Conquering Demand Surges with Leaner Labor Strategies
Operations directors in packaging facilities face a daunting challenge: meeting the growing demand for their products while contending with a shrinking labor force. The need for efficiency has never been greater, and traditional methods of managing production are no longer sufficient.
However, there is hope on the horizon. By leveraging the latest advancements in technology and strategic partnerships, operations directors can streamline their processes, optimize their resources, and meet increased demand with a decreased labor force.
In this blog post, we'll explore how operations directors can integrate advanced planning and scheduling software like PlanetTogether with leading enterprise resource planning (ERP) systems such as SAP, Oracle, Microsoft, Kinaxis, or Aveva to maximize efficiency, minimize labor dependency, and ensure continued success in the face of evolving market demands.
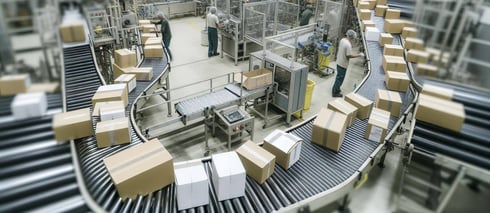
The Challenge
The packaging industry is experiencing unprecedented growth, driven by factors such as e-commerce expansion, increased consumer demand for convenience, and sustainability initiatives. While this presents lucrative opportunities for packaging manufacturers, it also poses significant challenges, particularly in terms of production capacity and labor availability.
Traditionally, meeting increased demand would involve hiring additional workers or extending existing employees' hours, both of which come with their own set of drawbacks, including increased labor costs, training requirements, and potential fatigue-related errors. Moreover, in an era where skilled labor is in short supply, relying solely on manpower is no longer a sustainable solution.

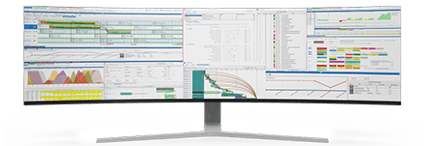
Integration Solutions
To overcome these challenges, operations directors can turn to technology to optimize their production processes and maximize efficiency. By integrating advanced planning and scheduling software like PlanetTogether with their ERP systems, packaging manufacturers can gain greater visibility into their operations, improve decision-making, and automate time-consuming tasks.
Integration with SAP: SAP is a leading provider of ERP solutions, offering comprehensive modules for various industries, including manufacturing. By integrating PlanetTogether with SAP, operations directors can synchronize their production plans with real-time data from across the enterprise, ensuring alignment between demand forecasts, inventory levels, and production schedules.
This integration enables packaging manufacturers to optimize resource allocation, minimize lead times, and respond swiftly to changing market dynamics.
Integration with Oracle: Oracle's ERP suite offers robust capabilities for managing complex supply chains and manufacturing operations. By integrating PlanetTogether with Oracle, operations directors can leverage advanced forecasting algorithms and optimization tools to generate accurate production schedules that balance customer demand, production capacity, and resource constraints.
This integration facilitates seamless communication between different departments, streamlines workflow processes, and enhances overall operational efficiency.
Integration with Microsoft: Microsoft Dynamics ERP solutions provide a flexible platform for integrating various business processes, including production planning and scheduling. By integrating PlanetTogether with Microsoft Dynamics, operations directors can harness the power of data analytics and machine learning to optimize their production schedules in real-time.
This integration enables packaging manufacturers to identify bottlenecks, anticipate potential disruptions, and proactively adjust their plans to meet changing demand patterns.
Integration with Kinaxis: Kinaxis offers a cloud-based platform for supply chain planning and execution, providing end-to-end visibility and control over manufacturing operations. By integrating PlanetTogether with Kinaxis, operations directors can create a unified planning environment that spans across different functional areas, including production, procurement, and logistics.
This integration enables packaging manufacturers to synchronize their production schedules with supplier schedules, demand forecasts, and inventory levels, ensuring smooth execution and timely delivery of products to customers.
Integration with Aveva: Aveva's ERP solutions are tailored to the needs of process industries, offering specialized modules for manufacturing, logistics, and asset management. By integrating PlanetTogether with Aveva, operations directors can optimize their production schedules based on real-time data from IoT sensors, equipment monitoring systems, and predictive analytics algorithms.
This integration enables packaging manufacturers to minimize downtime, maximize equipment utilization, and improve overall operational performance.
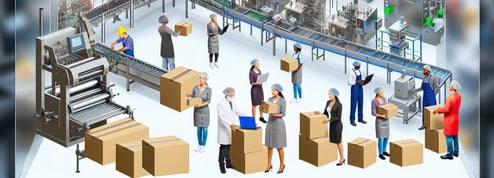
Benefits of Integration
By integrating advanced planning and scheduling software like PlanetTogether with leading ERP systems, operations directors in packaging manufacturing facilities can unlock a host of benefits, including:
Improved Production Efficiency: By aligning production plans with demand forecasts and resource availability, packaging manufacturers can optimize their production schedules, minimize idle time, and maximize throughput.
Reduced Labor Dependency: By automating routine tasks and streamlining workflow processes, operations directors can minimize reliance on manual labor, reduce labor costs, and mitigate the risks associated with labor shortages.
Enhanced Decision-Making: By leveraging real-time data and advanced analytics, operations directors can make informed decisions, anticipate potential disruptions, and proactively adjust their plans to meet changing market demands.
Increased Agility: By creating a flexible and adaptive planning environment, operations directors can respond swiftly to changing customer requirements, market conditions, and supply chain disruptions, ensuring continuity of operations and customer satisfaction.
Meeting increased demand with a decreased labor force is a formidable challenge facing operations directors in packaging manufacturing facilities. However, by embracing technological innovations and strategic partnerships, such as integrating PlanetTogether with leading ERP systems like SAP, Oracle, Microsoft, Kinaxis, or Aveva, operations directors can overcome these challenges, maximize efficiency, and ensure continued success in an increasingly competitive market landscape.
The future of packaging manufacturing lies in harnessing the power of integration to drive operational excellence, innovation, and sustainable growth.
Are you ready to take your manufacturing operations to the next level? Contact us today to learn more about how PlanetTogether and integrated scheduling solutions can help you achieve your sustainability goals and drive success in the packaging industry.