Harnessing Changeovers and Setup Times
As production planners, you are responsible for ensuring that every minute on the production floor is used effectively to meet customer demands, maintain product quality, and maximize profitability. One of the most significant challenges is managing changeovers and setup times. These non-productive periods are necessary for switching production lines but can lead to significant production delays if not handled effectively.
To tackle this, advanced planning and scheduling (APS) tools like PlanetTogether, integrated with enterprise systems such as SAP, Oracle, Microsoft, Kinaxis, and Aveva, are game-changers. By integrating PlanetTogether into your existing systems, you can optimize changeover processes, streamline setup times, and increase overall efficiency.
Let’s explore how this integration can enhance production planning in packaging manufacturing.
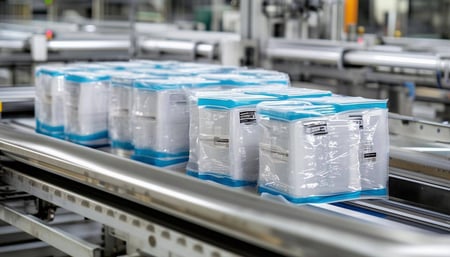
Changeovers in Packaging Manufacturing
Changeovers and setup times are common in packaging manufacturing, especially in facilities that handle diverse packaging formats, sizes, and materials. In essence, a changeover involves stopping a production line, reconfiguring equipment, and ensuring quality standards before restarting production. This downtime impacts productivity, and without careful planning, frequent changeovers can lead to excessive delays, increased costs, and dissatisfied customers.
Several factors influence changeover efficiency, including:
Product complexity: More complex products often require longer changeover times.
Equipment capabilities: Some machines are better suited for quick changeovers.
Workforce readiness: Skilled operators are essential for fast, efficient setup.
Despite these challenges, reducing changeover and setup times is possible with an effective strategy and the right tools. This is where APS tools like PlanetTogether, integrated with systems like SAP, Oracle, Microsoft, Kinaxis, and Aveva, can help transform your production planning approach.

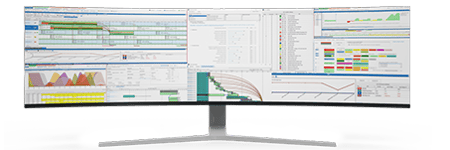
How PlanetTogether Helps Streamline Changeovers and Setup Times
PlanetTogether’s advanced planning and scheduling capabilities offer a comprehensive solution for managing changeovers. Its key features include real-time visibility, predictive scheduling, and automated optimization, which collectively contribute to minimizing downtime.
Key Benefits of PlanetTogether for Managing Changeovers:
Enhanced Visibility: PlanetTogether provides a complete view of all production activities, including planned changeovers. By visualizing where and when changeovers are scheduled, production planners can proactively manage resources and reduce idle time.
Dynamic Scheduling: With PlanetTogether, you can dynamically adjust schedules in response to real-time production floor changes, reducing unplanned delays and improving on-time delivery.
Setup Optimization: The software analyzes historical data and identifies optimal setup sequences to minimize changeover times. By grouping similar products together, you can reduce the frequency and duration of setups.
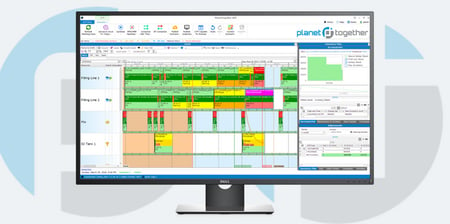
Integrating PlanetTogether with SAP, Oracle, Microsoft, Kinaxis, and Aveva
Integrating PlanetTogether with existing enterprise systems like SAP, Oracle, Microsoft, Kinaxis, or Aveva provides additional layers of functionality. This integration enables seamless data sharing between systems, providing a unified view of production and supply chain activities. Here’s how each integration can add value:
Integration with SAP
SAP is commonly used for enterprise resource planning (ERP) in packaging manufacturing. By integrating SAP with PlanetTogether, you can sync data related to material availability, order schedules, and resource capacities. This allows production planners to make informed decisions about changeovers based on real-time information, reducing delays caused by material shortages or equipment unavailability.
Integration with Oracle
Oracle’s ERP solutions are known for their powerful data analytics capabilities. When combined with PlanetTogether, production planners can leverage Oracle’s data insights to forecast demand trends and adjust production schedules accordingly. This enables planners to reduce the frequency of changeovers by aligning production with forecasted demand, allowing for more extended production runs and fewer setup times.
Integration with Microsoft
Microsoft offers tools like Dynamics 365, which are widely used for managing business operations. Integration with PlanetTogether allows planners to utilize data from across the organization, from inventory levels to labor schedules, ensuring that production runs are coordinated with minimal interruptions. Microsoft Power BI can further enhance this integration by providing advanced visualizations of changeover performance metrics, enabling planners to identify areas for improvement.
Integration with Kinaxis
Kinaxis specializes in supply chain management, offering tools for demand planning, inventory optimization, and supply chain visibility. By integrating PlanetTogether with Kinaxis, production planners can align production schedules with supply chain constraints, ensuring the availability of necessary inputs before initiating changeovers. This coordination reduces downtime, as planners can anticipate delays in the supply chain and adjust schedules accordingly.
Integration with Aveva
Aveva’s solutions are commonly used for operational management in manufacturing. When integrated with PlanetTogether, Aveva provides real-time machine data, such as maintenance schedules and performance metrics. This information is crucial for reducing changeovers and setup times, as planners can proactively schedule setups during planned downtime or maintenance windows, further minimizing production interruptions.
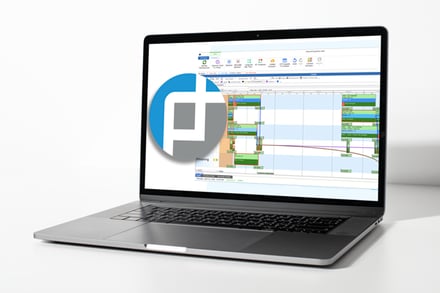
Best Practices for Reducing Changeovers and Setup Times Using PlanetTogether
Integrating PlanetTogether with your ERP or supply chain systems is a powerful step, but optimizing changeovers also requires strategic planning. Here are some best practices to consider:
Group Similar Jobs Together
PlanetTogether allows you to group similar production jobs to minimize setup time. For example, grouping similar materials or packaging formats can reduce the need for equipment reconfiguration. This approach reduces both the frequency and duration of changeovers, boosting overall production efficiency.
Analyze and Standardize Setup Procedures
By analyzing historical data, PlanetTogether can help you identify the most efficient setup procedures. Standardizing these procedures ensures that changeovers are consistent and repeatable. Additionally, standardization reduces the dependency on specific operators, making it easier to achieve optimal setups regardless of who is on the production floor.
Schedule Changeovers During Planned Downtime
With real-time visibility, you can schedule changeovers during planned downtime, such as during lunch breaks or maintenance windows. This minimizes the impact on overall production and ensures that changeovers don’t interfere with high-priority tasks.
Implement Training Programs for Operators
Reducing setup times is not only a matter of software and scheduling; skilled operators are essential for efficient changeovers. By using data insights from PlanetTogether, you can identify areas where additional training is needed, empowering operators to perform faster and more accurate setups.
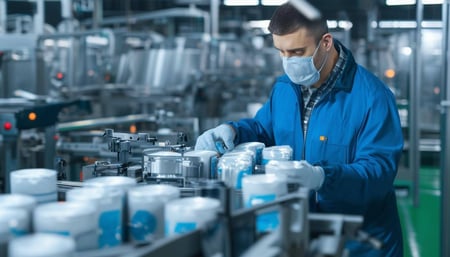
Measuring Success: Key Metrics for Changeover Optimization
To gauge the effectiveness of your changeover optimization efforts, it’s essential to track key performance indicators (KPIs). PlanetTogether, combined with your ERP system, provides detailed reporting capabilities that allow you to measure the following KPIs:
Changeover Time: The average time required to complete a changeover.
Frequency of Changeovers: The number of changeovers within a given period.
Setup Time per Job: The time required to set up each production job.
On-Time Delivery Rate: The percentage of orders delivered on time, which can be impacted by changeover efficiency.
Production Downtime: The total time production is halted due to changeovers and setups.
Regularly reviewing these KPIs enables production planners to identify trends, set realistic targets, and continually improve the efficiency of changeovers. With PlanetTogether’s predictive analytics, you can forecast the impact of changeovers on production schedules and adjust accordingly.
Managing changeovers and setup times is a crucial aspect of production planning in packaging manufacturing. With PlanetTogether, integrated with ERP Systems such as SAP, Oracle, Microsoft, Kinaxis, or Aveva, you gain a powerful toolset for optimizing these processes. This integration provides real-time data, predictive insights, and streamlined scheduling capabilities, enabling you to reduce changeover times, improve on-time delivery rates, and enhance overall efficiency.
By following best practices and leveraging the full capabilities of an integrated APS and ERP system, production planners can transform their approach to managing changeovers, ultimately leading to a more agile and competitive manufacturing environment. Embrace the power of integrated planning, and watch as your facility moves closer to achieving seamless, efficient production cycles.
Are you ready to take your manufacturing operations to the next level? Contact us today to learn more about how PlanetTogether can help you achieve your goals and drive success in your industry.