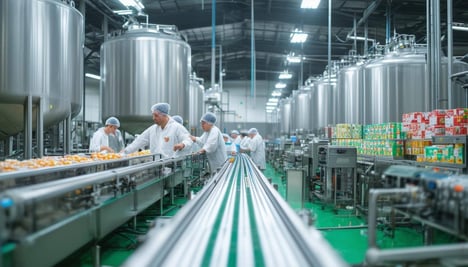
How Industry Standards Influence Production Schedules in Food and Beverage Manufacturing
In the food and beverage manufacturing industry, maintaining operational excellence while meeting stringent industry standards is an ongoing challenge. From regulatory compliance to sustainability goals, these standards significantly influence how production planners design and execute schedules. This complexity is further magnified when integrated systems like PlanetTogether work alongside enterprise resource planning (ERP) solutions like SAP, Oracle, Microsoft Dynamics, Kinaxis, or Aveva to drive efficiency and compliance.
This blog explores how industry standards shape production scheduling and highlights the critical role of system integration in streamlining operations.
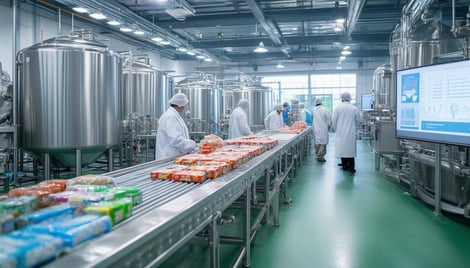
The Importance of Industry Standards in Food and Beverage Manufacturing
Industry standards in food and beverage manufacturing encompass a wide range of regulations, guidelines, and best practices. These standards serve as benchmarks for ensuring quality, safety, and sustainability, and compliance is non-negotiable for manufacturers looking to maintain their reputation and market position. Some of the most critical standards include:
Food Safety Standards: Compliance with standards like the FDA's Food Safety Modernization Act (FSMA) or the Global Food Safety Initiative (GFSI) is essential to avoid product recalls and protect public health.
Sustainability Goals: Increasingly, manufacturers are adopting practices aligned with environmental standards to reduce their carbon footprint and minimize waste.
Consumer Preferences: Adapting to certifications like organic, non-GMO, or fair trade often influences production timelines and batch sizes.
Each of these standards imposes specific constraints on production schedules, from raw material procurement to final product delivery.
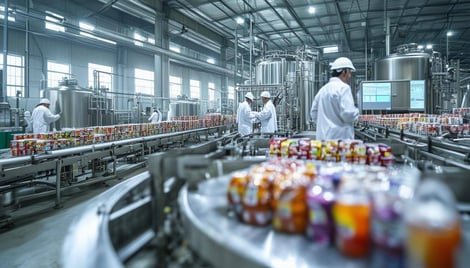
How Industry Standards Shape Production Schedules
Production planners are at the heart of ensuring that industry standards are seamlessly incorporated into the manufacturing process. Here’s how these standards influence production schedules:
Traceability and Documentation
Challenge: Meeting traceability requirements often involves tracking every step of the production process, from sourcing raw materials to distributing finished products.
Solution: Integrated systems like PlanetTogether and SAP can automate the capture and storage of production data, ensuring comprehensive documentation while reducing manual errors.
Batch Management
Challenge: Producing goods in compliance with standards such as allergen-free or organic certification requires strict segregation of production batches.
Solution: Advanced scheduling tools like PlanetTogether allow planners to segment production runs efficiently, ensuring compliance without disrupting timelines.
Quality Control
Challenge: Standards like HACCP (Hazard Analysis and Critical Control Points) require quality checks at various stages of production.
Solution: By integrating PlanetTogether with an ERP system like Oracle, planners can schedule quality control activities into production timelines, minimizing downtime.
Sustainability Metrics
Challenge: Adhering to environmental standards may necessitate adjustments in energy usage, waste disposal, or packaging processes.
Solution: Systems integration between PlanetTogether and Microsoft Dynamics can optimize resource allocation, reducing waste and improving energy efficiency.

The Role of System Integration in Meeting Standards
To navigate the complexities of industry standards, seamless integration between PlanetTogether and ERP systems is vital. Here’s how integration enhances the ability to meet standards:
Real-time Data Sharing
Integrated systems ensure that production schedules are informed by real-time data from across the supply chain. For example, Kinaxis integration with PlanetTogether allows for dynamic scheduling adjustments based on changes in raw material availability or regulatory updates.
End-to-End Visibility
When scheduling systems like PlanetTogether are linked to Aveva, production planners gain comprehensive visibility into manufacturing workflows, ensuring compliance at every stage.
Improved Collaboration
Integration promotes collaboration between departments, ensuring that quality assurance, procurement, and production teams are aligned in meeting industry standards.
Automated Compliance
Automated workflows can embed compliance checks directly into production schedules, reducing the risk of oversight and non-compliance penalties.
Best Practices for Production Planners
To maximize the benefits of integrated systems and ensure compliance with industry standards, production planners can adopt the following practices:
Leverage Advanced Scheduling Algorithms
Use tools like PlanetTogether to prioritize production runs based on compliance needs, customer demand, and resource availability.
Incorporate Predictive Analytics
Integration with ERP systems like SAP enables the use of predictive analytics to forecast potential compliance risks and schedule adjustments proactively.
Monitor Key Performance Indicators (KPIs)
Track metrics such as on-time delivery rates, compliance adherence, and waste reduction to evaluate the effectiveness of production schedules.
Continuous Training
Ensure that planning teams are trained on the latest regulatory requirements and the functionalities of integrated systems.
Industry standards play a pivotal role in shaping production schedules in the food and beverage manufacturing industry. For production planners, integrating tools like PlanetTogether with ERP systems such as SAP, Oracle, Microsoft Dynamics, Kinaxis, or Aveva is no longer a luxury but a necessity. These integrations enable planners to navigate the complexities of compliance while driving operational efficiency.
Embracing advanced technologies and best practices will empower production planners to not only meet industry standards but also exceed customer expectations and drive business growth. Are you ready to take your manufacturing operations to the next level? Contact us today to learn more about how PlanetTogether can help you achieve your goals and drive success in your industry.