With the rising costs of production, many manufacturers are looking for ways to increase efficiency in their production systems to remain competitive in the market. One commonly used technique is Lean Manufacturing, which aims to reduce waste from the production process to cut costs and increase efficiency.
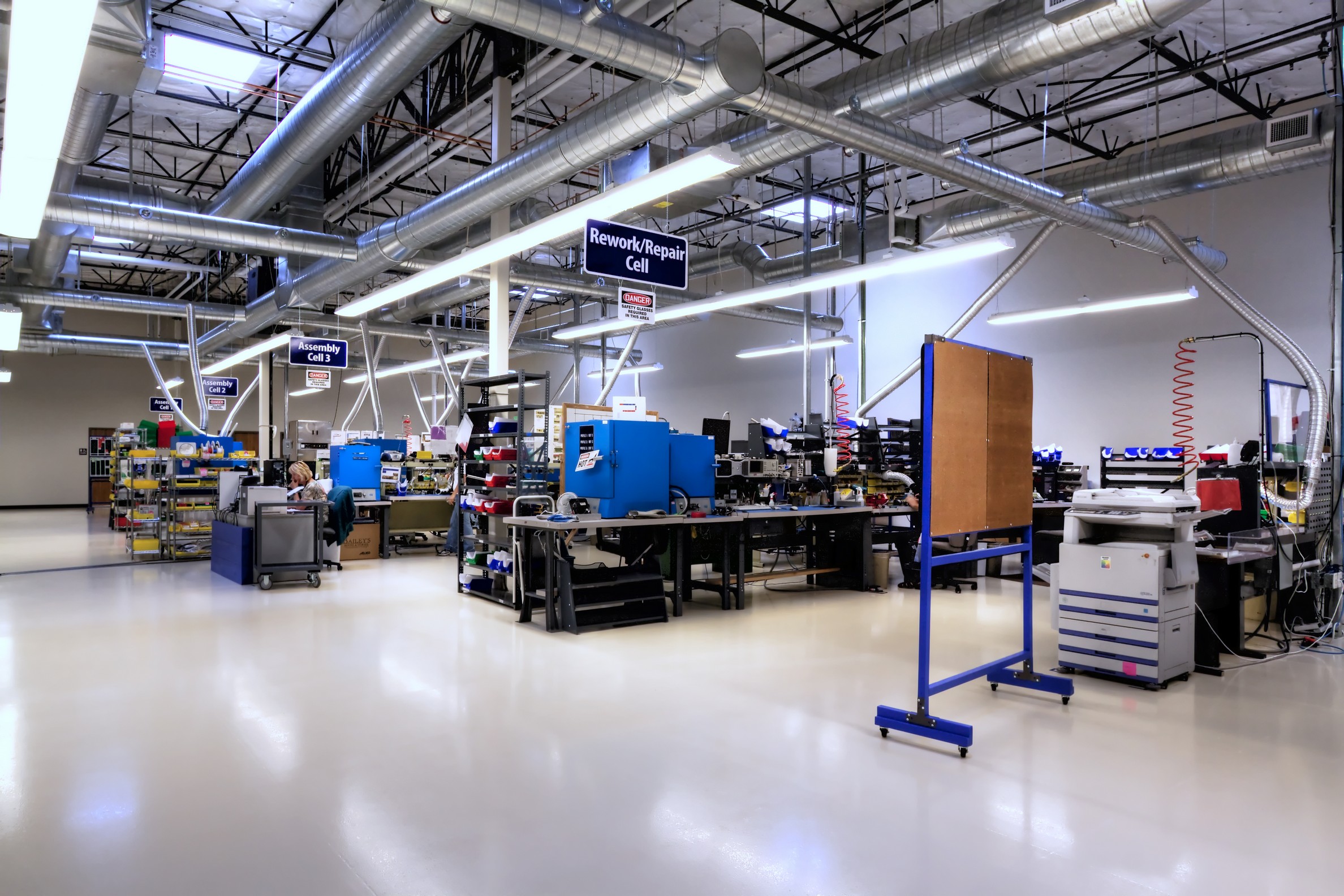
With the rising costs of production, many manufacturers are looking for ways to increase efficiency in their production systems to remain competitive in the market. One commonly used technique is Lean Manufacturing, which aims to reduce waste from the production process to cut costs and increase efficiency.
What is Lean Manufacturing?
Lean Manufacturing originates from the Japanese automotive industry and aims to minimize waste and remove activities that are not valuable to the production process. Removing waste from the system reduces the time required for production while improving the quality of products and reducing the overall costs.
There are many benefits that arise from using Lean Manufacturing techniques. These include:
- Waste Minimization: The main goal of lean manufacturing is to reduce the amount of waste throughout production. The elimination of wasteful processes will increase the efficiency and throughput of your production. In addition, the elimination of defects and over-processing will bring you one step closer to building a more sustainable supply chain.
- Cost Reduction: Lean manufacturing strategies allow you to reduce the amount of WIP items you need to store. Warehouses and inventory managing processes can incur very high costs so reducing the number of items that need to be stored will allow you to reduce or eliminate warehouse space.
- Meet Promised Dates: Streamlining the production process and removing wasteful activities allows you to reduce the manufacturing lead time for the object. This allows you to produce more items in a shorter amount of time so that you can be sure to meet promised delivery dates.
- Improve Quality: Efforts to eliminate defects to reduce waste will often require an improvement of processes and lead to products of better quality. Lean manufacturing techniques also encourage the practice of continuous improvement.
Five Principles of Lean Manufacturing
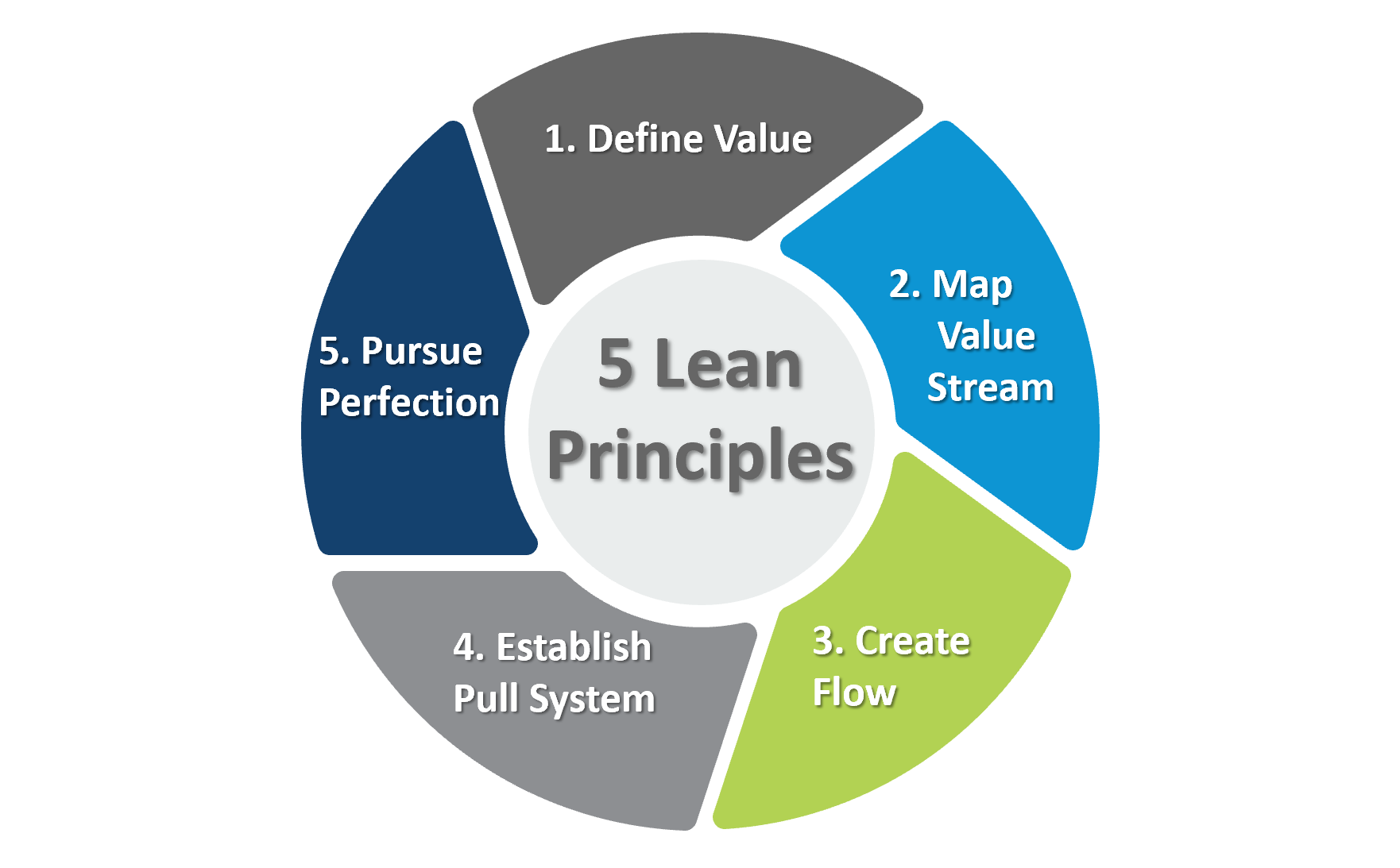
The five principles of lean manufacturing include defining value, mapping the value stream, creating flow, using a pull system, and pursuing perfection. These five principles are outlined in more detail below:
- Define Value - Lean manufacturing principles aim to add value to the end customer. It is important to understand what the customers value in terms of their needs, what they really want, and what they are willing to pay for. It is possible that consumers are unable to properly articulate exactly what they want. This is especially common where new products are being developed or with technology. There are many techniques such as interviews, surveys, and demographic information that can help you discover what exactly customers find valuable.
- Mapping the Value Stream - The second principle within lean is identifying and mapping the value stream. In this step, the overall goal is to utilize the customer’s value as a reference point and locate areas that correlate with their values. Any activities and processes that do not add value to the end customer are considered wasteful. The waste can be broken into two categories: non-value added but necessary and non-value & unnecessary. The latter is pure waste and should be eliminated while the former should be reduced as much as possible.
- Creating Flow - After removing the waste from the value stream, the following action is to ensure that the flow of the remaining steps will run smoothly without interruption or delays. Some strategies for ensuring that value-adding activities flow smoothly include methods such as re-configuring production steps, leveling out the workload, or creating cross-functional departments.
- Establish Pull - Inventory is one of the biggest wastes within a production facility. The overall goal of a pull-based system is to limit inventory and work in process (WIP) items while ensuring that the requisite materials and information are available for a smooth workflow. A pull-based system allows for Just-In-Time delivery and manufacturing where products are created at a time they are needed and in the quantities needed. Through following the value stream and working backward through the production system, you can ensure that the products produced will be able to satisfy the needs of customers.
- Pursue Perfection - Waste is prevented through the achievement of the first four steps which include identifying value, mapping the value stream, creating flow, and adopting a pull system. The fifth step, pursuing perfection makes lean thinking and continuous process improvement a part of the organizational culture. All employees should attempt to strive toward perfection while delivering products based on the customer’s needs.
A software that can aid with a lean manufacturing operation is PlanetTogether’s Advanced Planning and Scheduling (APS) Software. A visual production planning and scheduling system is useful to identify areas of production that are in need of improvement and represent potential waste. This allows you to manipulate your overall production process and areas of production that are in need of enhancement and ultimately reduce waste within your overall operation.
The shift to PlanetTogether is saving us about 15% in inventory overhead and about 20% in overtime labor expenses.
BRUCE HAYS, DIRECTOR OF MANUFACTURING, J&J SYNTHES
Advanced Planning and Scheduling Software
Advanced Planning and Scheduling Softwares have become a must for modern-day manufacturing operations as customer demand for increased product assortment, fast delivery, and downward cost pressures become prevalent. These systems help planners save time while providing greater agility in updating ever-changing priorities, production schedules, and inventory plans. APS Systems can be quickly integrated with an ERP/MRP software to fill the gaps where these systems lack planning and scheduling flexibility, accuracy, and efficiency.
With PlanetTogether APS you can:
- Create optimized schedules that balance production efficiency and delivery performance
- Maximize throughput on bottleneck resources to increase revenue
- Synchronize supply with demand to reduce inventories
- Provide company-wide visibility to resource capacity
- Enable scenario data-driven decision making
The implementation of an Advanced Planning and Scheduling (APS) Software will take your manufacturing operations to the next level of production efficiency by taking advantage of the operational data you already possess in your ERP system. APS is a step in the right direction of efficiency and lean manufacturing production enhancement. Try out a free trial or demo!
Related Multi Plant Video
APS Resources