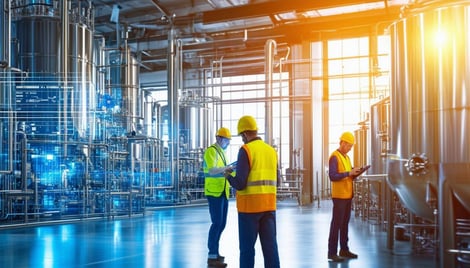
Enhancing Schedule Visibility in Chemical Manufacturing through Integrated Planning Solutions
Production schedulers face the ongoing challenge of balancing operational efficiency, resource utilization, and tight production timelines. Whether you're managing batch production, continuous processes, or complex workflows, maintaining clear visibility across your schedules is critical for ensuring on-time delivery and maximizing plant performance. However, achieving this level of transparency can often feel like chasing a moving target. Disconnected systems, siloed data, and manual scheduling methods can cloud visibility and hinder real-time decision-making.
So, how can production schedulers in chemical manufacturing enhance schedule visibility while minimizing disruptions? The answer lies in leveraging integrated planning solutions like PlanetTogether that seamlessly connect with leading Enterprise Resource Planning (ERP) systems such as SAP, Oracle, Microsoft, Kinaxis, or Aveva.
In this blog, we explore the importance of schedule visibility in chemical manufacturing and how integrated planning platforms can empower production schedulers to optimize operations, improve resource alignment, and unlock greater productivity.
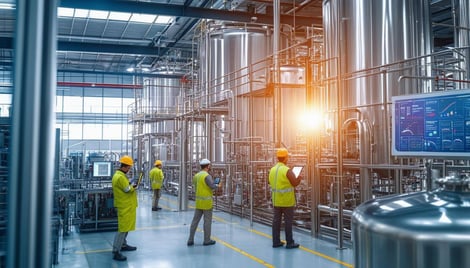
The Growing Importance of Schedule Visibility in Chemical Manufacturing
Chemical manufacturing is inherently complex, involving:
Multiple production processes (e.g., mixing, blending, distillation, drying, and packaging).
Resource-intensive operations (e.g., raw material handling, equipment constraints, and human resource scheduling).
Stringent safety and compliance requirements.
Variable batch sizes and changing customer demands.
As the complexity grows, so too does the need for accurate and real-time visibility into production schedules. Without clear insight, production teams are forced to make reactive decisions, leading to inefficiencies such as:
Underutilized or overburdened equipment.
Production bottlenecks that delay delivery schedules.
Misaligned resource allocation.
Higher operational costs.
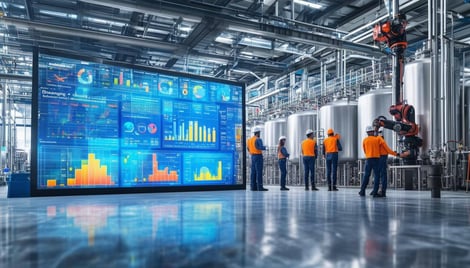
Why Traditional Scheduling Methods Fall Short
Many chemical manufacturers continue to rely on manual spreadsheets, outdated scheduling software, or disparate systems for production planning. While these methods may work for basic scheduling tasks, they often fail to provide the visibility and agility needed for modern manufacturing environments. Key limitations include:
Disconnected Systems: Data silos prevent production schedulers from seeing the full picture, leading to inaccurate or incomplete scheduling decisions.
Limited Real-Time Updates: Traditional tools lack the ability to reflect real-time changes in production, making it difficult to respond to unexpected disruptions.
Inefficient Resource Coordination: Without dynamic scheduling capabilities, resource utilization becomes suboptimal, resulting in costly idle time or overloading.
Inability to Simulate Scenarios: What-if analysis is critical for production planning, yet many tools lack the functionality to test different scenarios and identify the optimal path forward.

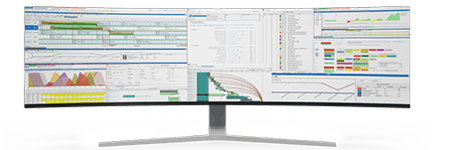
How PlanetTogether Elevates Schedule Visibility for Chemical Manufacturers
PlanetTogether, a leading Advanced Planning and Scheduling (APS) solution, empowers production schedulers to overcome these challenges and achieve real-time schedule visibility. When integrated with systems like SAP, Oracle, Microsoft, Kinaxis, or Aveva, PlanetTogether transforms fragmented planning workflows into a cohesive and transparent process.
Here's how PlanetTogether enhances schedule visibility and drives operational excellence in chemical manufacturing:
1. Seamless Data Integration
By integrating PlanetTogether with your ERP or Manufacturing Execution System (MES), you can eliminate data silos and enable a single source of truth for production scheduling. Real-time data flows between systems ensure that production schedules are always updated with the latest information, including:
Current inventory levels and material availability.
Equipment status and maintenance schedules.
Workforce availability and shift planning.
Customer orders and delivery timelines.
For example, a chemical manufacturer using SAP ERP can integrate PlanetTogether to pull live order data and synchronize schedules. This ensures production teams have immediate visibility into demand fluctuations and resource constraints.
2. Dynamic Scheduling Capabilities
PlanetTogether's APS platform provides production schedulers with dynamic scheduling tools that adjust in real time based on changing conditions. Whether equipment breaks down, raw materials are delayed, or a rush order is placed, schedulers can:
Instantly update schedules to reflect new constraints.
Prioritize tasks to minimize downtime and maintain delivery timelines.
Reshuffle resources without disrupting upstream or downstream processes.
With this level of agility, chemical manufacturers can respond proactively to disruptions and keep production plans on track.
3. Improved Resource Utilization
Effective resource management is at the heart of production scheduling. PlanetTogether provides powerful visibility into resource utilization, helping schedulers align equipment, labor, and materials to production priorities. By identifying and eliminating inefficiencies, manufacturers can:
Maximize equipment capacity without overloading machines.
Reduce idle time and bottlenecks.
Optimize labor schedules to meet demand without overstaffing.
Integration with systems like Aveva MES ensures real-time monitoring of equipment availability and production processes, further enhancing resource alignment.
4. Advanced Analytics and What-If Scenarios
Schedule visibility isn't just about seeing the current state—it's also about planning for the future. PlanetTogether enables production schedulers to perform advanced what-if analyses, allowing them to test different scenarios and determine the best course of action. Key benefits include:
Simulating the impact of schedule changes on production timelines.
Identifying potential risks and resolving bottlenecks before they occur.
Comparing multiple scheduling strategies to find the most efficient plan.
For example, a scheduler might use PlanetTogether to test the impact of shifting production from one batch process to another, ensuring on-time delivery while balancing equipment loads.
5. Enhanced Collaboration Across Teams
Schedule visibility is not limited to the production floor—it impacts stakeholders across procurement, logistics, maintenance, and customer service. PlanetTogether's intuitive interface provides role-based access to scheduling data, ensuring all teams are aligned. Integration with ERP platforms like Oracle or Microsoft Dynamics enables:
Procurement teams to coordinate raw material deliveries with production schedules.
Maintenance teams to schedule downtime without disrupting operations.
Customer service teams to provide accurate delivery timelines to clients.
By improving collaboration, chemical manufacturers can create a more streamlined and efficient scheduling process.
Schedule visibility is no longer a "nice-to-have" for chemical manufacturers—it's a requirement. Production schedulers play a critical role in ensuring smooth operations, and the right tools can empower them to make better decisions, optimize workflows, and drive efficiency.
PlanetTogether's integration with leading ERP platforms provides the clarity, control, and collaboration needed to overcome scheduling challenges and achieve operational excellence. If your chemical manufacturing facility is ready to elevate its scheduling processes, now is the time to explore the power of integrated planning solutions.
Are you ready to take your manufacturing operations to the next level? Contact us today to learn more about how PlanetTogether can help you achieve your goals and drive success in your industry.