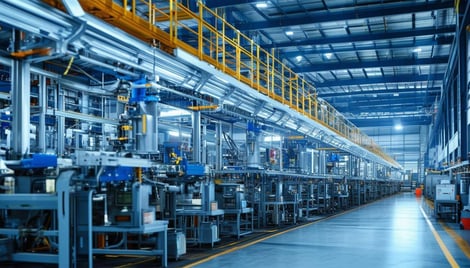
Enhancing Flexibility in Industrial Manufacturing: The Role of Advanced Planning Systems
Flexibility has become the cornerstone of success in industrial manufacturing. With fluctuating market demands, supply chain disruptions, and the ever-evolving regulatory landscape, Plant Managers are under constant pressure to maintain operational efficiency while ensuring agility.
One of the most transformative tools in achieving this balance is the integration of advanced planning and scheduling systems, such as PlanetTogether, with enterprise resource planning (ERP) platforms like SAP, Oracle, Microsoft, Kinaxis, or Aveva.
This integration empowers manufacturing facilities to adapt quickly, optimize resources, and maintain a competitive edge.
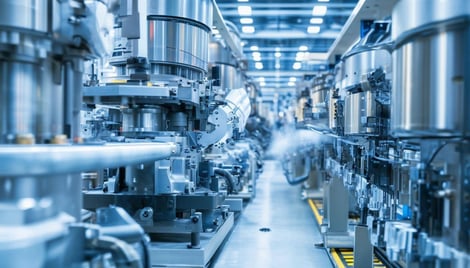
The Need for Flexibility in Modern Manufacturing
Industrial manufacturing has entered an era of rapid change. Globalization, digital transformation, and customer demand for personalized products have necessitated a shift from rigid, linear production processes to more dynamic and adaptable systems. For Plant Managers, the primary challenge lies in navigating these complexities while meeting production targets and minimizing downtime.
Flexibility in manufacturing refers to the ability to respond swiftly to changes without compromising quality or efficiency. This could involve adjusting production schedules, reallocating resources, or scaling operations up or down based on demand. However, achieving this level of agility requires real-time data, seamless communication between systems, and robust planning capabilities—areas where integrated solutions shine.
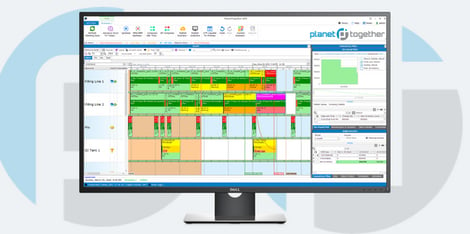
Unlocking Flexibility with PlanetTogether and ERP Integration
PlanetTogether Advanced Planning and Scheduling (APS) software is designed to enhance operational efficiency by optimizing production schedules, balancing workloads, and improving resource utilization. When integrated with ERP systems like SAP, Oracle, Microsoft Dynamics, Kinaxis, or Aveva, the results can be transformative. Here’s how this integration drives flexibility:
Real-Time Data Synchronization
Integration ensures that data flows seamlessly between PlanetTogether and the ERP system. This real-time synchronization eliminates the delays and inaccuracies associated with manual data entry. For example, a sudden change in customer demand captured in the ERP system can instantly reflect in PlanetTogether, allowing for immediate adjustments to production schedules.
Enhanced Visibility Across Operations
By combining the macro-level insights of an ERP system with the detailed scheduling capabilities of PlanetTogether, Plant Managers gain a comprehensive view of operations. This visibility enables better decision-making, such as identifying bottlenecks, reallocating resources, or rescheduling tasks to meet delivery timelines.
Scenario Planning and Optimization
PlanetTogether’s integration with ERP platforms facilitates scenario planning. Plant Managers can simulate various “what-if” scenarios, such as a sudden equipment breakdown or a spike in raw material costs, and evaluate their impact on production. This proactive approach allows for the development of contingency plans, ensuring minimal disruption.
Improved Resource Utilization
Flexibility isn’t just about adapting to changes; it’s also about maximizing the use of available resources. PlanetTogether’s scheduling algorithms, when combined with ERP data, optimize machine and labor utilization. For instance, if an ERP system indicates a surge in orders, PlanetTogether can adjust shifts and reassign resources to meet the demand without overburdening staff.
Streamlined Communication
Integration bridges the gap between the shop floor and management. With PlanetTogether and ERP systems working in tandem, Plant Managers can ensure that production teams are aligned with broader business objectives. Automated notifications and updates reduce the risk of miscommunication, enabling a more cohesive operation.
Overcoming Implementation Challenges
While the benefits of integrating PlanetTogether with ERP systems are clear, the implementation process can present challenges. Plant Managers must navigate potential obstacles such as:
Data Silos: Ensuring that data from various departments is accessible and compatible with both systems.
Resistance to Change: Addressing employee concerns about adopting new technologies and workflows.
Customization Needs: Tailoring the integration to meet the specific needs of the facility.
To overcome these challenges, it is crucial to partner with experienced implementation teams and invest in comprehensive training for staff. Additionally, phased rollouts can help minimize disruptions during the transition.
In the competitive landscape of industrial manufacturing, flexibility is no longer a luxury—it’s a must. Integrating advanced planning systems like PlanetTogether with ERP platforms such as SAP, Oracle, Microsoft, Kinaxis, or Aveva equips Plant Managers with the tools they need to adapt, optimize, and thrive.
By embracing this integration, facilities can achieve real-time responsiveness, better resource utilization, and improved operational efficiency. As the manufacturing sector continues to evolve, those who invest in flexible, data-driven solutions will be best positioned to succeed in the face of uncertainty.
Are you ready to take your manufacturing operations to the next level? Contact us today to learn more about how PlanetTogether can help you achieve your goals and drive success in your industry.
LEAVE A COMMENT