Industrial Robots for Hazardous Environments
The role of production schedulers is essential in ensuring efficiency, safety, and timely delivery of products in chemical manufacturing. However, the challenges posed by hazardous environments often present obstacles that traditional methods struggle to overcome. Enter industrial robots – a game-changing innovation that promises to revolutionize how chemical manufacturing facilities operate in hazardous conditions.
In this blog, we'll look into the integration of industrial robots into chemical manufacturing processes, exploring their benefits, applications, and the seamless integration with advanced scheduling software like PlanetTogether, coupled with ERP, SCM, and MES systems such as SAP, Oracle, Microsoft, Kinaxis, and Aveva.
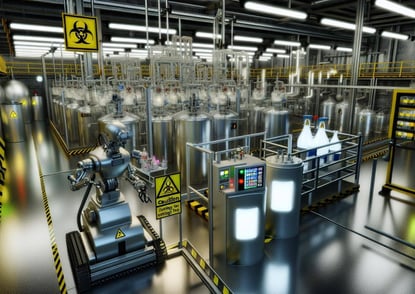
Industrial Robots in Hazardous Environments
Chemical manufacturing facilities are fraught with hazards ranging from toxic chemicals and extreme temperatures to confined spaces and high-pressure environments. Traditional manual labor in such conditions poses significant risks to human safety and often leads to inefficiencies in production processes. Industrial robots offer a compelling solution by assuming tasks that are dangerous or challenging for humans, thereby mitigating risks and improving overall operational efficiency.
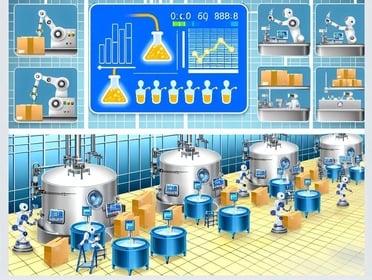
Benefits of Industrial Robots in Chemical Manufacturing
Enhanced Safety: By delegating hazardous tasks to industrial robots, manufacturers can significantly reduce the risk of accidents and injuries to human workers. Robots are immune to fatigue, distraction, and the adverse effects of hazardous substances, making them ideal for operating in high-risk environments.
Improved Efficiency: Industrial robots excel in repetitive, precise, and high-speed tasks, leading to increased productivity and consistency in manufacturing processes. By automating routine operations, production schedulers can optimize resource utilization and minimize downtime, ultimately driving cost savings and enhancing competitiveness.
Flexibility and Adaptability: Modern industrial robots are equipped with advanced sensors, vision systems, and machine learning algorithms that enable them to adapt to dynamic environments and perform a wide range of tasks with minimal reprogramming. This flexibility is invaluable in chemical manufacturing, where processes often require frequent adjustments and customization.
Quality Assurance: Consistency is crucial in chemical manufacturing to ensure product quality and regulatory compliance. Industrial robots offer unparalleled precision and accuracy, reducing variability and minimizing defects in the final product. By maintaining stringent quality standards, manufacturers can safeguard their reputation and customer satisfaction.
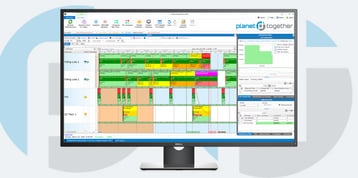
Integration of Industrial Robots with Advanced Scheduling Software
To unleash the full potential of industrial robots in chemical manufacturing, seamless integration with advanced scheduling software is essential. Platforms like PlanetTogether provide production schedulers with real-time visibility, predictive analytics, and optimization tools to streamline operations and maximize efficiency. By integrating with leading ERP, SCM, and MES systems such as SAP, Oracle, Microsoft, Kinaxis, and Aveva, production schedulers can orchestrate a synchronized workflow that leverages the capabilities of industrial robots to the fullest extent.
Key Considerations for Integration:
Data Exchange: Integration between scheduling software and ERP, SCM, and MES systems facilitates seamless data exchange, allowing production schedulers to access critical information such as inventory levels, production orders, and equipment status in real time. This enables proactive decision-making and ensures alignment between production schedules and business objectives.
Process Optimization: By leveraging data analytics and machine learning algorithms, integrated systems can identify optimization opportunities across the manufacturing value chain. Production schedulers can utilize insights generated by scheduling software to fine-tune production schedules, allocate resources efficiently, and optimize the utilization of industrial robots.
Interoperability: Compatibility between scheduling software and ERP, SCM, and MES systems is essential for smooth integration and interoperability. Standardized communication protocols and APIs facilitate seamless data transmission and ensure compatibility with diverse hardware and software environments.
Scalability and Future-Proofing: As chemical manufacturing processes evolve and technologies advance, integrated systems must be scalable and adaptable to accommodate changing requirements. Production schedulers should prioritize solutions that offer scalability and robust support for emerging technologies, ensuring long-term viability and future-proofing their operations.
Industrial robots represent a paradigm shift in chemical manufacturing, offering a potent combination of safety, efficiency, and flexibility in hazardous environments. By seamlessly integrating robots with advanced scheduling software like PlanetTogether and ERP, SCM, and MES systems, production schedulers can unlock new levels of productivity and competitiveness while ensuring the well-being of their workforce.
As the industry continues to embrace automation and digitization, the transformative potential of industrial robots in chemical manufacturing is boundless, heralding a new era of innovation and growth.
With the integration of industrial robots and advanced scheduling software, chemical manufacturing facilities can navigate the complexities of hazardous environments with confidence, paving the way for a safer, more efficient, and sustainable future.
Are you ready to take your manufacturing operations to the next level? Contact us today to learn more about how PlanetTogether can help you achieve your goals and drive success in your industry.
LEAVE A COMMENT