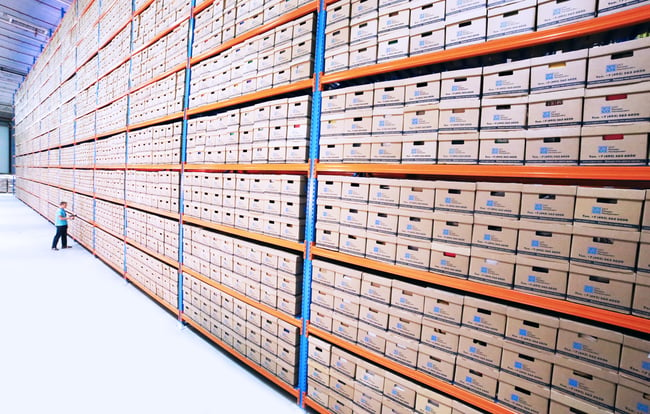
As inventory is a substantial component within many manufacturing operations, the challenge comes in determining the optimal quantity of inventory to hold in stock. On one hand, having a lot of inventory in stock leads to increased customer satisfaction and ensures for on-time delivery. As customer expectations are changing, being able to receive items quickly is an important aspect of their experience with your company. This will lead to increased loyalty as they know your business keeps products in stock at all times.
However, holding excess inventory for popular items may only be beneficial for businesses that move inventory regularly and quickly. Excess inventory has both various advantages and disadvantages that can both benefit and harm your business.
This is why it is important to take a look at the advantages and disadvantages of holding excess inventory and determine whether it is an adequate solution for your business. In the following sections, we will discuss some of the advantages and disadvantages pertaining to excess inventory within an operation.
Advantages of Excess Inventory
The advantages pertaining to excess inventory include the following:
- Fast Order Fulfillment - One of the main advantages of having high stock levels is that you can ensure that customer fulfillment times are always met within the time frame that they are requesting. As customers will receive their product in hand faster, they will have a more positive experience working with your business which is a fundamental aspect of quality customer service and loyalty.
- Reduced Shortage Risk - In addition to fast customer fulfillment, having excess inventory will ensure that stock shortages are reduced or eradicated. If the factory experiences issues where they cannot proceed with production, they may risk having a shortage of items. This is especially true for manufacturing facilities using JIT (Just-In-Time) production strategies. Holding more inventory will allow you to have a buffer to reduce the risk in these situations, allowing you to ship products to customers within a normal time frame even though your production line is down.
- Quantity Discounts - Being able to hold large amounts of inventory usually means that you can benefit from supplier discounts if you purchase in bulk. These discounts will reduce your costs and allow you to make a larger profit on your sales. This may also allow you to sell your products at a lower price which can make your company gain a competitive advantage in the market.
While there are advantages associated with excess inventory, it is important to consider the disadvantages as well.
Disadvantages of Excess Inventory
The disadvantages of excess inventory include the following:
- Storage Costs - One of the biggest issues with inventory-based facilities is the amount of cost associated with storage. The more stuff you have, the more space you need to store it. Warehouse space to hold large amounts of inventory will only lead to increased costs within the organization. Inventory-related costs include storage costs, inventory control, audits, and additional labor to work in the warehouse. Depending on your location, storage costs may be extremely high, especially in densely populated areas where space is limited.
- Obsolete Inventory - Another risk that comes with holding excess inventory is that it can become obsolete before you sell it all. This is especially true if you are following short-term demand and are holding the newest technological advancement for consumers. It is likely that you will hold that for a short period of time before something new comes out. If you stock up on a particular product with no plan to innovate or continuously improve, it will be obsolete once the craze is over and you will be left with a substantial amount of inventory on hand with no one to sell to.
- Reduced Available Cash Flow - While you may get better prices when purchasing goods in bulk, you are also tying up a lot of money into your inventory and will have less cash flow to cover daily expenses. Having cash flow issues is never a good thing, especially when you don’t have enough money to cover expenses and need to borrow money.
The challenge that comes with inventory management is to find the right balance for your business. You want to ensure that you have enough items in stock to meet customer demand without incurring high inventory costs and risking being left with obsolete stock.
The shift to PlanetTogether is saving us about 15% in inventory overhead and about 20% in overtime labor expenses. We’re not building equipment to stock any longer - we’re building to ship.BRUCE HAYS, DIRECTOR OF MANUFACTURING, J&J SYNTHES
A software that can help with inventory management is PlanetTogether’s Advanced Planning and Scheduling (APS) Software. This software is a must for manufacturing operations around the globe that are looking to fulfill delivery time frame requirements, reduce inventory, and ensure that they provide the best customer experience.
Advanced Planning and Scheduling (APS) Software
Advanced Planning and Scheduling Softwares have become a must for modern-day manufacturing operations as customer demand for increased product assortment, fast delivery, and downward cost pressures become prevalent. These systems help planners save time while providing greater agility in updating ever-changing priorities, production schedules, and inventory plans. APS Systems can be quickly integrated with an ERP/MRP software to fill the gaps where these systems lack planning and scheduling flexibility, accuracy, and efficiency.
With PlanetTogether APS you can:
- Create optimized schedules that balance production efficiency and delivery performance
- Maximize throughput on bottleneck resources to increase revenue
- Synchronize supply with demand to reduce inventories
- Provide company-wide visibility to resource capacity
- Enable scenario data-driven decision making
The implementation of an Advanced Planning and Scheduling (APS) Software will take your manufacturing operations to the next level of production efficiency by taking advantage of the operational data you already possess in your ERP system. APS is a step in the right direction of efficiency and lean manufacturing production enhancement. Try out a free trial or demo!
Related Capacity Planning Video
APS Resources
Topics: Inventory Management
LEAVE A COMMENT