Leveraging Partnerships and Supplier Agreements
Production planners play a pivotal role in ensuring smooth operations, optimizing resources, and meeting customer demands. In recent years, the industry has witnessed a shift towards collaborative partnerships and innovative supplier agreements to streamline processes and drive efficiency.
In this blog, we explore how production planners can leverage partnerships and supplier agreements, along with the integration between Planettogether and leading enterprise resource planning (ERP) systems like SAP, Oracle, Microsoft, Kinaxis, and Aveva, to achieve operational excellence.
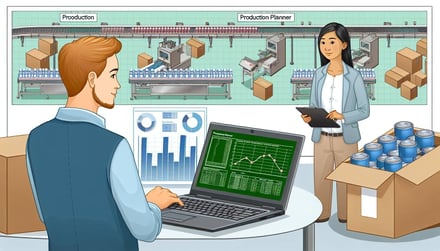
The Role of Production Planners
Production planners are tasked with balancing supply and demand, optimizing production schedules, managing inventory levels, and ensuring timely delivery of products. They are the linchpin between various departments within a manufacturing facility and external suppliers. To excel in their role, production planners need access to real-time data, advanced planning tools, and seamless communication channels.
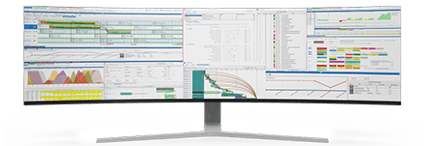
Integration between Planettogether and ERP Systems
Planettogether is a powerful production planning and scheduling software designed to streamline manufacturing operations. By integrating with leading ERP systems such as SAP, Oracle, Microsoft Dynamics, Kinaxis RapidResponse, and Aveva, production planners can harness the full potential of both platforms. This integration enables seamless data exchange, synchronized workflows, and enhanced visibility across the supply chain.
Benefits of Integration
Real-Time Data Sync: Integration between Planettogether and ERP systems ensures that production planners have access to real-time data on inventory levels, order status, and production capacity. This enables them to make informed decisions and adjust schedules accordingly.
Streamlined Workflows: With data seamlessly flowing between Planettogether and ERP systems, production planners can streamline workflows and eliminate manual data entry tasks. This not only saves time but also reduces the risk of errors.
Enhanced Visibility: Integration provides production planners with a holistic view of the entire production process, from raw material procurement to finished goods delivery. This visibility allows them to identify bottlenecks, anticipate potential issues, and proactively address them.
Improved Collaboration: By facilitating communication and collaboration between different departments and external suppliers, integration fosters a culture of teamwork and agility. Production planners can coordinate with procurement, production, and logistics teams more effectively, ensuring alignment and synchronization across the supply chain.
Optimized Resource Utilization: With accurate demand forecasting and production scheduling capabilities, production planners can optimize resource utilization and minimize waste. This leads to cost savings and improved profitability for the organization.
Food and beverage manufacturers must continuously strive for efficiency and agility to stay ahead of the curve. By forging strategic partnerships and embracing innovative supplier agreements, production planners can unlock new opportunities for optimization and growth. Integration between Planettogether and leading ERP systems acts as a catalyst, enabling seamless collaboration, data-driven decision-making, and operational excellence across the supply chain.
As we look towards the future, the importance of partnerships and collaboration in driving efficiency cannot be overstated. By working together, we can create a more resilient and sustainable food and beverage industry for generations to come.
Are you ready to take your manufacturing operations to the next level? Contact us today to learn more about how PlanetTogether can help you achieve your goals and drive success in your industry.