Lean manufacturing is by far one of the largest manufacturing methods today that is utilized by various production facilities around the globe. Lean manufacturing was developed from manufacturing practices but in recent times it has transformed the world of knowledge, work, and management. Lean manufacturing encourages the concept of continuous improvement and is based off of the fundamental idea of respect for people.
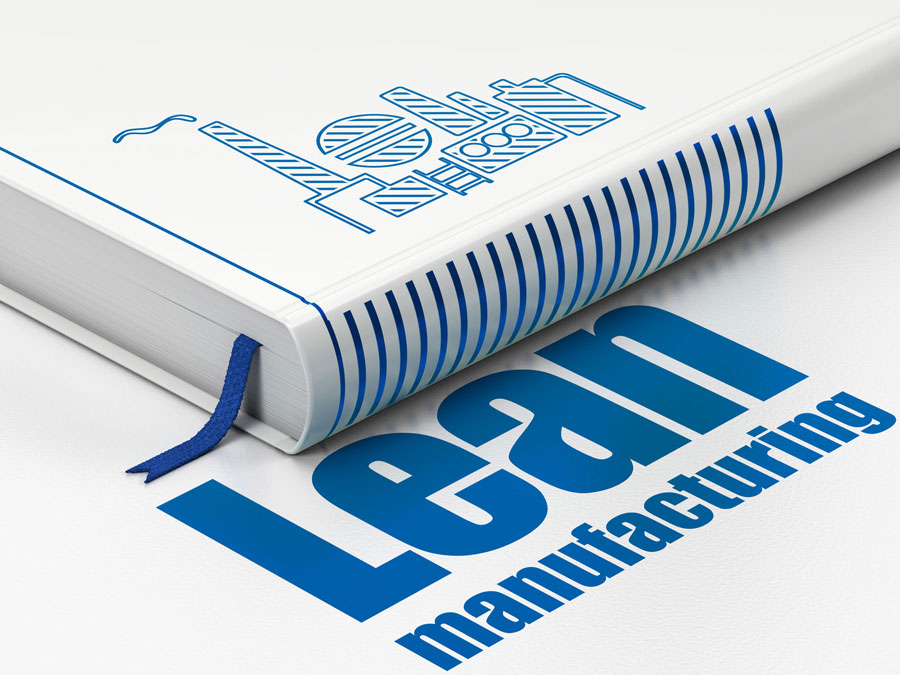
Without lean manufacturing, companies may find themselves with higher cost, higher waste, and most importantly, less profit and revenue being generated back into their company. This is why many companies have found their way into a lean manufacturing operation and have obtained the benefits associated with the concept and methodology. Before implementing the methodology, it is essential to understand the five principles of lean manufacturing.
Five Principles of Lean Manufacturing
The five principles of lean manufacturing include the following:
- Defining Value - In order to better understand this principle of defining customer value, it is important to understand what value is. Value is defined as what customers are willing to pay for a product or service. It is absolutely essential to discover what the actual needs of the customer may be. At times, customers may not know what they want or may have a difficult time articulating it. This is especially common for novel products or technologies. There are many techniques such as interviews, surveys, demographic information, and web analytics that can help you decipher and discover what customers define as “valuable”.
- Mapping the Value Stream - The second principle within lean manufacturing is identifying and mapping the value stream. Within this step, the goal is to use the customer’s value as a reference point and identify all the activities that contribute to these values. If there are activities that are considered to not add value, then this is considered also considered as waste and should be eliminated. The waste can be broken into two categories: non valued added but necessary and non-value and necessary.
- Creating Flow - Once you remove waste from the value stream, the following action is to ensure that the flow of remaining steps run smoothly without interruptions or delays. Some of these strategies for ensuring that value-adding activities flow smoothly include breaking down steps, reconfiguring the production steps, leveling out the workload, creating cross-functional departments, and training employees to be multi-skilled and adaptive.
- Establishing Pull - When it comes to inventory, it is considered one of the biggest waste within any production system. The entire goal of pull-based systems is to limit inventory and work in process (WIP) items while ensuring that the requisite materials and information are available for a smooth flow of work. In other words, a pull-based system enables for JIT delivery and manufacturing where products are created at the time that they are needed and in just the quantities needed.
- Pursuing Perfection - In order to pursue perfection, you have to understand that waste are prevented through the achievement of the first four steps: 1.) identifying value, 2.) mapping the value stream, 3.) creating flow, 4.) adopting a pull system. However, the fifth step of pursuing perfection is the most important among them all. It makes lean thinking and continuous process improvement a part of the organizational culture.
If you are seeking to implement the five principles of lean manufacturing, it is an absolute must that you understand the five principles. A software that can easily be integrated with lean thinking is PlanetTogether’s Advanced Planning and Scheduling (APS) Software. Advanced Planning and Scheduling (APS) Software is an absolute necessity for modern-day lean and agile manufacturers that are seeking to improve operational efficiency within their operation. While you may believe that MRP and ERP alone are softwares that are sufficient enough to enhance production, there are areas where these softwares are falling short. This is why many manufacturing companies are finding themselves implementing Advanced Planning and Scheduling (APS) Software into their operations and witnessing the benefits such as cost reduction, waste reduction, thorough visibility, and more.
Advanced Planning and Scheduling Software
Advanced Planning and Scheduling (APS) software has become a must for modern-day manufacturing operations due to customer demand for increased product mix and fast delivery combined with downward cost pressures. APS can be quickly integrated with a ERP/MRP software to fill gaps where these system lack planning and scheduling flexibility and accuracy. Advanced Planning and Scheduling (APS) helps planners save time while providing greater agility in updating ever-changing priorities, production schedules, and inventory plans.
- Create optimized schedules balancing production efficiency and delivery performance
- Maximize output on bottleneck resources to increase revenue
- Synchronize supply with demand to reduce inventories
- Provide company-wide visibility to capacity
- Enable scenario data-driven decision making
Implementation of Advanced Planning and Scheduling (APS) software will take your manufacturing operations to the next level of production efficiency, taking advantage of the operational data you already have in your ERP.
APS Resources