Order Fulfillment Performance Monitoring
The ability to fulfill orders promptly and accurately can make or break a company's reputation and profitability. In today's digitally-driven era, the convergence of Manufacturing Execution Systems (MES), Enterprise Resource Planning (ERP), and Supply Chain Management (SCM) solutions has revolutionized how manufacturers monitor and optimize their order fulfillment processes.
This blog looks into the significance of order fulfillment performance monitoring and explores how integration between PlanetTogether and leading ERP, SCM, and MES systems such as SAP, Oracle, Microsoft, Kinaxis, and Aveva is reshaping the manufacturing IT landscape.
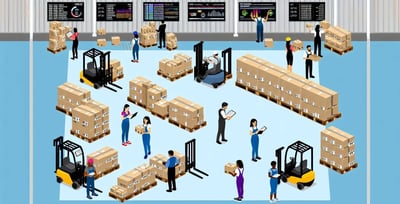
Understanding Order Fulfillment Performance Monitoring
Order fulfillment performance monitoring involves tracking and analyzing various metrics throughout the order processing lifecycle. These metrics include order cycle time, on-time delivery, inventory levels, production throughput, and resource utilization, among others.
Efficient order fulfillment relies on real-time visibility into manufacturing operations, seamless coordination between departments, and agile responses to changing demand and supply conditions. This necessitates the integration of disparate IT systems to enable data sharing, process automation, and decision support.
The Role of Manufacturing IT Integration
Manufacturing IT integration refers to the seamless connectivity between different software applications used across the production ecosystem. By integrating MES, ERP, and SCM systems, manufacturers can achieve end-to-end visibility and control over their operations, leading to enhanced order fulfillment performance.
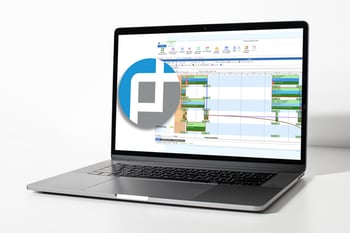
Leveraging PlanetTogether for Production Planning and Scheduling
PlanetTogether is a powerful Production Planning and Scheduling (PPS) software designed to optimize manufacturing processes. It offers advanced features such as capacity planning, constraint-based scheduling, what-if analysis, and scenario planning, enabling manufacturers to optimize resource utilization and minimize lead times.
Integration with ERP Systems: Streamlining Data Flow
Enterprise Resource Planning (ERP) systems serve as the backbone of manufacturing operations, managing core business functions such as finance, procurement, inventory, and order management. Integrating PlanetTogether with leading ERP platforms like SAP, Oracle, and Microsoft Dynamics enables seamless data exchange between production planning/scheduling and other business processes.
Through integration, production plans generated in PlanetTogether can be synchronized with ERP systems, ensuring accurate material availability, labor allocation, and production scheduling. This alignment improves order fulfillment accuracy and reduces the risk of stockouts or overstock situations.
Integration with SCM Systems: Enhancing Supply Chain Visibility
Supply Chain Management (SCM) systems play a crucial role in coordinating the flow of materials, information, and finances across the supply chain network. Integrating PlanetTogether with SCM solutions such as Kinaxis and Aveva enables manufacturers to synchronize production plans with demand forecasts, supplier schedules, and logistics operations.
By aligning production schedules with supply chain dynamics, manufacturers can minimize lead times, optimize inventory levels, and mitigate disruptions, thereby improving order fulfillment performance and customer satisfaction.
Integration with MES Systems: Bridging the Shop Floor Divide
Manufacturing Execution Systems (MES) provide real-time visibility and control over shop floor operations, including machine monitoring, labor tracking, quality management, and workflow automation. Integrating PlanetTogether with MES solutions ensures seamless coordination between production planning/scheduling and shop floor execution.
Real-time data exchange between PlanetTogether and MES systems enables dynamic scheduling adjustments based on actual production status, resource availability, and quality issues. This agile responsiveness improves order fulfillment agility and enables Just-in-Time (JIT) manufacturing practices.
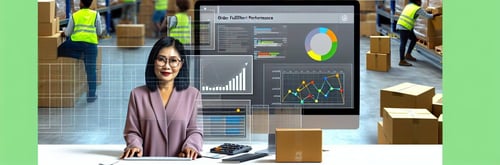
Benefits of Integrated Order Fulfillment Performance Monitoring
Improved Efficiency: Integration between PlanetTogether and ERP/SCM/MES systems streamlines data flow, eliminates manual data entry, and reduces process latency, thereby improving overall operational efficiency.
Enhanced Visibility: End-to-end visibility into order fulfillment processes enables proactive decision-making, timely interventions, and continuous performance improvement across the production ecosystem.
Optimized Resource Utilization: By synchronizing production plans with resource availability and demand fluctuations, manufacturers can optimize resource utilization, minimize idle time, and maximize throughput.
Reduced Lead Times: Seamless integration facilitates faster order processing, shorter lead times, and on-time delivery, thereby enhancing customer satisfaction and loyalty.
Agile Responsiveness: Real-time data exchange and dynamic scheduling adjustments enable agile responses to changing market conditions, customer demands, and supply chain disruptions.
Order fulfillment performance monitoring is critical for achieving operational excellence and competitive advantage in industrial manufacturing. By integrating PlanetTogether with leading ERP, SCM, and MES systems, manufacturers can enhance visibility, efficiency, and agility across the order fulfillment lifecycle.
Seamless data exchange, process automation, and decision support capabilities enable manufacturers to optimize resource utilization, minimize lead times, and deliver superior customer experiences. As manufacturing IT continues to evolve, integrated order fulfillment performance monitoring will remain a cornerstone of success in the Industry 4.0 era.
Are you ready to take your manufacturing operations to the next level? Contact us today to learn more about how PlanetTogether can help you achieve your goals and drive success in your industry.