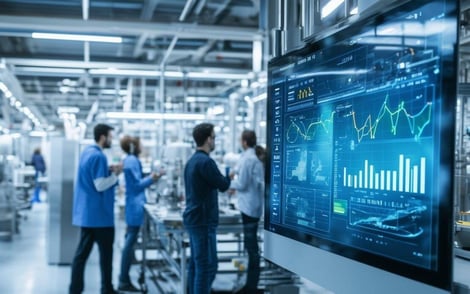
Handling Product Recalls in Production Scheduling for Medical Manufacturing
In medical manufacturing, product recalls are among the most challenging scenarios a plant manager can face. A recall doesn’t just threaten the reputation of your company; it also has profound implications for patient safety, compliance with regulatory bodies, and the financial stability of your operation.
Effective handling of product recalls involves more than just damage control—it requires a strategic approach to production scheduling and seamless integration of advanced tools like PlanetTogether with enterprise systems such as SAP, Oracle, Microsoft, Kinaxis, or Aveva.
This blog explores how plant managers in medical manufacturing facilities can leverage smart production scheduling strategies to manage recalls effectively, ensuring minimal disruption to operations while maintaining compliance and customer trust.
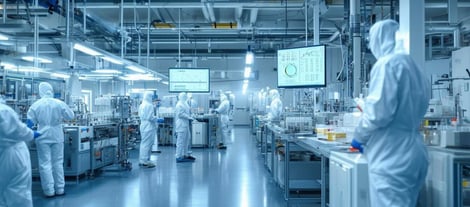
The Complexity of Product Recalls in Medical Manufacturing
Medical manufacturing is characterized by stringent quality standards, extensive documentation, and precise production requirements. A product recall can result from various issues, including manufacturing defects, contamination, labeling errors, or non-compliance with regulatory guidelines. Whatever the cause, recalls demand swift action to identify affected batches, remove defective products, and ramp up production of replacements—all while minimizing impact on ongoing operations.
The inherent complexity of recalls lies in their multi-faceted impact:
Traceability Requirements: Identifying and isolating defective batches from the supply chain.
Regulatory Compliance: Coordinating with governing bodies such as the FDA or EMA.
Operational Continuity: Adjusting production schedules to balance recall management with meeting current demand.
Financial Impact: Mitigating revenue losses and controlling recall costs.
These challenges necessitate advanced production scheduling capabilities supported by integrated software solutions.

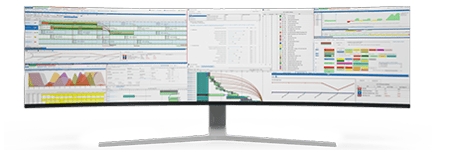
Advanced Production Scheduling in Recalls
Advanced production scheduling tools like PlanetTogether play a pivotal role in navigating the operational challenges of product recalls. By providing real-time visibility into production workflows, inventory levels, and resource allocation, these tools enable plant managers to make informed decisions quickly and efficiently. Here's how advanced scheduling can aid in recall management:
Real-Time Batch Tracking
Recalls require precise identification of affected batches. PlanetTogether's batch tracking feature, integrated with ERP systems like SAP or Oracle, ensures real-time visibility into batch records, enabling swift identification and isolation of defective products.
Dynamic Rescheduling
During a recall, production schedules need to be adjusted dynamically to prioritize the manufacturing of replacement products while maintaining delivery commitments for other orders. PlanetTogether's optimization algorithms can reschedule production lines in real-time, balancing competing priorities.
Capacity Utilization Analysis
Handling a recall often necessitates the reallocation of resources. Integrated systems combining PlanetTogether with tools like Kinaxis can analyze capacity constraints across the supply chain and production facilities, ensuring resources are utilized optimally.
Regulatory Reporting
Compliance with regulatory requirements is non-negotiable in medical manufacturing. By integrating PlanetTogether with Aveva or Microsoft systems, plant managers can streamline documentation and reporting, ensuring accurate records of recall activities and corrective actions.
Scenario Planning
What-if analysis is essential during a recall. PlanetTogether, integrated with enterprise systems, allows plant managers to simulate various scenarios, such as ramping up production or reallocating resources, to assess the best course of action.
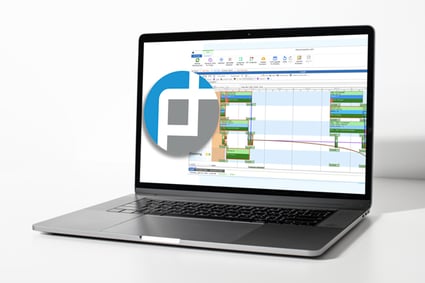
Integration with Enterprise Systems: The Game-Changer
While PlanetTogether offers powerful production scheduling capabilities, its integration with enterprise systems such as SAP, Oracle, Microsoft, Kinaxis, or Aveva amplifies its effectiveness. Here’s how these integrations enhance recall management:
SAP: Comprehensive ERP Support
SAP's robust ERP system provides extensive data on inventory, procurement, and supply chain operations. When integrated with PlanetTogether, it enables real-time data exchange, ensuring that scheduling decisions are based on the most up-to-date information. For recalls, this means faster identification of affected products and streamlined communication across departments.
Oracle: Advanced Analytics
Oracle's data analytics capabilities can complement PlanetTogether's scheduling functions by providing deeper insights into production trends, potential risks, and cost implications. During recalls, Oracle can help quantify the financial impact and identify opportunities to mitigate losses.
Microsoft: Unified Communication
Microsoft's suite of tools, such as Dynamics 365 and Teams, enhances collaboration during recalls. Integration with PlanetTogether ensures that all stakeholders—production planners, quality assurance teams, and supply chain managers—are on the same page, facilitating faster decision-making.
Kinaxis: Supply Chain Synchronization
Kinaxis excels in supply chain planning and risk management. When integrated with PlanetTogether, it enables synchronization between production schedules and supply chain operations. This is particularly valuable during recalls, as it helps align production adjustments with inventory levels and distribution networks.
Aveva: Enhanced Operational Visibility
Aveva's industrial software solutions offer real-time visibility into plant operations. Combined with PlanetTogether, it enables granular tracking of production metrics and immediate identification of bottlenecks, ensuring smooth recall execution.
Best Practices for Handling Product Recalls with Integrated Scheduling Tools
To maximize the effectiveness of PlanetTogether and its integrations, consider the following best practices:
Develop a Recall Response Plan
Have a detailed plan in place that outlines roles, responsibilities, and workflows for handling recalls. Ensure the plan leverages the capabilities of your integrated scheduling and ERP systems.
Invest in Employee Training
Train your team on how to use PlanetTogether and integrated systems during emergencies. Familiarity with these tools ensures faster and more effective recall management.
Conduct Regular System Audits
Ensure that your integrated systems are up-to-date and functioning optimally. Regular audits can identify potential issues before they impact recall management.
Leverage Predictive Analytics
Use predictive analytics to anticipate potential recall scenarios and prepare accordingly. Integrated systems like Oracle or Kinaxis can provide valuable insights into risks and mitigation strategies.
Maintain Transparent Communication
Keep all stakeholders informed throughout the recall process. Use tools like Microsoft Teams for real-time updates and Aveva for operational insights.
Product recalls are a reality in medical manufacturing, but they don’t have to spell disaster. By leveraging advanced production scheduling tools like PlanetTogether and integrating them with enterprise systems such as SAP, Oracle, Microsoft, Kinaxis, or Aveva, plant managers can handle recalls with precision and efficiency. These technologies not only streamline the recall process but also ensure compliance, protect brand reputation, and safeguard patient safety.
For medical manufacturing facilities, the key to effective recall management lies in preparation, real-time responsiveness, and a commitment to leveraging cutting-edge tools. By adopting these strategies, plant managers can turn the challenges of product recalls into opportunities for operational excellence.
Are you ready to take your manufacturing operations to the next level? Contact us today to learn more about how PlanetTogether can help you achieve your goals and drive success in your industry.