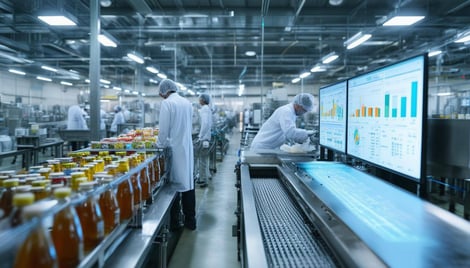
How AI Improves Job Prioritization in Scheduling for Food and Beverage Manufacturing
With fluctuating consumer demand, strict regulatory requirements, and the constant need to manage perishable goods, traditional scheduling methods often fall short. Enter artificial intelligence (AI): a transformative force reshaping how manufacturers prioritize jobs and streamline production schedules.
By integrating advanced AI capabilities with systems like PlanetTogether and enterprise resource planning (ERP) platforms such as SAP, Oracle, Microsoft Dynamics, Kinaxis, or Aveva, companies can unlock unparalleled efficiency and responsiveness.
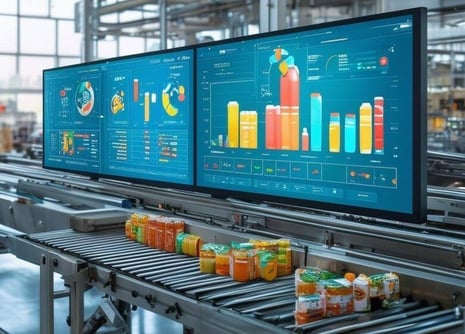
The Complexity of Scheduling in Food and Beverage Manufacturing
Scheduling in this sector is notoriously intricate, involving multiple factors such as:
Perishability of Ingredients: Ensuring raw materials are used before expiration while maintaining quality.
Compliance with Regulatory Standards: Adhering to food safety laws and traceability requirements.
Dynamic Demand: Adapting to seasonal trends and unexpected surges in customer demand.
Equipment Constraints: Managing limited production line capacities and frequent cleaning schedules.
Workforce Availability: Aligning shifts and skill sets with production demands.
Traditional methods—spreadsheets or rule-based scheduling tools—struggle to balance these variables dynamically. This is where AI-powered scheduling solutions excel.
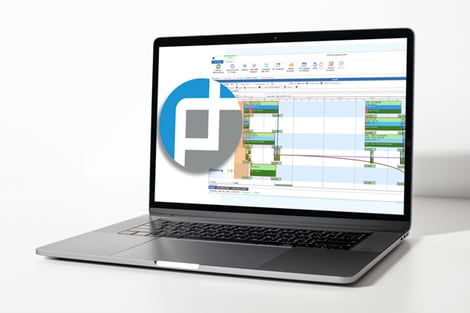
How AI Transforms Job Prioritization in Scheduling
AI-driven systems bring intelligence and adaptability to the scheduling process by leveraging advanced algorithms and data analysis. Here’s how AI improves job prioritization:
Data-Driven Decision-Making
AI collects and analyzes vast amounts of data from multiple sources, such as historical production performance, inventory levels, order demand, and machine availability. This allows it to identify patterns and predict future needs with remarkable accuracy.
For example, by integrating PlanetTogether with SAP or Oracle, manufacturers can create a seamless flow of real-time data between scheduling software and the ERP system. This integration ensures that scheduling decisions are always informed by the latest information on inventory, sales orders, and production capacities.
Dynamic Prioritization
AI-powered systems can dynamically reprioritize jobs based on changing conditions. If a machine breakdown occurs or an urgent order arrives, the system recalibrates the schedule in real time to minimize disruptions.
Using tools like PlanetTogether in conjunction with Microsoft Dynamics, for instance, enables the AI engine to detect production bottlenecks or delays and automatically adjust the sequence of tasks, ensuring high-priority jobs are completed on time.
Optimized Resource Allocation
AI algorithms excel at allocating resources—be it raw materials, equipment, or labor—where they are needed most. They consider constraints like machine maintenance schedules, ingredient shelf lives, and workforce availability to optimize resource utilization.
An integration with Kinaxis can provide advanced supply chain insights, enabling the AI scheduler to align production priorities with raw material delivery schedules, thereby reducing waste and avoiding costly downtimes.
Improved Lead Time Accuracy
Meeting customer delivery expectations is critical in food and beverage manufacturing. AI enhances lead time predictions by analyzing production capacities, potential delays, and supply chain variables.
When paired with Aveva’s industrial software, AI scheduling tools can access detailed machine data to provide more accurate lead time estimates. This not only boosts customer satisfaction but also enhances trust in the manufacturer’s ability to deliver consistently.
Enhanced Compliance and Traceability
In a sector heavily regulated for safety and quality, AI supports compliance by ensuring production schedules align with regulatory requirements. For instance, it can prioritize cleaning and sanitation cycles between product runs to prevent contamination risks.
Integration with Oracle ERP allows PlanetTogether to incorporate compliance data into the scheduling process. This ensures that every batch meets traceability requirements and maintains a clear audit trail.
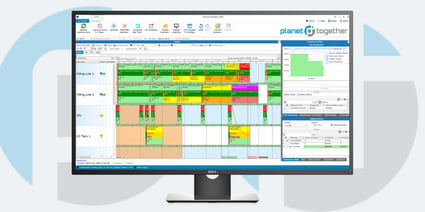
Integration as the Key to Success
While AI provides the intelligence behind improved job prioritization, integration with existing systems is what makes it actionable. PlanetTogether’s scheduling software, for example, acts as the central hub, processing data from ERP systems like SAP, Oracle, or Microsoft Dynamics. This integration ensures that AI-driven scheduling is fully aligned with broader business processes.
Steps to Successful Integration:
Assess Current Systems: Evaluate your existing ERP, MES, and scheduling tools for compatibility with AI solutions.
Choose the Right Integration Partner: Ensure the scheduling software you choose—such as PlanetTogether—supports seamless integration with your ERP platform.
Define Clear Objectives: Identify specific scheduling challenges you want AI to address, such as reducing lead times or minimizing material waste.
Train Your Team: Equip your workforce with the skills to leverage AI-powered tools effectively.
AI is revolutionizing job prioritization in scheduling, enabling food and beverage manufacturers to navigate complexity with precision and agility. By integrating AI-driven scheduling tools like PlanetTogether with robust ERP systems, companies can transform their operations, ensuring that every production decision aligns with business goals and customer expectations.
The path to smarter scheduling starts with embracing AI and integration. Are you ready to take your manufacturing operations to the next level? Contact us today to learn more about how PlanetTogether can help you achieve your goals and drive success in your industry.