Embracing Circular Economy Principles
The concept of a circular economy is rapidly gaining traction in industrial manufacturing. As sustainability becomes an increasingly pressing concern, companies are reevaluating their production processes to minimize waste, reduce environmental impact, and optimize resource utilization. At the heart of this transformation lies production planning – the cornerstone of operational efficiency in any manufacturing facility.
For Operations Directors navigating this evolving landscape, integrating circular economy principles into production planning is not just a choice but a necessity.
In this blog, we look into the significance of circular economy principles in production planning, and how leveraging advanced technologies such as PlanetTogether integrated with ERP, SCM, and MES systems can drive this transformative agenda forward.
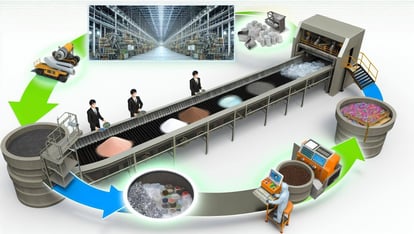
Understanding Circular Economy Principles
The traditional linear economy model, characterized by the "take-make-dispose" approach, is inherently unsustainable. It relies on the constant extraction of resources, leading to environmental degradation and resource depletion. In contrast, the circular economy model aims to minimize waste and maximize the value of resources by promoting reuse, recycling, and regeneration.
In production planning, embracing circular economy principles involves adopting strategies to:
Optimize Resource Utilization: Efficiently manage resources to minimize waste and maximize value throughout the production process.
Design for Sustainability: Integrate sustainability considerations into product design, ensuring products are durable, repairable, and recyclable.
Closed-Loop Systems: Establish closed-loop systems where materials are reused, recycled, or repurposed to minimize the need for virgin resources.
Supply Chain Collaboration: Collaborate with suppliers and partners to optimize the flow of materials and minimize environmental impact across the supply chain.
Data-Driven Decision Making: Utilize data analytics and real-time insights to identify opportunities for improvement and drive continuous optimization.
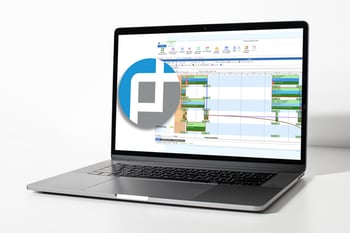
Integration of PlanetTogether with ERP, SCM, and MES Systems
To effectively implement circular economy principles in production planning, seamless integration between advanced planning and scheduling (APS) software like PlanetTogether and ERP, SCM, and MES systems is paramount. Here's how such integration can facilitate the transition towards a circular economy:
Real-Time Data Exchange: Integration allows for the seamless exchange of data between production planning and other systems, providing a holistic view of operations in real-time. This enables better decision-making and optimization of resources.
Enhanced Visibility: By integrating with ERP systems such as SAP, Oracle, or Microsoft Dynamics, PlanetTogether gains access to critical data related to inventory levels, material availability, and customer demand. This enhanced visibility enables more accurate production planning and reduces the risk of overstocking or stockouts.
Streamlined Workflows: Integration streamlines workflows by automating data transfer between systems, eliminating manual errors, and reducing administrative overhead. This ensures that production plans align seamlessly with procurement, inventory management, and order fulfillment processes.
Improved Responsiveness: Integration with MES systems enables real-time monitoring of production processes, allowing for immediate adjustments in response to changing demand or resource availability. This agility is crucial for adapting to dynamic market conditions while minimizing waste.
Predictive Analytics: Leveraging data from ERP and SCM systems, integrated APS software can perform predictive analytics to anticipate future demand, optimize inventory levels, and proactively identify opportunities for resource optimization.
As an Operations Director in an industrial manufacturing facility, embracing circular economy principles in production planning is not just a strategic imperative but a moral obligation. By integrating advanced planning and scheduling software like PlanetTogether with ERP, SCM, and MES systems, you can drive the transition towards a more sustainable and efficient manufacturing ecosystem.
The journey towards a circular economy may present challenges, but the rewards are immense – from cost savings and operational efficiency to environmental stewardship and social responsibility. By leveraging technology, collaboration, and innovation, you have the power to revolutionize production planning and pave the way for a brighter, more sustainable future.
Are you ready to take your manufacturing operations to the next level? Contact us today to learn more about how PlanetTogether can help you achieve your goals and drive success in your industry.
LEAVE A COMMENT