Business Process Reengineering
The seamless flow of materials, resources, and tasks is not just a matter of productivity; it directly impacts patient care and safety. As a Production Scheduler in a medical manufacturing facility, you're at the heart of this operation, responsible for orchestrating the intricate dance of production processes. However, the traditional methods of scheduling may not suffice in today's dynamic and highly regulated environment. This is where business process reengineering (BPR) steps in.
In this blog, we'll look into the realm of business process reengineering tailored for scheduling efficiency in medical manufacturing. Moreover, we'll explore the integration between advanced scheduling tools like PlanetTogether and leading ERP, SCM, and MES systems such as SAP, Oracle, Microsoft, Kinaxis, and Aveva, to streamline operations and drive competitive advantage.
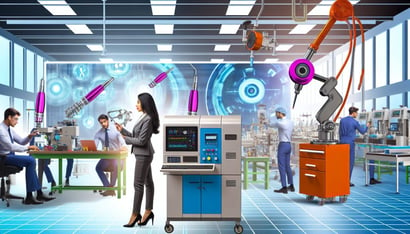
Understanding Business Process Reengineering
Business Process Reengineering (BPR) is not merely about tweaking existing processes; it's a fundamental overhaul aimed at achieving dramatic improvements in performance, efficiency, and effectiveness. For production schedulers in medical manufacturing, BPR offers an opportunity to optimize workflows, eliminate bottlenecks, and adapt to evolving market demands.
The Core Principles of BPR for Scheduling Efficiency:
Holistic Approach: BPR requires looking at the scheduling process from a holistic perspective, considering all interconnected aspects such as demand forecasting, inventory management, resource allocation, and production planning.
Customer Focus: In medical manufacturing, the end-users are patients whose well-being relies on timely access to quality products. BPR should prioritize customer needs and satisfaction, aligning scheduling decisions with patient-centric outcomes.
Simplicity and Flexibility: Complex scheduling algorithms and rigid processes can hinder adaptability. BPR aims to simplify scheduling workflows while ensuring flexibility to accommodate changes in demand, resource availability, and regulatory requirements.
Technology Integration: Embracing advanced scheduling tools and integrating them with existing systems is a cornerstone of BPR. This enables real-time visibility, data-driven decision-making, and automation of repetitive tasks.
Continuous Improvement: BPR is not a one-time initiative but a continuous journey of optimization. Regular evaluation, feedback loops, and agile methodologies are essential for sustaining efficiency gains over time.
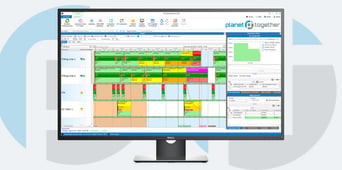
Integration of PlanetTogether with ERP, SCM, and MES Systems
PlanetTogether is a powerful production scheduling software designed to optimize complex manufacturing environments. When integrated with ERP, SCM, and MES systems such as SAP, Oracle, Microsoft, Kinaxis, and Aveva, it becomes a catalyst for synchronization and efficiency across the entire value chain.
Seamless Data Exchange: Integration allows for seamless exchange of data between scheduling software and other systems. This means accurate and up-to-date information flows effortlessly, enabling better decision-making at every level of the organization.
Real-Time Visibility: By integrating with ERP systems, PlanetTogether provides real-time visibility into inventory levels, order statuses, and resource availability. This enables production schedulers to make informed decisions based on the most current information, reducing lead times and minimizing stockouts.
Automated Workflows: Integration with MES systems automates workflows, reducing manual intervention and streamlining production processes. Tasks such as job tracking, quality control, and equipment maintenance can be seamlessly coordinated with scheduling activities, improving overall efficiency.
Improved Forecasting and Planning: ERP systems are rich sources of historical data and market insights. By integrating with these systems, PlanetTogether can leverage advanced forecasting algorithms to generate more accurate production schedules. This helps in optimizing inventory levels, reducing waste, and meeting customer demand with greater precision.
Compliance and Traceability: In the highly regulated medical manufacturing industry, compliance with quality standards and traceability requirements is non-negotiable. Integration with ERP and SCM systems ensures that scheduling decisions align with regulatory guidelines and enable thorough tracking of materials and processes from procurement to delivery.
In the highly regulated world of medical manufacturing, efficient production scheduling is essential for meeting customer demands, ensuring product quality, and driving competitive advantage. Business Process Reengineering (BPR), coupled with advanced scheduling tools like PlanetTogether and integration with leading ERP, SCM, and MES systems, offers a strategic framework for achieving scheduling efficiency.
As a Production Scheduler, embracing BPR principles and leveraging integrated scheduling solutions can unlock new levels of operational excellence, enabling your organization to thrive in an ever-evolving industry landscape. By continuously optimizing workflows, harnessing technology, and prioritizing customer-centricity, you can pave the way for sustainable growth and innovation in medical manufacturing.
Are you ready to take your manufacturing operations to the next level? Contact us today to learn more about how PlanetTogether can help you achieve your goals and drive success in your industry.
LEAVE A COMMENT