Genetic Algorithms for JIT Scheduling Optimization
The role of a Production Planner cannot be overstated in chemical manufacturing. These professionals are tasked with orchestrating the delicate balance between supply and demand while optimizing resources and timelines. Just-in-Time (JIT) scheduling has emerged as a cornerstone strategy in this domain, aiming to minimize inventory costs and streamline production processes.
However, achieving JIT scheduling perfection is no easy feat. It requires sophisticated planning tools capable of navigating the complexities of production environments. In recent years, the integration of genetic algorithms into planning software, such as PlanetTogether, has revolutionized the way production planners approach scheduling optimization.
In this blog, we'll look into the world of genetic algorithms and explore how they can be harnessed to drive JIT scheduling optimization in chemical manufacturing facilities, especially when integrated with leading ERP, SCM, and MES systems like SAP, Oracle, Microsoft, Kinaxis, and Aveva.

Just-in-Time (JIT) Scheduling
At its core, JIT scheduling aims to synchronize production with demand, ensuring that materials and resources are utilized efficiently and excess inventory is minimized. By producing goods only as needed, JIT reduces waste, carrying costs, and lead times, thereby enhancing overall productivity and responsiveness to customer demands. However, implementing JIT scheduling requires meticulous planning and real-time adaptability, factors that are often challenging to achieve manually.
The Role of Production Planners
Production planners play a pivotal role in JIT scheduling, serving as the architects behind the seamless flow of materials and resources throughout the production process. Their responsibilities include forecasting demand, coordinating production schedules, optimizing resource allocation, and mitigating potential bottlenecks. Traditionally, these tasks relied heavily on heuristic approaches and intuition, leaving room for inefficiencies and suboptimal outcomes.
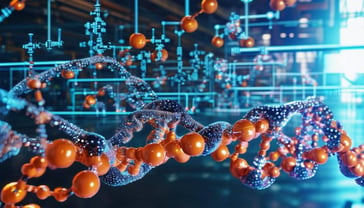
Enter Genetic Algorithms
Genetic algorithms (GAs) offer a dynamic and data-driven approach to scheduling optimization, inspired by the principles of natural selection and evolution. By mimicking the process of natural selection within a simulated environment, GAs iteratively generate and refine schedules to identify the most optimal solutions based on predefined objectives and constraints. Unlike traditional optimization methods, GAs excel in navigating complex, nonlinear problem spaces with multiple variables and interdependencies.

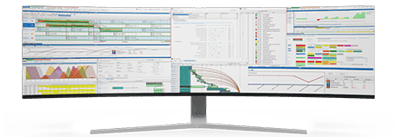
Integration with Planning Software
The integration of genetic algorithms into planning software, such as PlanetTogether, enhances the capabilities of production planners by providing powerful tools for JIT scheduling optimization. By leveraging real-time data from ERP, SCM, and MES systems like SAP, Oracle, Microsoft, Kinaxis, and Aveva, these platforms can generate schedules that are not only efficient but also responsive to dynamic market conditions and production constraints.
Benefits of Genetic Algorithms for JIT Scheduling Optimization:
- Adaptability: Genetic algorithms excel in adapting to changing circumstances and unforeseen disruptions, allowing production planners to quickly adjust schedules in response to fluctuations in demand, supply chain disruptions, or resource constraints.
- Efficiency: By systematically exploring a vast array of scheduling possibilities, genetic algorithms identify near-optimal solutions that minimize production costs, lead times, and inventory levels while maximizing resource utilization and throughput.
- Optimization: Genetic algorithms optimize schedules based on multiple objectives, such as minimizing setup times, maximizing machine utilization, and balancing workloads across production lines, thereby achieving a more balanced and efficient production flow.
- Scalability: Genetic algorithms are highly scalable and can accommodate the complexities of large-scale manufacturing operations, including multiple production lines, diverse product mixes, and intricate process dependencies.
- Transparency: Unlike black-box optimization methods, genetic algorithms offer transparency into the scheduling process, allowing production planners to understand the rationale behind schedule recommendations and fine-tune parameters to align with organizational priorities.
JIT scheduling optimization is essential for staying competitive and responsive to customer demands in chemical manufacturing. Genetic algorithms offer a powerful solution for production planners seeking to maximize efficiency and minimize waste in their scheduling processes.
When integrated with advanced planning software like PlanetTogether and leading ERP, SCM, and MES systems, genetic algorithms empower production planners to achieve unprecedented levels of optimization and agility.
As chemical manufacturing facilities continue to evolve and adapt to changing market dynamics, the adoption of genetic algorithms for JIT scheduling optimization will undoubtedly play a crucial role in driving operational excellence and unlocking new levels of efficiency and profitability.
Are you ready to take your manufacturing operations to the next level? Contact us today to learn more about how PlanetTogether can help you achieve your goals and drive success in your industry.