Electrification and Decarbonization of Product Portfolios
As the world continues to grapple with climate change, industries are increasingly turning their attention toward sustainability initiatives. For plant managers in industrial manufacturing facilities, this trend isn’t just a passing fad—it’s a strategic imperative. Electrification and decarbonization are now essential for product portfolio management, customer satisfaction, regulatory compliance, and long-term profitability.
These initiatives involve adopting new technologies, rethinking operational processes, and often integrating advanced planning and scheduling systems like PlanetTogether with enterprise resource planning (ERP) solutions such as SAP, Oracle, Microsoft Dynamics, Kinaxis, and Aveva.
This blog will explore how electrification and decarbonization efforts impact industrial manufacturing facilities, the challenges and opportunities they present, and how the integration of advanced software solutions can support these initiatives.
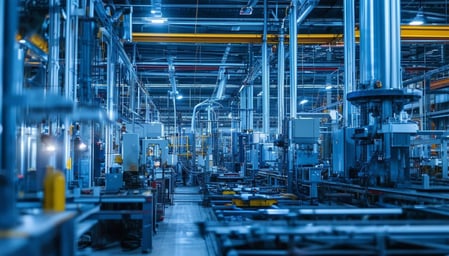
Why Electrification and Decarbonization Matter in Manufacturing
Decarbonization involves reducing carbon emissions from production processes, either through energy efficiency measures or by adopting cleaner energy sources. Electrification refers to the shift from fossil fuels to electricity in powering industrial processes, vehicles, and heating systems. Together, they offer pathways toward a more sustainable, lower-carbon future.
Several factors are driving this shift:
Regulatory Pressure: Governments across the globe are implementing stricter regulations to curb carbon emissions, with many setting ambitious goals to reach net-zero emissions by 2050. Industrial manufacturing facilities, which are often large carbon emitters, are under increasing scrutiny.
Consumer Demand: End consumers are more environmentally conscious than ever before. Companies that can offer greener products—produced with less environmental impact—gain a competitive edge in the market.
Operational Efficiency: Electrification and decarbonization can lead to increased energy efficiency, reducing both costs and the environmental footprint of manufacturing operations.
Corporate Sustainability Goals: Many companies have set their own sustainability targets, recognizing that a commitment to reducing carbon emissions aligns with long-term business resilience and brand reputation.
For a plant manager overseeing an industrial manufacturing facility, electrification and decarbonization aren’t just nice-to-have strategies—they’re essential for maintaining regulatory compliance, meeting customer expectations, and ensuring the facility remains competitive in the marketplace.
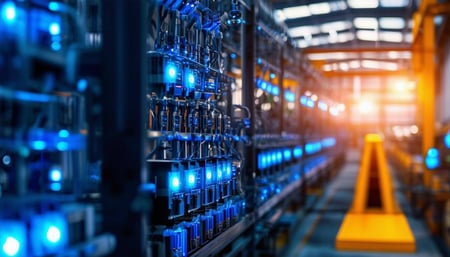
Challenges in Implementing Electrification and Decarbonization
While the benefits of electrification and decarbonization are clear, implementing these strategies can be challenging for several reasons:
Cost of Transition: Shifting from fossil fuels to electricity often requires significant capital investment in new equipment and infrastructure. Plant managers need to navigate the cost-benefit analysis carefully, considering the long-term savings against the upfront costs.
Energy Infrastructure: Industrial facilities are often large consumers of energy, and the local electrical grid may not have the capacity to meet increased demand from electrification efforts. Furthermore, the intermittency of renewable energy sources like solar and wind can complicate efforts to decarbonize.
Operational Disruptions: Retrofitting or replacing fossil fuel-powered equipment with electrical alternatives can disrupt production schedules. Careful planning is essential to minimize downtime and ensure a smooth transition.
Supply Chain Complications: Many decarbonization efforts involve sourcing new, more sustainable materials, which can add complexity to an already intricate supply chain.
Lack of Expertise: Electrification and decarbonization are relatively new fields for many manufacturers. Finding the right talent to lead and manage these initiatives can be difficult.
Despite these challenges, the pressure to decarbonize is only increasing. Plant managers must leverage advanced technology and strategic partnerships to overcome these hurdles.

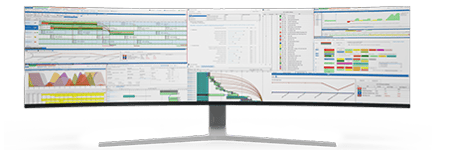
The Role of Technology in Facilitating Electrification and Decarbonization
To manage the complexities of electrification and decarbonization, plant managers must embrace digital transformation. Software platforms like PlanetTogether Advanced Planning and Scheduling (APS), when integrated with ERP systems such as SAP, Oracle, Microsoft Dynamics, Kinaxis, and Aveva, provide powerful tools to optimize production while aligning with sustainability goals.
Data-Driven Decision Making
Electrification and decarbonization require detailed data to track energy consumption, emissions, and the environmental impact of each production process. A solution like PlanetTogether can provide real-time data and insights on production efficiency, energy use, and carbon emissions.
When integrated with ERP systems like SAP or Oracle, this data can be extended across the entire enterprise, allowing plant managers to align operational decisions with broader business strategies. By centralizing data from production lines, supply chains, and energy sources, the plant manager gains visibility over the environmental footprint of the facility’s operations.
For example, integrating PlanetTogether with SAP enables real-time tracking of energy consumption at each stage of the production process, from raw materials to finished goods. This allows plant managers to identify inefficiencies and adjust production schedules to reduce energy use, optimize resource allocation, and minimize carbon emissions.
Optimizing Energy Efficiency
Energy consumption is one of the biggest drivers of carbon emissions in industrial manufacturing. Through the use of advanced scheduling and planning software like PlanetTogether, plant managers can optimize production processes to reduce energy consumption.
For instance, an integration between PlanetTogether and Microsoft Dynamics can provide plant managers with the ability to synchronize production schedules with periods of low electricity demand, taking advantage of off-peak energy prices. This not only reduces costs but also minimizes the strain on the energy grid, making it easier to incorporate renewable energy sources like wind or solar.
Moreover, PlanetTogether’s scheduling algorithms can be used to balance production loads, ensuring that machines are run at optimal efficiency. This can lead to significant reductions in energy consumption over time, directly contributing to decarbonization efforts.
Supply Chain Sustainability
Electrification and decarbonization efforts often require sourcing more sustainable materials, which can complicate supply chain management. By integrating PlanetTogether with Kinaxis or Aveva, plant managers can ensure that sustainability is embedded throughout the supply chain.
These systems provide advanced tools for managing supplier relationships, monitoring the carbon footprint of sourced materials, and identifying potential risks or disruptions. With such integrations, plant managers can collaborate more effectively with suppliers to ensure that they meet sustainability goals and regulatory requirements.
For instance, integrating PlanetTogether with Aveva can help streamline material flows, ensuring that greener materials are delivered in time to meet production schedules. The advanced forecasting tools provided by Kinaxis, when integrated with PlanetTogether, can also anticipate supply chain disruptions that could arise due to environmental factors, helping plant managers build more resilient, sustainable supply chains.
Minimizing Downtime and Disruptions
The process of electrifying a facility or decarbonizing its operations can lead to significant disruptions if not managed properly. PlanetTogether’s advanced scheduling capabilities, when integrated with ERP systems like SAP or Oracle, can help minimize these disruptions.
The software enables plant managers to plan equipment upgrades, retrofits, and downtime in a way that minimizes impacts on production schedules. For instance, if a facility needs to replace a fossil fuel-powered boiler with an electric alternative, PlanetTogether can optimize production around the downtime required for the installation, ensuring that customer orders are still met and that there are no major disruptions to the supply chain.
In this way, the integration of PlanetTogether with ERP systems allows plant managers to balance electrification efforts with ongoing production needs, ensuring a smooth transition to greener operations.
Electrification and decarbonization represent the next frontier of industrial manufacturing. The path forward may be complex, but with the right strategies and tools, plant managers can navigate these challenges successfully. Integrating software solutions like PlanetTogether with ERP platforms such as SAP, Oracle, Microsoft Dynamics, Kinaxis, or Aveva offers a powerful way to streamline this transition, ensuring that your facility not only meets today’s sustainability standards but also thrives in tomorrow’s green economy.
By adopting electrification and decarbonization strategies, you’re not just reducing your facility’s environmental footprint—you’re future-proofing your operations and setting your company up for long-term success in an increasingly sustainability-focused world. The decisions you make today will shape the future of your facility, your workforce, and your industry as a whole.
Are you ready to take your manufacturing operations to the next level? Contact us today to learn more about how PlanetTogether can help you achieve your goals and drive success in your industry.