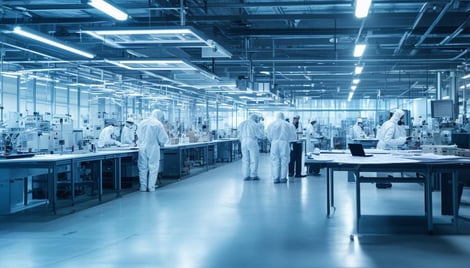
Effective Strategies for Managing Stock-Out Risks in Medical Manufacturing Facilities
In the high-stakes environment of medical manufacturing, maintaining consistent product availability is critical. Stock-outs, where inventory levels fall short of demand, can lead to production delays, missed delivery commitments, and, in some cases, regulatory non-compliance. For production schedulers in medical manufacturing facilities, effectively managing stock-out risks is essential to maintaining both operational efficiency and customer satisfaction.
In this blog, we will explore strategies that can help reduce the risk of stock-outs, highlighting the role of advanced planning tools like PlanetTogether and their integration with enterprise systems such as SAP, Oracle, Microsoft, Kinaxis, and Aveva.
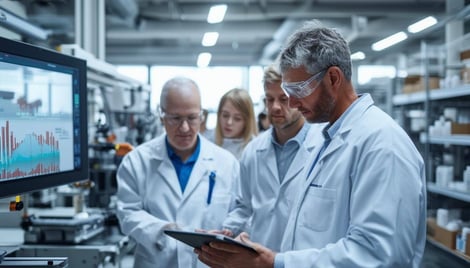
The Cost of Stock-Outs in Medical Manufacturing
Stock-outs in a medical manufacturing facility can result in a variety of negative outcomes. These include:
Production Downtime: A lack of critical materials can halt production, leading to costly delays and missed deadlines.
Increased Costs: Rushed procurement to address shortages often comes at a premium, driving up the cost of materials.
Customer Dissatisfaction: Delays in product availability can damage relationships with customers, particularly when they rely on timely deliveries for patient care.
Regulatory and Compliance Risks: Medical manufacturing is subject to strict regulations, and any delays in the production process can compromise compliance, potentially leading to fines and reputation damage.
These potential consequences make it clear that preventing stock-outs should be a top priority for production schedulers in medical manufacturing.

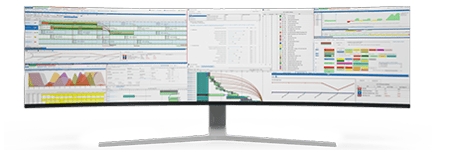
Integrating PlanetTogether with ERP Systems
Leverage Real-Time Data for Better Decision Making
Effective stock-out risk management starts with accurate, real-time data. In many medical manufacturing facilities, legacy systems or disconnected tools often make it difficult for schedulers to have a full, up-to-date picture of inventory levels, production capacity, and demand forecasts. To address this, production schedulers must adopt integrated planning and scheduling systems, such as PlanetTogether, which can be connected to enterprise systems like SAP, Oracle, Microsoft, Kinaxis, and Aveva.
PlanetTogether's integration with these platforms allows production schedulers to access a unified view of operations. This integration enables the system to pull data from sales forecasts, procurement information, inventory levels, and production schedules into a single dashboard, providing decision-makers with the information they need to prevent stock-outs.
For instance, SAP’s powerful enterprise resource planning (ERP) system can track procurement and inventory levels, while PlanetTogether can overlay this data with production schedules, allowing schedulers to anticipate stock-out risks before they occur. Integration with Microsoft tools such as Power BI can help turn data into actionable insights, providing production schedulers with real-time alerts when stock levels approach critical thresholds.
Improve Forecast Accuracy with Predictive Analytics
A core strategy for minimizing stock-out risks is improving the accuracy of demand forecasts. In medical manufacturing, where demand can fluctuate due to market conditions, seasonal factors, or regulatory changes, accurate forecasting is especially challenging. By relying on historical data, predictive analytics, and machine learning, schedulers can make more informed decisions and better prepare for fluctuations in demand.
Systems like Kinaxis RapidResponse and Aveva's advanced planning and scheduling solutions integrate with PlanetTogether to offer predictive analytics capabilities. These tools leverage historical data and market trends to create more accurate demand forecasts, which can be used to adjust production plans and procurement schedules. With better demand visibility, schedulers can adjust their inventory levels and order more precisely, reducing the risk of overstocking or running out of critical materials.
By using predictive analytics, schedulers can also prepare for unexpected spikes in demand or supplier delays, allowing them to proactively manage risks before they impact production. This approach enables better planning and agility in responding to changes in the medical manufacturing landscape.
Establish Strong Supplier Relationships and Collaborative Planning
Supplier reliability plays a crucial role in minimizing stock-outs. In medical manufacturing, sourcing high-quality materials from dependable suppliers is a must. Working closely with suppliers to establish lead times, quality standards, and safety stock levels can help ensure that you receive the right materials at the right time.
However, it’s not enough to just rely on suppliers to meet your needs. To manage stock-out risks effectively, production schedulers must adopt collaborative planning strategies. By integrating supplier data into their planning systems, schedulers can get visibility into potential supply chain disruptions and adjust their schedules accordingly.
PlanetTogether’s integration with ERP systems like SAP and Oracle provides transparency into procurement timelines, allowing schedulers to better align production schedules with supplier lead times. When suppliers face delays or shortages, this integration allows the scheduler to adjust production plans dynamically, either by shifting production to alternative products or expediting orders with critical suppliers.
Furthermore, using collaborative tools, schedulers can maintain open communication with suppliers, sharing real-time demand forecasts and adjusting procurement plans in real time. This can significantly reduce the risk of stock-outs caused by last-minute supply chain issues.
Optimize Inventory Management with Safety Stock Levels
Safety stock is a crucial buffer against supply chain variability. By maintaining an appropriate level of safety stock, medical manufacturers can mitigate the risks associated with supply chain disruptions, delays in deliveries, or unforeseen spikes in demand. However, maintaining too much safety stock can result in increased inventory carrying costs, while too little can lead to stock-outs.
The optimal safety stock level is influenced by factors such as lead times, demand variability, and the criticality of materials. Using advanced planning systems like PlanetTogether, integrated with ERP systems such as SAP, Oracle, or Aveva, production schedulers can optimize their safety stock levels based on real-time demand and supply data. These systems can automatically adjust inventory levels in response to fluctuations in demand, ensuring that safety stock is maintained at an optimal level.
For instance, PlanetTogether can analyze historical demand and lead times to recommend appropriate safety stock levels. When demand spikes or when supplier delays are detected, the system can automatically trigger replenishment orders or adjust production schedules to ensure materials are available when needed.
Implement Agile Production Scheduling
An agile approach to production scheduling can significantly reduce stock-out risks. In medical manufacturing, production schedules often need to be adjusted quickly in response to changing demand, supply disruptions, or other unforeseen circumstances. By implementing agile production scheduling practices, schedulers can create more flexible schedules that can adapt to these changes.
PlanetTogether's integration with systems like Microsoft Dynamics 365 and Kinaxis RapidResponse offers production schedulers the tools to create dynamic schedules that can adjust in real time. With these tools, schedulers can reschedule production runs, prioritize orders, and allocate resources more efficiently to address potential stock-outs.
For example, if a supplier experiences a delay, PlanetTogether can adjust the production schedule to prioritize the use of available inventory and make up for lost production time. Agile scheduling also allows for the quick incorporation of new orders, minimizing the risk of stock-outs due to missed opportunities.
Establish a Proactive Stock-Out Risk Management Plan
A comprehensive risk management plan is essential for anticipating and responding to potential stock-outs. Production schedulers should work with other departments, including procurement, production, and logistics, to identify risks and develop contingency plans.
By integrating data from SAP, Oracle, or Aveva, PlanetTogether can help create a centralized risk management plan that includes factors like supply chain vulnerabilities, supplier performance, and inventory levels. The system can also identify critical materials that are at high risk for stock-outs and provide early warnings to prevent disruptions.
Having a proactive plan in place means that, when a stock-out risk is identified, the team can quickly enact the appropriate response, whether it’s expediting procurement, adjusting production schedules, or increasing safety stock.
Managing stock-out risks in medical manufacturing is a multifaceted challenge that requires accurate forecasting, robust inventory management, agile scheduling, and strong supplier collaboration. By leveraging advanced planning systems like PlanetTogether and integrating them with ERP platforms such as SAP, Oracle, Microsoft, Kinaxis, and Aveva, production schedulers can gain the real-time insights and flexibility needed to prevent stock-outs and maintain smooth operations.
Ultimately, by adopting these strategies and integrating best-in-class tools, medical manufacturing facilities can significantly reduce the risks of stock-outs, ensuring consistent product availability, minimizing costs, and enhancing customer satisfaction in a highly competitive and regulated industry.
Are you ready to take your manufacturing operations to the next level? Contact us today to learn more about how PlanetTogether can help you achieve your goals and drive success in your industry.