By far one of the most important aspects pertaining to manufacturing facilities and warehouses across the globe include managing inventory. Depending on what your organization holds or produces, you need to ask yourself some questions. What is my demand? How frequently does it fluctuate? How cost-effective would holding excess inventory be? Would warehousing product increase my revenue in the long-term? These questions are all prevalent and important when deciding on whether or not to hold excess inventory – and ultimately how much you should store and choose to reorder at a given time.
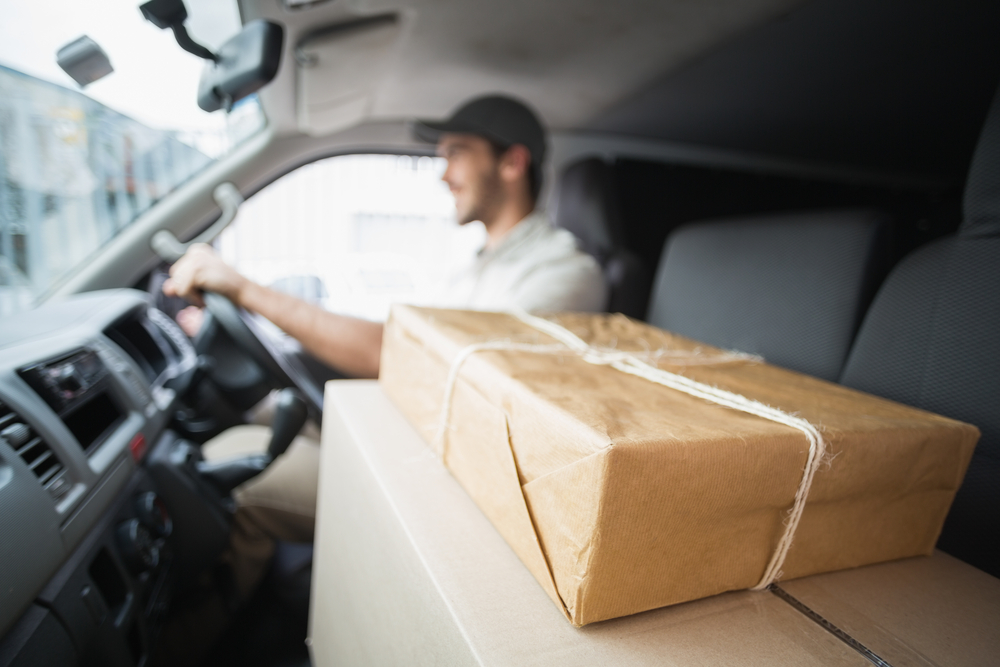
Holding excess inventory is both advantageous and detrimental to an operation, but the options can be weighed when considering what type of products you are warehousing. Within this blog, we are going to discuss the pros and cons associated with holding excess inventory and how it pertains to your operation.
Pros of Holding Excess Inventory
The pros and advantageous of holding excess inventory include the following:
- Enhanced Response Time – Fulfilling orders is extremely important when attempting to grow your consumer base and increase customer loyalty. Holding excess inventory will allow you to easily and quickly fulfill customer orders as soon as they come in, all without having to worry about waiting on your stock to come in to ship an order out. Holding onto your customers is essential – and this is the step in the right direction.
- Decreased Risk Shortage – Through keeping stock on hand, you are able to guarantee, up to a certain point, that you will not run out of a particular item and will have less to worry about if a product is discontinued. If there is a shift upward in demand, then you are able to meet these customer delivery fulfillment times and beat out the competition in this aspect, and will more than likely be able to sell excess inventory at an ideal price.
Cons of Holding Excess Inventory
The cons of holding excess inventory include the following:
- Obsolete Inventory - Obsolete inventory is a common concern among manufacturing facilities and warehouses, especially if your inventory is in the technology sector. The value and quality of your product will decrease the longer that you keep it in stock, in which you have to make it a priority to sell this stock while it is new to the market. Don’t get stuck in building up large amounts of stock for a product that is the new craze or a fad – it could go away in the blink of an eye and you’re stuck with a mountain of inventory.
- Storage Costs Increase – Excess inventory will mean that extra space is needed for storage. Extra space will also mean extra costs, which you will have to include in pricing. This can potentially cause you to lose to the competition with other sellers because your holding costs are making your overall price too high. Even if you have your own warehouse, you will still have extra costs associated with maintenance and also risk not having enough space for newer items.
Understanding the advantages and disadvantages pertaining to holding excess inventory can greatly enhance the decision making process through allowing you to decide whether it is an option for you or not. A software that can aid with adequate inventory management is PlanetTogether’s Advanced Planning and Scheduling (APS) Software. Advanced Planning and Scheduling (APS) Software is a must for manufacturing operations that are seeking to enhance operational efficiency and cut costs within their operation as well.
Advanced Planning and Scheduling Software
Advanced Planning and Scheduling (APS) software has become a must for modern-day manufacturing operations due to customer demand for increased product mix and fast delivery combined with downward cost pressures. APS can be quickly integrated with a ERP/MRP software to fill gaps where these system lack planning and scheduling flexibility and accuracy. Advanced Planning and Scheduling (APS) helps planners save time while providing greater agility in updating ever-changing priorities, production schedules, and inventory plans.
- Create optimized schedules balancing production efficiency and delivery performance
- Maximize output on bottleneck resources to increase revenue
- Synchronize supply with demand to reduce inventories
- Provide company-wide visibility to capacity
- Enable scenario data-driven decision making
Implementation of Advanced Planning and Scheduling (APS) software will take your manufacturing operations to the next level of production efficiency, taking advantage of the operational data you already have in your ERP.
Related Capacity Planning Video
APS Resources