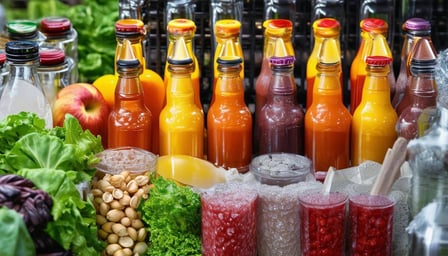
Embracing the Circular Economy and Sustainability in Food and Beverage Manufacturing
Sustainability is no longer an option but a critical business imperative in food and beverage manufacturing. Plant Managers are at the forefront of implementing sustainable practices, faced with the challenge of reducing waste, optimizing resources, and meeting increasing regulatory requirements. Central to achieving these goals is embracing a circular economy approach, which aims to eliminate waste and encourage the continual use of resources. This shift not only drives positive environmental impact but also offers potential for significant cost savings and efficiency improvements.
Advanced manufacturing technologies, such as PlanetTogether, paired with robust ERP systems like SAP, Oracle, Microsoft, Kinaxis, or Aveva, empower Plant Managers to operationalize sustainability in real time. Through seamless integration, these systems can help you optimize production processes, track waste, and even predict potential inefficiencies.
Here’s how adopting a circular economy approach in food and beverage manufacturing, supported by the right technological integration, can transform your facility’s sustainability initiatives and drive long-term success.
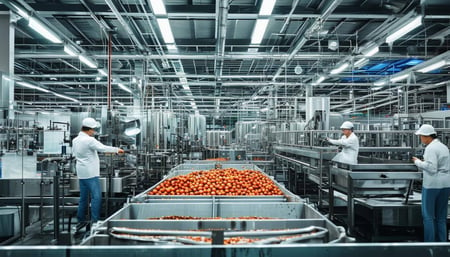
Circular Economy in Food and Beverage Manufacturing
The circular economy model revolves around reducing waste and reusing resources. In food and beverage manufacturing, this might mean converting by-products into new inputs, rethinking packaging solutions, or streamlining logistics to minimize carbon emissions. Here’s a closer look at some key circular economy principles that apply directly to food and beverage manufacturing:
Elimination of Waste and Pollution: Redesign production processes to prevent waste and pollution from the outset.
Product and Material Lifecycle Management: Extend the lifespan of equipment, ingredients, and packaging, ensuring they remain in use for as long as possible.
Natural Systems Regeneration: Utilize regenerative processes, such as recycling or composting, to return resources to the environment safely.
To effectively implement these principles, it is crucial to have visibility and control over each stage of the production process. Integrating advanced production planning tools like PlanetTogether with established ERP systems, such as SAP, Oracle, or Microsoft, provides a powerful solution to this challenge.

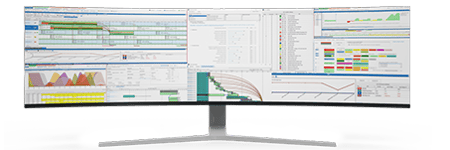
Leveraging PlanetTogether Integration for Sustainability Goals
Integrating PlanetTogether with systems like SAP, Oracle, Microsoft, Kinaxis, or Aveva allows for a more dynamic and responsive production environment. It offers real-time visibility into your entire supply chain and manufacturing process, helping you make informed, sustainable decisions. Let’s explore some specific ways this integration supports circular economy practices.
Optimizing Production Scheduling to Minimize Waste
In food and beverage manufacturing, ingredient spoilage, overproduction, and machine downtime are among the top causes of waste. By connecting PlanetTogether with ERP systems such as SAP or Oracle, Plant Managers gain a centralized view of production schedules, inventory levels, and machine performance. This integration enables you to:
Reduce Overproduction: Real-time data from your ERP system allows PlanetTogether to adjust production schedules based on demand forecasts, reducing overproduction and excess inventory.
Improve Machine Efficiency: Integrating machine data from systems like Aveva or Microsoft ensures timely maintenance, reducing the likelihood of equipment failure and downtime.
Track and Reduce Waste: With complete visibility into waste at every stage, you can identify inefficiencies in the process and make data-driven adjustments to reduce waste output.
This enhanced scheduling capability not only reduces waste but also improves operational efficiency, making it easier to meet sustainability targets while optimizing production output.
Real-Time Inventory Management for Reduced Waste and Spoilage
Managing ingredients and materials is one of the biggest challenges in the food and beverage industry, where spoilage can have a significant financial and environmental impact. Integrating PlanetTogether with inventory systems in SAP, Oracle, or Kinaxis helps Plant Managers control ingredient lifecycles more effectively. Here’s how:
Batch Tracking and Expiry Management: Integration with ERP systems enables accurate tracking of ingredient expiry dates, allowing you to prioritize older batches in the production cycle, reducing spoilage.
On-Demand Production Adjustments: With data from PlanetTogether’s integration, you can adjust production in real-time based on ingredient availability, thereby minimizing the risk of waste due to expired materials.
Inventory Optimization: Real-time inventory insights allow you to maintain optimal stock levels, reducing both overstock and stockouts, which further reduces waste and saves costs.
This type of intelligent inventory management aligns directly with circular economy goals by reducing waste and maximizing resource utilization.
Enhancing Resource Efficiency through Data-Driven Decisions
A significant part of the circular economy is maximizing resource efficiency. Integrating PlanetTogether with systems like Microsoft or SAP enables detailed resource monitoring and predictive analytics, helping Plant Managers to allocate resources precisely where they are needed most. This integration aids in:
Predictive Maintenance: By analyzing machine performance data in real-time, you can predict maintenance needs before breakdowns occur, reducing both waste and resource consumption.
Energy Management: Data from integrated systems helps you monitor energy use, identifying areas for energy conservation. This can result in not only environmental benefits but also significant cost savings.
Sustainable Supplier Management: ERP systems with integrated supply chain data allow you to choose suppliers based on their sustainability practices and align with circular economy principles.
With precise data from these systems, Plant Managers can make informed decisions to conserve resources, reduce emissions, and contribute to overall sustainability goals.
Transforming By-Products into New Value Streams
One of the core elements of the circular economy is turning by-products into valuable resources. In the food and beverage industry, many by-products can be repurposed, such as turning waste grain from brewing into animal feed or fertilizer. PlanetTogether, integrated with an ERP system like SAP or Oracle, can facilitate the efficient management and tracking of by-products, enabling you to explore new value streams. For example:
By-Product Inventory Tracking: Keep track of by-product volumes and integrate this data into your ERP to identify potential uses or sales opportunities.
Supplier and Customer Collaboration: Connect with suppliers and customers who are interested in purchasing or utilizing your by-products, creating a closed-loop system.
Data-Driven Innovation: Use analytics from the integrated system to identify trends and develop new sustainable products from existing waste streams.
Through this approach, Plant Managers can discover innovative ways to generate value from by-products, reducing waste while increasing profitability.
Supporting Compliance and Reporting through Seamless Data Integration
As sustainability regulations become stricter, the ability to accurately report on environmental impact is crucial. An integrated system with PlanetTogether and ERP software like Aveva, SAP, or Microsoft provides a single source of truth for your data, making it easier to compile reports and meet compliance requirements. With this integration, Plant Managers can:
Track Sustainability KPIs: Monitor metrics such as energy use, emissions, and waste reduction efforts in real-time.
Automate Compliance Reporting: Generate reports for regulatory bodies, showcasing your commitment to sustainability and adherence to local and international standards.
Transparency for Stakeholders: Share data-backed sustainability achievements with stakeholders, improving brand reputation and customer trust.
This streamlined approach to compliance ensures that your facility remains compliant and transparent while contributing to broader circular economy goals.
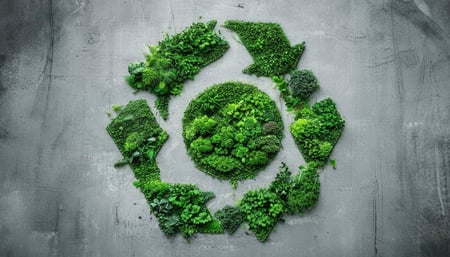
Implementing the Circular Economy: Steps for Success
To truly reap the benefits of a circular economy approach, integrating PlanetTogether with ERP systems is a step in the right direction. However, achieving sustainable success requires a strategic plan. Here are a few steps to get started:
Conduct a Sustainability Audit: Evaluate your current production process and identify key areas for improvement in waste reduction, resource efficiency, and energy consumption.
Develop Key Performance Indicators (KPIs): Define sustainability KPIs aligned with circular economy principles, such as waste reduction targets, energy efficiency goals, and by-product utilization rates.
Engage Stakeholders and Suppliers: Collaborate with suppliers and stakeholders to build a network committed to sustainability. Leveraging data from PlanetTogether can strengthen partnerships and provide insights to enhance supplier accountability.
Train Your Team: Ensure all staff are aware of circular economy practices and their role in achieving sustainability goals. PlanetTogether’s integration makes it easy to track real-time data, but its value is maximized when your team understands how to leverage this information effectively.
Monitor, Analyze, and Adjust: Sustainability is a journey, and continual improvement is key. Regularly analyze data from PlanetTogether and your ERP to assess progress and make necessary adjustments.
Adopting a circular economy approach in food and beverage manufacturing is essential for meeting today’s sustainability demands. With PlanetTogether’s integration with ERP systems like SAP, Oracle, Microsoft, Kinaxis, and Aveva, Plant Managers gain the tools they need to optimize production, minimize waste, and achieve long-term resource efficiency. By leveraging these advanced integration solutions, food and beverage manufacturers can not only reduce their environmental impact but also improve profitability and build a resilient, future-ready business model.
As a Plant Manager, embracing these changes and leading the shift toward circularity positions your facility for success in an increasingly eco-conscious market. Are you ready to take your manufacturing operations to the next level? Contact us today to learn more about how PlanetTogether and integrated scheduling solutions can help you achieve your sustainability goals and drive success.