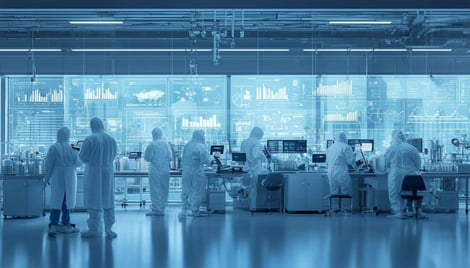
Handling Multi-Level Dependencies in Pharmaceutical Job Scheduling
Every step in the supply chain, from raw material procurement to final delivery, is interwoven with dependencies that demand meticulous planning. Multi-level dependencies in job scheduling can make or break production timelines, compliance efforts, and overall efficiency.
Enter advanced planning and scheduling (APS) tools like PlanetTogether and their ability to integrate with enterprise resource planning (ERP) systems such as SAP, Oracle, Microsoft, Kinaxis, or Aveva. Together, these systems create a unified ecosystem capable of handling the complexities of multi-level dependencies with finesse.
Let’s explore how this integration can empower Supply Chain Managers to thrive in the challenging landscape of pharmaceutical manufacturing.
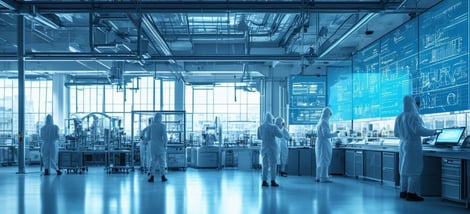
The Challenge of Multi-Level Dependencies in Pharmaceutical Job Scheduling
Multi-level dependencies are a defining feature of pharmaceutical manufacturing. Consider a typical scenario:
Material Availability: Active pharmaceutical ingredients (APIs) must be sourced and available before formulation begins.
Batch Testing: Each batch must undergo rigorous quality control checks, delaying downstream activities if discrepancies arise.
Regulatory Compliance: Documentation and approvals are required at multiple stages, adding to lead times.
Packaging Constraints: Customized packaging for different markets often requires a final synchronization of efforts.
For Supply Chain Managers, these dependencies mean juggling multiple constraints simultaneously. Traditional scheduling tools often fall short when it comes to visualizing and optimizing these interconnected steps.

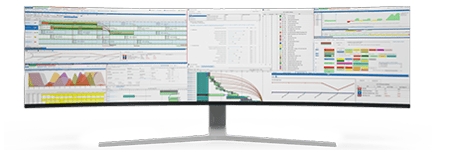
The Role of PlanetTogether and ERP Integration
Advanced Planning and Scheduling systems like PlanetTogether shine in their ability to map and manage these complexities. However, the real power emerges when APS tools integrate seamlessly with ERP systems. Here’s how this integration addresses the key challenges of multi-level dependencies:
Real-Time Data Synchronization
When PlanetTogether integrates with ERP platforms like SAP or Microsoft Dynamics, it ensures that production schedules are informed by up-to-date inventory levels, procurement statuses, and demand forecasts. This synchronization allows Supply Chain Managers to dynamically adjust plans in response to real-time disruptions.
Constraint-Based Scheduling
PlanetTogether leverages data from ERP systems to account for machine capacities, labor availability, and regulatory deadlines. For example, integration with Oracle Cloud ERP can provide insights into workforce availability and machine downtime, enabling constraint-aware scheduling.
Enhanced Visibility
The integration creates a single source of truth for all stakeholders. With Kinaxis RapidResponse, for instance, Supply Chain Managers can access a unified dashboard displaying dependencies, timelines, and risk indicators, simplifying decision-making.
Scenario Planning
In pharmaceutical manufacturing, unexpected changes are the norm. Whether it’s a supplier delay or a last-minute change in regulatory requirements, integration between PlanetTogether and Aveva enables scenario modeling. This capability allows managers to evaluate alternate strategies and choose the best course of action.
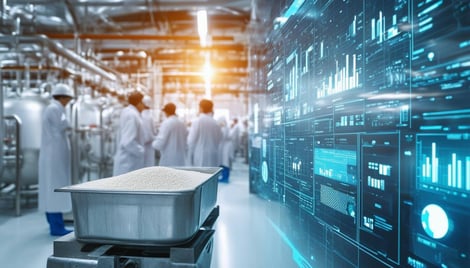
Best Practices for Managing Multi-Level Dependencies
Leverage Data-Driven Insights
Integration enables APS tools like PlanetTogether to harness the wealth of data stored in ERP systems. Use this data to identify bottlenecks, forecast demand, and optimize resource allocation. For example, connecting PlanetTogether with Oracle ERP Cloud can provide predictive analytics on supplier performance, helping to mitigate risks early.
Implement Hierarchical Scheduling
Break down the production schedule into hierarchical levels that mirror your dependencies. Start with high-level milestones (e.g., regulatory approval) and drill down to granular tasks (e.g., individual machine schedules). PlanetTogether’s Gantt chart capabilities are particularly effective for visualizing and managing these hierarchies.
Enable Cross-Functional Collaboration
Integration fosters collaboration between departments. For instance, by linking PlanetTogether with Microsoft Dynamics 365, production, quality control, and procurement teams can access the same data, ensuring alignment across all dependency levels.
Monitor and Adapt in Real Time
The pharmaceutical supply chain is dynamic. Use integration to monitor KPIs such as on-time delivery rates and schedule adherence. Tools like Kinaxis RapidResponse provide live updates, enabling you to adapt quickly to changes.
Invest in Training
Ensure your team understands how to leverage the full capabilities of integrated systems. Provide training sessions on how PlanetTogether interacts with your ERP platform to optimize scheduling.
Handling multi-level dependencies in job scheduling is one of the most challenging aspects of pharmaceutical manufacturing. By integrating PlanetTogether with ERP systems like SAP, Oracle, Microsoft, Kinaxis, or Aveva, Supply Chain Managers gain powerful tools to navigate these complexities.
The result? Greater efficiency, reduced lead times, and enhanced compliance—all critical for staying competitive in today’s fast-paced market. Whether you’re dealing with the intricacies of batch production, regulatory hurdles, or supply chain disruptions, leveraging the synergy between APS and ERP systems is your path to operational excellence.
Are you ready to take your manufacturing operations to the next level? Contact us today to learn more about how PlanetTogether can help you achieve your goals and drive success in your industry.
LEAVE A COMMENT