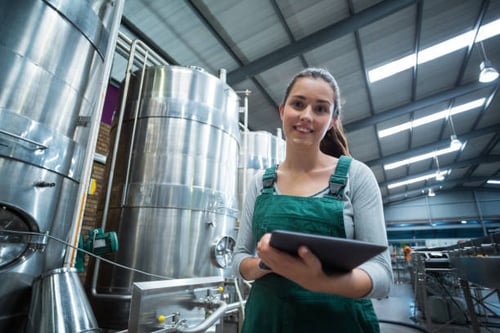
Embracing Technology for Smarter Supplier and Inventory Management in Food & Beverage Manufacturing
In Food and Beverage (F&B) manufacturing, the role of Purchasing Managers has never been more critical—or more complex. Increasing demand variability, tighter regulatory oversight, and global supply chain disruptions make supplier coordination and inventory oversight a daunting task. The good news? Technological advancements, especially in Advanced Planning and Scheduling (APS) and ERP integration, are transforming these challenges into strategic advantages.
One such technology that is making a significant impact is PlanetTogether APS, particularly when integrated with ERP platforms such as SAP, Oracle, Microsoft Dynamics, Kinaxis, or Aveva. This integration empowers Purchasing Managers to synchronize procurement with production plans, manage supplier risks more proactively, and optimize inventory levels with unprecedented precision.
This blog explores how adopting technology can revolutionize supplier and inventory management in the F&B sector—bringing greater agility, visibility, and cost control to the purchasing function.
The Evolving Role of the Purchasing Manager
Gone are the days when purchasing was a transactional function focused solely on cost savings. Today’s Purchasing Managers in the F&B sector are strategic collaborators—balancing quality assurance, supplier reliability, production alignment, and regulatory compliance. With perishable goods and fluctuating demand cycles, even slight misalignments between procurement and production schedules can result in spoilage, stockouts, or excessive working capital.
Technology adoption, therefore, is not just an efficiency play—it’s a necessity for survival.
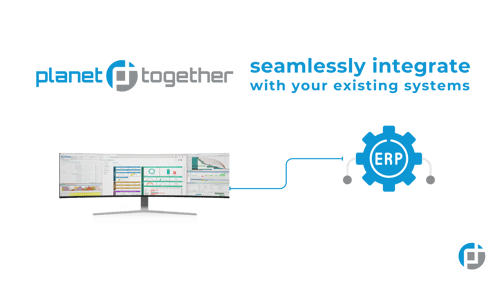
Technology as the Enabler: The PlanetTogether Advantage
At the heart of smart procurement lies real-time data synchronization and predictive planning, both made possible through the integration of PlanetTogether APS with core ERP systems like SAP, Oracle, Microsoft Dynamics, Kinaxis, or Aveva.
Key Benefits:
End-to-End Supply Chain Visibility
By integrating PlanetTogether with your ERP system, you gain real-time visibility into material requirements, supplier lead times, and inventory levels.
This transparency allows Purchasing Managers to make informed decisions quickly—anticipating shortages or adjusting orders before disruptions occur.
Synchronized Procurement and Production
APS tools like PlanetTogether help generate optimized production schedules that directly inform procurement needs.
With real-time feedback loops between PlanetTogether and systems like SAP or Oracle, purchasing aligns with actual, dynamic production schedules—not outdated forecasts.
Optimized Inventory Management
Overstocking ties up capital and risks spoilage; understocking halts production. Integration ensures just-in-time procurement that balances both extremes.
Forecasting modules using AI and machine learning (especially in Kinaxis and Microsoft environments) refine predictions as new data flows in.
Supplier Performance Analytics
With ERP-integrated APS, supplier performance data—on-time deliveries, quality metrics, responsiveness—can be tracked and visualized.
This supports smarter sourcing decisions and strengthens vendor negotiations.
Risk Mitigation Through Scenario Planning
What happens if a supplier fails to deliver on time? PlanetTogether lets you run "what-if" scenarios to simulate outcomes and prepare alternate plans.
These insights are invaluable when integrated into broader business continuity planning in Aveva or SAP systems.
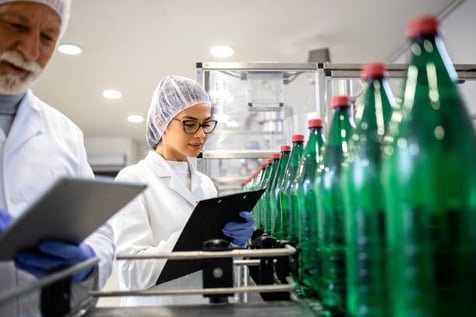
Implementation Considerations
While the benefits are compelling, adopting these technologies requires careful planning.
Change Management
Equip procurement teams with the right training to adapt to tech-driven workflows.
Encourage cross-functional collaboration between purchasing, production, and IT.
Integration Strategy
Work closely with integration experts to ensure seamless data exchange between PlanetTogether and your ERP system—be it Oracle or Kinaxis.
Consider middleware or APIs that enable flexibility without heavy IT overhauls.
Data Hygiene
The quality of your output depends on your input. Ensure supplier master data, lead times, and inventory records are accurate and up to date.
Pilot Programs
Start with a single product line or supplier category to validate the integration and measure ROI before full-scale rollout.
Supplier and inventory management are no longer back-office functions—they are strategic levers of competitiveness, especially in the F&B industry. By integrating PlanetTogether APS with leading ERP platforms like SAP, Oracle, Microsoft Dynamics, Kinaxis, or Aveva, Purchasing Managers can move from reactive firefighting to proactive planning.
Adopting these technologies enhances supplier collaboration, optimizes inventory levels, and ultimately drives better business outcomes. For the F&B sector—where freshness, timing, and cost efficiency are everything—there’s no better time to embrace a digital-first procurement strategy.
Ready to take your supplier and inventory management to the next level?
Consider starting with a tailored PlanetTogether integration. Contact us today to learn more about how PlanetTogether can fit in your current ERP ecosystem and business goals. Because when procurement aligns with planning, profitability follows.
LEAVE A COMMENT