Human-Centric Automation Design: Enhancing Worker Safety and Productivity
Optimizing operations is not just about maximizing output and efficiency in chemical manufacturing—it's also about prioritizing the safety and well-being of the workforce. As a Plant Manager, you're constantly seeking innovative solutions to streamline processes while safeguarding your team.
In this blog, we look into the concept of human-centric automation design and its pivotal role in revolutionizing safety and productivity in chemical manufacturing facilities.
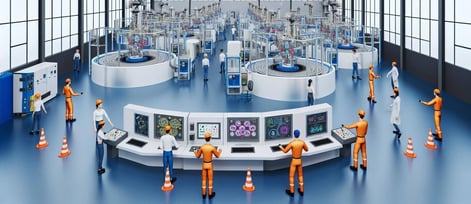
Human-Centric Automation Design
Human-centric automation design is a paradigm shift in industrial engineering that places the human operator at the center of technological advancements. It goes beyond mere efficiency gains to encompass the holistic enhancement of worker experience, safety, and productivity. By leveraging cutting-edge technologies and intuitive interfaces, human-centric automation empowers employees to work smarter, safer, and more efficiently.
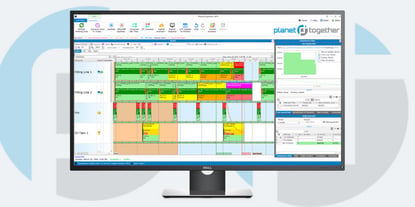
The Integration Imperative: PlanetTogether and ERP/SCM/MES Systems
At the heart of human-centric automation lies seamless integration between advanced planning and scheduling (APS) solutions like PlanetTogether and enterprise resource planning (ERP), supply chain management (SCM), and manufacturing execution systems (MES) such as SAP, Oracle, Microsoft, Kinaxis, and Aveva. This integration ensures real-time visibility, data synchronization, and streamlined communication across all levels of the manufacturing hierarchy.
Benefits of Integration
Enhanced Decision-Making: By consolidating data from disparate systems into a unified platform, Plant Managers gain comprehensive insights into production schedules, inventory levels, and resource allocation. This facilitates data-driven decision-making and enables proactive risk management.
Optimized Resource Utilization: Integration between APS and ERP/SCM/MES systems enables dynamic resource allocation based on real-time demand fluctuations and production constraints. This leads to optimized utilization of manpower, equipment, and raw materials, thereby maximizing operational efficiency.
Improved Workflow Efficiency: With automated data exchange and synchronization, manual data entry errors and processing delays are minimized. This results in smoother workflows, reduced lead times, and enhanced throughput, ultimately boosting productivity across the manufacturing floor.
Agile Adaptation to Changes: In today's volatile market landscape, agility is paramount. Integrated systems enable rapid adaptation to changing market dynamics, customer demands, and regulatory requirements, ensuring that the manufacturing facility remains resilient and competitive.
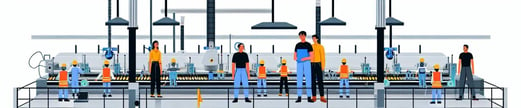
Human-Centric Design Principles
User-Centric Interface: The user interface of automation systems should be intuitive, ergonomic, and user-friendly. Clear visualizations, contextual prompts, and customizable dashboards empower operators to interact seamlessly with the technology, minimizing cognitive load and enhancing usability.
Predictive Analytics and AI: Leveraging advanced analytics and artificial intelligence (AI), human-centric automation anticipates potential safety hazards, production bottlenecks, and quality deviations. Predictive insights enable preemptive interventions, ensuring proactive risk mitigation and operational continuity.
Collaborative Work Environment: Automation should complement human expertise rather than replace it. Interactive collaboration tools and real-time communication channels foster teamwork and knowledge sharing among operators, engineers, and management, creating a culture of continuous improvement and innovation.
Emphasis on Safety and Ergonomics: Safety is non-negotiable in chemical manufacturing. Human-centric automation prioritizes ergonomic design, hazard identification, and safety protocols to minimize the risk of accidents and occupational hazards. From ergonomic workstations to predictive maintenance algorithms, every aspect of the system is engineered to safeguard employee well-being.
In the quest for operational excellence, prioritizing human-centric automation design is not just a strategic imperative—it's a moral obligation. By placing the safety, well-being, and empowerment of employees at the forefront, chemical manufacturing facilities can achieve unprecedented levels of productivity, efficiency, and resilience.
Through seamless integration between advanced planning and scheduling solutions like PlanetTogether and ERP/SCM/MES systems, Plant Managers can pave the way for a future where technology serves humanity, rather than the other way around.
It's time to embrace the era of human-centric automation and redefine the future of chemical manufacturing. Are you ready to take your manufacturing operations to the next level? Contact us today to learn more about how PlanetTogether can help you achieve your goals and drive success in your industry.