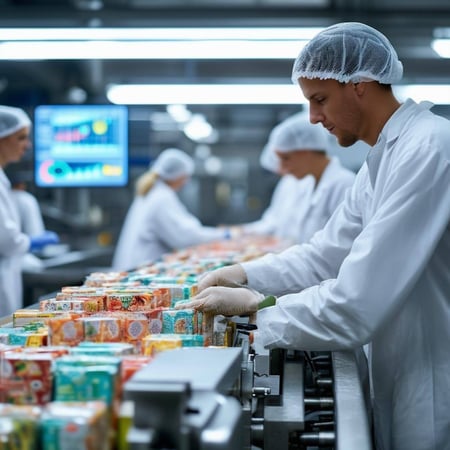
Benefits of Compliance Beyond Regulation
Compliance isn’t just a regulatory checkbox; it’s a strategic advantage. By implementing robust compliance processes, you can:
Enhance Brand Reputation: Consumers and partners are more likely to trust a brand with visible commitments to quality and safety.
Improve Supplier Relationships: Clear compliance requirements foster transparency and accountability in supplier partnerships.
Reduce Risk: Full traceability and documentation minimize the risk of product recalls or regulatory penalties.
Boost Efficiency: Integrated systems reduce manual processes, allowing your team to focus on strategic procurement.
For Purchasing Managers in food and beverage manufacturing, compliance is more than a regulatory necessity—it’s a strategic priority. By integrating tools like PlanetTogether with ERP systems such as SAP, Oracle, Microsoft Dynamics, Kinaxis, or Aveva, you can transform compliance from a burden into a streamlined, value-adding process.
The benefits are clear: enhanced supplier management, full traceability, automated documentation, and cost-effective compliance. With the right approach, you can ensure your procurement practices not only meet regulatory standards but also contribute to your company’s overall success.
By embracing these technologies, you’re not just managing compliance—you’re setting your organization up for long-term growth and resilience in a demanding industry.
Are you ready to take your manufacturing operations to the next level? Contact us today to learn more about how PlanetTogether can help you achieve your goals and drive success in your industry.
LEAVE A COMMENT