PDCA Cycle in Continuous Scheduling Improvement
Operations Directors constantly seek ways to optimize production processes, minimize waste, and meet customer demands promptly. Amidst the myriad of challenges, one methodology stands out for its effectiveness in driving continuous improvement – the PDCA (Plan-Do-Check-Act) cycle.
When integrated seamlessly with advanced scheduling systems like PlanetTogether and ERP, SCM, and MES systems such as SAP, Oracle, Microsoft, Kinaxis, or Aveva, the PDCA cycle becomes a formidable tool for enhancing scheduling efficiency.
In this blog, we'll explore the significance of the PDCA cycle in packaging manufacturing and how its integration with cutting-edge technologies can revolutionize scheduling practices.
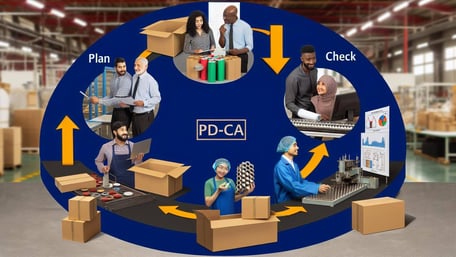
Understanding the PDCA Cycle
The PDCA cycle, popularized by W. Edwards Deming, is a systematic approach to problem-solving and continuous improvement. It consists of four interrelated steps:
Plan: In this phase, objectives and processes are established, along with the identification of potential areas for improvement. It involves setting goals, defining strategies, and creating action plans to achieve desired outcomes.
Do: Execution of the plan occurs in this phase. It involves implementing the proposed changes or improvements on a small scale, typically through pilot projects or experiments. Data is collected during this phase to assess the effectiveness of the changes.
Check: Evaluation of the results obtained from the implementation phase is conducted here. Data is analyzed to determine whether the desired outcomes were achieved, and to identify any deviations from the expected results.
Act: Based on the findings of the check phase, appropriate actions are taken. If the desired outcomes were achieved, the successful changes are standardized and integrated into the regular processes. If not, adjustments are made, and the cycle begins again.

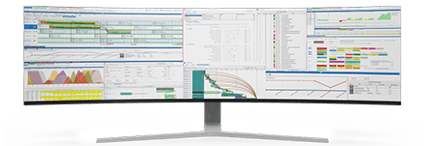
Integration of PDCA Cycle with Advanced Scheduling Systems
Now, let's look into how the PDCA cycle can be integrated with advanced scheduling systems like PlanetTogether, alongside ERP, SCM, and MES systems, to drive continuous scheduling improvement in packaging manufacturing facilities:
Plan: With the help of sophisticated scheduling software like PlanetTogether, Operations Directors can effectively plan and optimize production schedules. By analyzing historical data, customer orders, and resource availability, the software assists in developing comprehensive production plans that align with business objectives. Integration with ERP systems such as SAP or Oracle enables seamless transfer of data, ensuring accurate planning based on real-time information.
Do: Once the production plan is in place, the execution phase begins. Advanced scheduling systems facilitate the implementation of the plan by providing real-time visibility into production processes. Through features like drag-and-drop scheduling, resource allocation, and automated alerts, manufacturers can swiftly adapt to changing demands and optimize production efficiency. Integration with MES systems allows for the direct capture of shop floor data, enabling accurate tracking of progress and performance.
Check: The check phase involves evaluating the effectiveness of the implemented changes. Advanced scheduling systems offer robust reporting and analytics capabilities, allowing Operations Directors to assess key performance metrics such as production throughput, resource utilization, and on-time delivery. By comparing actual performance against planned targets, deviations can be identified, and areas for improvement pinpointed. Integration with SCM systems facilitates the analysis of supply chain data, enabling proactive identification of bottlenecks or constraints.
Act: Based on the insights gathered during the check phase, appropriate actions are taken to drive further improvements. Advanced scheduling systems support decision-making by providing scenario analysis and what-if simulations. Operations Directors can experiment with different scheduling strategies and evaluate their potential impact before implementing changes. Integration with Kinaxis or Aveva systems enables alignment of scheduling decisions with broader supply chain objectives, ensuring synchronization across the entire value chain.
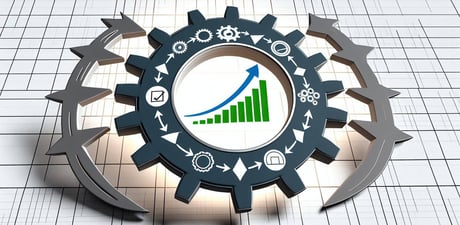
Benefits of Integrated PDCA Cycle and Advanced Scheduling Systems
The integration of the PDCA cycle with advanced scheduling systems and ERP, SCM, and MES systems offers several benefits for packaging manufacturing facilities:
Improved Efficiency: By continuously iterating through the PDCA cycle, organizations can identify and address inefficiencies in scheduling processes, leading to improved productivity and resource utilization.
Enhanced Agility: Advanced scheduling systems enable quick adaptation to changing market conditions and customer requirements, ensuring that production schedules remain responsive and flexible.
Optimized Resource Allocation: Integration with ERP and MES systems provides real-time visibility into resource availability and capacity constraints, allowing for optimal allocation of resources across production operations.
Data-Driven Decision Making: The integration of advanced analytics and reporting capabilities enables Operations Directors to make informed decisions based on actionable insights derived from production data.
Continuous Improvement Culture: By embedding the PDCA cycle into scheduling practices, organizations foster a culture of continuous improvement, where every iteration contributes to incremental enhancements in performance and efficiency.
The PDCA cycle serves as a powerful framework for driving continuous scheduling improvement in packaging manufacturing facilities. When integrated with advanced scheduling systems like PlanetTogether and ERP, SCM, and MES systems such as SAP, Oracle, Microsoft, Kinaxis, or Aveva, its effectiveness is further amplified.
By systematically planning, executing, evaluating, and acting upon scheduling decisions, Operations Directors can achieve greater efficiency, agility, and competitiveness in today's dynamic business environment.
Are you ready to take your manufacturing operations to the next level? Contact us today to learn more about how PlanetTogether can help you achieve your goals and drive success in your industry.