
Harnessing Data and Smart Manufacturing in Food and Beverage Production
The Digital Transformation in Food and Beverage Manufacturing
Manufacturing IT Managers in food and beverage (F&B) manufacturing are under increasing pressure to optimize production efficiency, ensure compliance, and maintain quality while reducing costs. The key to achieving these goals lies in data-driven decision-making and smart manufacturing technologies.
Smart manufacturing leverages real-time data analytics, AI-driven automation, and integrated planning tools to enhance production efficiency and responsiveness. At the heart of this transformation is the seamless integration of PlanetTogether APS (Advanced Planning and Scheduling) with leading enterprise resource planning (ERP) systems like SAP, Oracle, Microsoft, Kinaxis, or Aveva.
In this blog, we’ll explore how data-driven smart manufacturing can revolutionize F&B production and how IT leaders can successfully integrate APS with ERP systems to optimize operations.
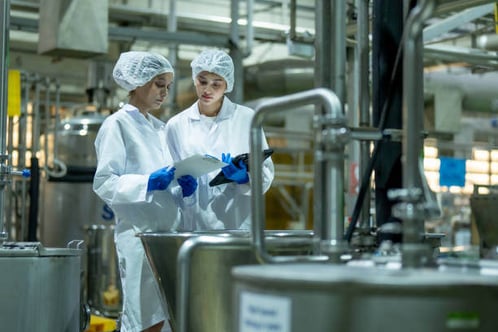
The Role of Data in Smart Manufacturing
Data is the fuel that powers smart manufacturing. Every step of food and beverage production—from sourcing raw ingredients to packaging and distribution—generates vast amounts of data. But collecting data isn’t enough. The real value lies in how manufacturers use this data to drive insights and automation.
Key Data Sources in F&B Manufacturing
Production Equipment and IoT Sensors
Capture temperature, humidity, pressure, and other critical parameters in real time.
Enable predictive maintenance by detecting early signs of machine failure.
Enterprise Resource Planning (ERP) Systems
Manage inventory, procurement, and financials.
Provide historical production data for demand forecasting.
Advanced Planning and Scheduling (APS) Systems
Optimize production schedules based on real-time constraints and priorities.
Integrate with ERP for enhanced supply chain visibility.
Quality Control and Compliance Systems
Monitor product consistency and adherence to safety regulations.
Prevent recalls and compliance violations.
Supply Chain and Logistics Data
Track supplier performance, ingredient availability, and transportation logistics.
Optimize production schedules based on material arrival and customer demand.
By integrating these data sources, F&B manufacturers can transition from reactive decision-making to proactive and predictive strategies, enhancing efficiency and reducing waste.
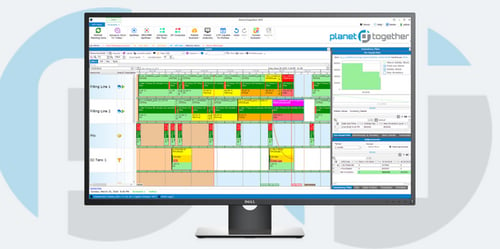
Smart Manufacturing and the Integration of PlanetTogether APS with ERP Systems
One of the biggest challenges in food and beverage manufacturing is balancing production efficiency with real-time demand fluctuations. Traditional manufacturing planning systems often struggle to adapt quickly to changing conditions, leading to inefficiencies such as:
Overproduction or stockouts
Unplanned downtime
Inefficient use of raw materials
Quality control issues due to poor traceability
This is where integrating PlanetTogether APS with ERP systems like SAP, Oracle, Microsoft, Kinaxis, or Aveva becomes a game-changer.
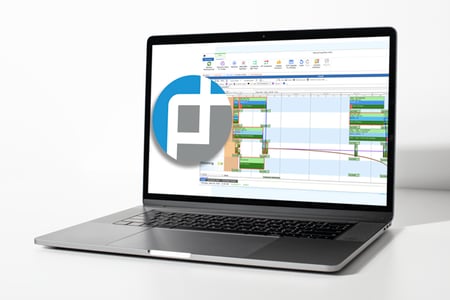
How PlanetTogether APS Enhances Smart Manufacturing
Real-Time Production Scheduling
PlanetTogether APS dynamically adjusts production schedules based on real-time data from ERP, IoT sensors, and supply chain systems. For example:
If an unexpected equipment failure occurs, the system automatically reschedules production to minimize downtime.
If a key ingredient shipment is delayed, PlanetTogether adjusts the schedule to prioritize products that can be made with available materials.
Optimized Resource Utilization
By leveraging data from ERP and IoT devices, APS ensures optimal use of labor, raw materials, and machinery, reducing bottlenecks and maximizing throughput.
Predictive Maintenance & Reduced Downtime
With integration between PlanetTogether and ERP systems, machine performance data is analyzed in real time. AI-driven predictive maintenance ensures:
Machines are serviced before they break down, avoiding costly disruptions.
Maintenance schedules align with production demands, ensuring minimal impact.
Demand-Driven Production
APS systems integrate with forecasting and demand planning tools in ERP solutions (SAP IBP, Oracle SCM Cloud, Microsoft Dynamics 365, etc.), enabling just-in-time manufacturing.
Instead of producing based on static forecasts, manufacturers can adjust production dynamically based on actual demand signals.
This helps prevent overproduction, food waste, and excess inventory costs.
End-to-End Traceability and Compliance
With PlanetTogether’s integration into ERP systems, F&B manufacturers gain end-to-end traceability of ingredients and products. This ensures:
Faster response to recalls.
Compliance with food safety regulations like FDA, FSMA, and HACCP.
Improved consumer trust through better quality control.
The integration of PlanetTogether APS with ERP systems marks a major step forward in data-driven smart manufacturing. By leveraging real-time analytics, predictive intelligence, and optimized scheduling, food and beverage manufacturers can:
✅ Reduce costs and waste
✅ Improve efficiency and throughput
✅ Enhance product quality and compliance
✅ Respond faster to market changes
For Manufacturing IT Managers, the challenge is not just collecting data—it’s ensuring that data is connected, accessible, and actionable. Smart manufacturing is no longer a futuristic concept—it’s a necessity for staying competitive in today’s fast-paced F&B industry.
By adopting PlanetTogether APS and integrating it with SAP, Oracle, Microsoft, Kinaxis, or Aveva, manufacturers can unlock the full potential of data-driven decision-making and build more resilient, agile, and efficient operations.
Are you ready to take your manufacturing operations to the next level? Contact us today to learn more about how PlanetTogether can help you achieve your goals and drive success in your industry.
LEAVE A COMMENT