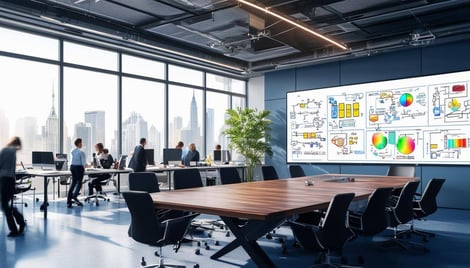
Enhancing Process Modeling in Pharmaceutical Manufacturing with PlanetTogether and ERP Integrations
Ensuring timely production, regulatory compliance, and cost-effectiveness often requires a delicate balancing act. Process modeling is at the heart of these operations, enabling schedulers to simulate, analyze, and optimize workflows. However, achieving seamless process modeling often demands robust tools and integrations.
Enter PlanetTogether, an advanced production scheduling and planning solution, and its potential integration with enterprise resource planning (ERP) systems like SAP, Oracle, Microsoft Dynamics, Kinaxis, or Aveva.
This blog explores how PlanetTogether, in conjunction with these ERP systems, can revolutionize process modeling for pharmaceutical production schedulers.
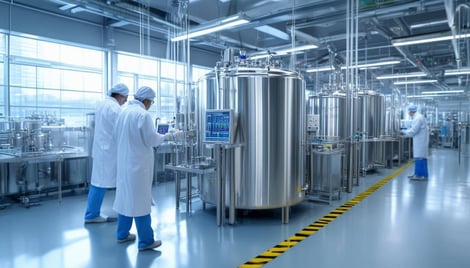
Process Modeling in Pharmaceutical Manufacturing
Process modeling involves creating digital representations of production workflows, allowing manufacturers to simulate and analyze operations. For pharmaceutical manufacturing, process modeling has several critical applications:
Regulatory Compliance: Ensuring adherence to stringent regulations like FDA’s cGMP (current Good Manufacturing Practices).
Resource Allocation: Optimizing the use of equipment, labor, and materials.
Batch Management: Planning and tracking batch production to prevent cross-contamination and ensure product quality.
Risk Assessment: Identifying potential bottlenecks or risks and implementing corrective actions proactively.
For production schedulers, process modeling is not just a tool—it’s a necessity to meet the dynamic demands of the pharmaceutical industry. However, traditional methods or siloed systems often fall short in delivering the agility and precision required.

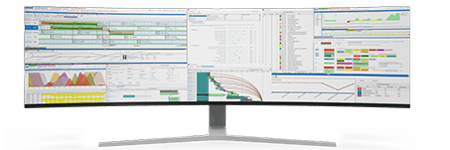
The Role of PlanetTogether in Process Modeling
PlanetTogether offers advanced features tailored to the needs of pharmaceutical manufacturers:
1. Dynamic Scheduling and Optimization
PlanetTogether allows schedulers to create dynamic schedules that adapt in real-time. For example, if a key resource becomes unavailable, the system can automatically reallocate tasks, ensuring minimal disruption.
2. Batch Scheduling
With PlanetTogether, production schedulers can model batch processes with precision, accounting for variables such as:
Lot sizes.
Cleaning and changeover times.
Regulatory requirements.
3. What-If Scenarios
Schedulers can simulate multiple scenarios to identify the most efficient and cost-effective production plan. For instance:
What happens if there’s a delay in raw material delivery?
How can production be scaled up to meet sudden demand surges?
4. Resource Utilization
The platform ensures optimal utilization of resources, such as:
Specialized equipment.
Skilled labor.
Critical raw materials.
5. Compliance and Traceability
PlanetTogether enhances traceability by linking production schedules with batch records, making it easier to comply with regulatory audits.
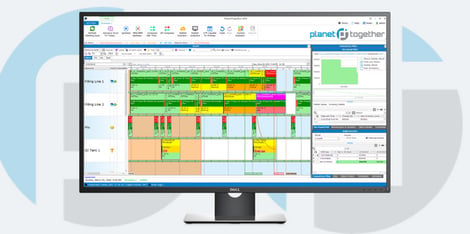
Integrating PlanetTogether with Leading ERP Systems
While PlanetTogether provides powerful process modeling capabilities, its true potential is unlocked when integrated with ERP systems. Let’s explore how integration with SAP, Oracle, Microsoft Dynamics, Kinaxis, or Aveva can enhance process modeling:
1. Real-Time Data Synchronization
Integration ensures seamless flow of data between PlanetTogether and ERP systems. For example:
SAP: PlanetTogether can pull real-time inventory levels and production orders from SAP, ensuring schedules are based on accurate data.
Oracle: Integration with Oracle’s supply chain modules allows schedulers to align production plans with broader business objectives.
2. Enhanced Visibility
By integrating with ERPs, PlanetTogether provides a unified view of operations:
Microsoft Dynamics: Combines production schedules with financial data for better cost analysis.
Aveva: Leverages Aveva’s process engineering tools to refine workflows further.
3. Predictive Analytics
ERP integrations enable advanced analytics. For example:
Kinaxis: Schedulers can leverage Kinaxis’ predictive models to forecast demand fluctuations and adjust production plans proactively.
4. Improved Collaboration
Integration fosters collaboration across departments:
Quality assurance teams can access production schedules for timely inspections.
Procurement teams can align raw material deliveries with production needs.
5. Streamlined Change Management
Changes in demand, regulations, or resources can be quickly reflected in production schedules, minimizing delays and errors.
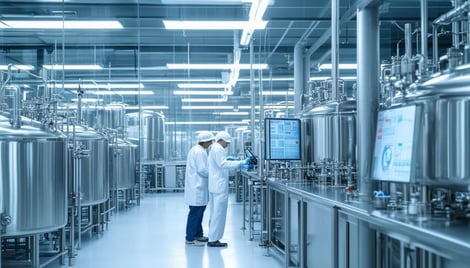
Best Practices for Implementation
To maximize the benefits of PlanetTogether and ERP integration, consider these best practices:
Define Clear Objectives: Identify specific goals, such as reducing changeover times or improving batch traceability.
Ensure Data Accuracy: Accurate data is critical for effective modeling and scheduling.
Train Your Team: Provide training for schedulers and other stakeholders to fully leverage the tools.
Monitor and Adjust: Regularly review and refine schedules based on real-time feedback.
Collaborate Across Departments: Foster communication between scheduling, procurement, and quality teams.
For production schedulers in pharmaceutical manufacturing, the integration of PlanetTogether with ERP systems like SAP, Oracle, Microsoft Dynamics, Kinaxis, or Aveva represents a game-changer. By enabling advanced process modeling, real-time data synchronization, and improved collaboration, these tools empower schedulers to navigate complex challenges with confidence.
Whether it’s optimizing batch schedules, ensuring regulatory compliance, or responding to sudden demand shifts, the combination of PlanetTogether and ERP integration delivers unmatched capabilities. As the industry moves towards greater digitalization, embracing these technologies will be essential for staying competitive and delivering high-quality pharmaceutical products efficiently.
Are you ready to take your manufacturing operations to the next level? Contact us today to learn more about how PlanetTogether can help you achieve your goals and drive success in your industry.