
How Can We Help You Become Technologically Agile as a Food and Beverage Manufacturing Company?
Consumer preferences are shifting at lightning speed, regulatory landscapes are becoming increasingly stringent, and supply chain complexities are at an all-time high. To thrive in this dynamic environment, F&B manufacturers must adopt a technology-driven approach to streamline operations, improve efficiency, and foster innovation.
At the heart of this transformation lies the integration of advanced planning tools like PlanetTogether with enterprise systems such as SAP, Oracle, Microsoft Dynamics, Kinaxis, and Aveva.
This integration enables Operations Directors like you to achieve end-to-end visibility, improve responsiveness, and enhance operational efficiency. But how does this help you become more technologically agile? Let’s explore.
The Importance of Technological Agility in F&B Manufacturing
Technological agility refers to the ability of a manufacturing company to quickly adapt to changes in market demands, operational requirements, and technological advancements. For Operations Directors, achieving technological agility means having the tools and systems in place to:
Respond to Market Trends: The rise of plant-based diets, organic products, and allergen-free options has made product diversification critical.
Ensure Regulatory Compliance: Food safety regulations demand meticulous record-keeping and traceability.
Optimize Supply Chains: Unpredictable disruptions, from pandemics to geopolitical tensions, require resilient supply chains.
Sustainability Goals: Reducing waste, lowering carbon footprints, and embracing circular supply chains are now key performance indicators.
Without the right technology, achieving these goals is daunting. Here’s how integrating PlanetTogether with ERP and advanced planning systems can help.

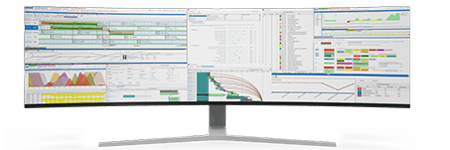
The Role of PlanetTogether in Achieving Agility
PlanetTogether is an advanced production scheduling and planning solution designed to address the unique challenges of manufacturing industries, particularly in complex environments like F&B. When integrated with leading enterprise systems, it creates a robust digital ecosystem that delivers:
1. Enhanced Production Scheduling
By integrating PlanetTogether with SAP or Microsoft Dynamics, you gain a unified view of your production schedules. This real-time synchronization ensures that:
Bottlenecks are minimized: Visualize and address capacity constraints proactively.
Schedules are optimized: Balance demand and supply efficiently.
Downtime is reduced: Coordinate maintenance schedules seamlessly.
For example, if your facility produces beverages with varying shelf lives, PlanetTogether’s integration with SAP can help sequence production runs to minimize spoilage and meet delivery deadlines.
2. Improved Supply Chain Visibility
Integration with systems like Oracle or Kinaxis provides real-time insights into your supply chain. This enables you to:
Respond quickly to raw material shortages or delays.
Optimize inventory levels to prevent overstocking or stockouts.
Collaborate effectively with suppliers and distributors.
Imagine a scenario where a key ingredient faces a supply disruption. With integrated systems, you can immediately adjust production schedules in PlanetTogether while updating procurement plans in Oracle.
3. Advanced Analytics for Decision-Making
When paired with Aveva’s industrial software, PlanetTogether unlocks powerful analytics capabilities. This combination allows you to:
Predict demand fluctuations based on historical and real-time data.
Monitor equipment performance and schedule predictive maintenance.
Identify trends that can inform long-term strategy.
For instance, Aveva’s predictive analytics can alert you to equipment wear, enabling you to preemptively schedule repairs using PlanetTogether, thereby avoiding costly production halts.
4. Scalability and Flexibility
PlanetTogether’s modular design, when integrated with ERP systems like Microsoft Dynamics, allows you to scale operations as your business grows. Whether you’re expanding to new markets or introducing new product lines, the system adapts to your changing needs without significant overhauls.

Steps to Achieve Technological Agility
Assess Your Current State:
Conduct a technology audit to identify gaps in your current systems.
Engage cross-functional teams to understand operational pain points.
Implement in Phases:
Start with pilot projects to validate the integration’s effectiveness.
Gradually scale the solution across all production lines and facilities.
Train Your Teams:
Provide comprehensive training on new systems to ensure adoption.
Establish a feedback loop for continuous improvement.
Measure and Optimize:
Use KPIs like production efficiency, delivery performance, and waste reduction to gauge success.
Continuously refine processes based on data insights.
The F&B industry will continue to face challenges such as evolving consumer demands, stricter regulations, and global disruptions. By adopting an integrated, technology-driven approach, you can position your facility as a leader in agility and innovation. PlanetTogether’s seamless integration with SAP, Oracle, Microsoft Dynamics, Kinaxis, and Aveva equips you with the tools to:
Anticipate and respond to market changes.
Drive efficiency across operations.
Meet sustainability targets without compromising profitability.
As an Operations Director, your role is pivotal in steering your organization towards technological agility. Embrace the tools and strategies that empower your teams, streamline your operations, and ensure long-term success.
Ready to Begin Your Journey?
The path to technological agility starts with the right partnerships. Discover how integrating PlanetTogether with leading enterprise systems can transform your F&B manufacturing operations. Reach out to us today to schedule a consultation and explore tailored solutions for your facility.
LEAVE A COMMENT