Sustainable Packaging Material Lifecycle Analysis Tools
Sustainability has emerged as a critical consideration for companies across industries. In the realm of packaging manufacturing, sustainability is not just a buzzword; it's a fundamental imperative. As the Purchasing Manager of a packaging manufacturing facility, you understand the importance of adopting sustainable practices throughout the supply chain. One key aspect of this endeavor is the implementation of robust lifecycle analysis tools to assess and enhance the sustainability of packaging materials.
In this blog, we will look into the significance of sustainable packaging material lifecycle analysis tools and explore how integrating such tools with enterprise resource planning (ERP), supply chain management (SCM), and manufacturing execution systems (MES) can drive efficiency and sustainability in your operations. Specifically, we'll examine the integration between PlanetTogether, a leading production planning software, and prominent ERP/SCM/MES systems like SAP, Oracle, Microsoft, Kinaxis, and Aveva.
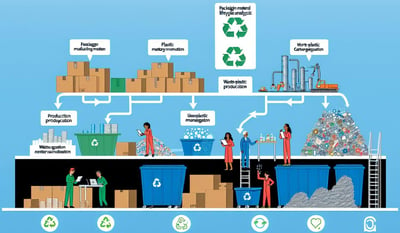
Sustainable Packaging Material Lifecycle Analysis
At its core, this process involves evaluating the environmental impact of packaging materials throughout their entire lifecycle – from raw material extraction to disposal or recycling. By conducting a comprehensive lifecycle analysis, companies can identify opportunities to reduce resource consumption, minimize waste, and optimize material usage.
These analyses typically consider factors such as carbon footprint, energy consumption, water usage, recyclability, and overall environmental impact. Armed with this data, businesses can make informed decisions regarding material selection, design optimization, and process improvements to align with sustainability goals.
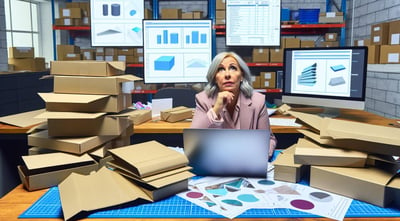
Challenges Faced by Purchasing Managers
As a Purchasing Manager, you encounter several challenges in your quest to procure sustainable packaging materials. These challenges include:
Limited Visibility: Traditional procurement processes often lack real-time visibility into the environmental impact of packaging materials.
Complex Supply Chains: Packaging materials may traverse complex supply chains, making it challenging to trace their origins and assess their sustainability credentials.
Data Fragmentation: Critical sustainability data may reside in siloed systems, hindering holistic analysis and decision-making.
Compliance Concerns: Regulatory requirements and evolving consumer preferences necessitate compliance with stringent sustainability standards.
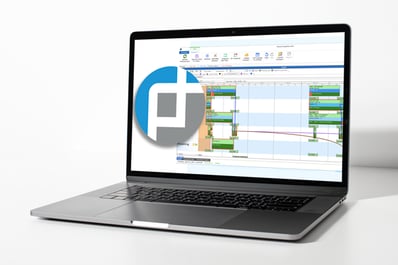
The Role of Integration in Enhancing Sustainability
Integration between production planning software like PlanetTogether and ERP/SCM/MES systems addresses these challenges by fostering seamless data exchange and collaboration across organizational functions. Let's explore how this integration can enhance sustainability efforts:
Real-time Data Syncing: Integration enables real-time syncing of production plans, material orders, and sustainability data between PlanetTogether and ERP/SCM/MES systems. This ensures that purchasing decisions align with sustainability objectives and production schedules.
Comprehensive Lifecycle Analysis: By integrating with ERP systems, PlanetTogether can access comprehensive data on raw material sourcing, production processes, and distribution networks. This facilitates holistic lifecycle analysis, allowing Purchasing Managers to evaluate the environmental impact of packaging materials at every stage.
Optimized Procurement: Integration empowers Purchasing Managers to make informed procurement decisions based on real-time sustainability metrics. For instance, they can prioritize suppliers with eco-friendly practices or select materials with lower carbon footprints without compromising production schedules.
End-to-End Traceability: Integrating with MES systems enables end-to-end traceability of packaging materials, from production floor to delivery. This visibility allows companies to monitor material usage, identify inefficiencies, and implement corrective measures to minimize waste and enhance sustainability.
Predictive Analytics: By leveraging data from ERP and SCM systems, PlanetTogether can deploy predictive analytics to forecast demand, optimize inventory levels, and minimize overproduction – thereby reducing environmental impact and promoting resource efficiency.
Sustainable packaging material lifecycle analysis tools play a pivotal role in driving sustainability and efficiency in packaging manufacturing. Integration between production planning software like PlanetTogether and ERP/SCM/MES systems amplifies the impact of these tools by facilitating real-time data exchange, comprehensive lifecycle analysis, and informed decision-making.
As a Purchasing Manager, embracing this integration can empower you to navigate the complex landscape of sustainable procurement, optimize material usage, and contribute to a greener future. By leveraging the synergy between technology and sustainability, packaging manufacturing facilities can achieve their dual objectives of profitability and environmental stewardship.
Are you ready to take your manufacturing operations to the next level? Contact us today to learn more about how PlanetTogether can help you achieve your goals and drive success in your industry.
LEAVE A COMMENT