Effective Order Processing
Production schedulers stand at the heart of ensuring that customer orders are fulfilled on time, costs are kept in check, and production lines run smoothly. One of the key areas where efficiency can make or break the production process is order processing. For a production scheduler, the complexity of balancing multiple orders, machine capacities, and labor constraints while maintaining optimal lead times is a monumental task.
To ensure a seamless flow from order receipt to order delivery, modern packaging facilities increasingly rely on advanced planning and scheduling tools such as PlanetTogether. But to fully harness the power of these tools, integrating them with broader Enterprise Resource Planning (ERP) systems such as SAP, Oracle, Microsoft, Kinaxis, or Aveva is critical.
This blog will explore how effective order processing can be achieved by production schedulers in packaging manufacturing, focusing on the benefits of integrating these systems and leveraging their full potential.
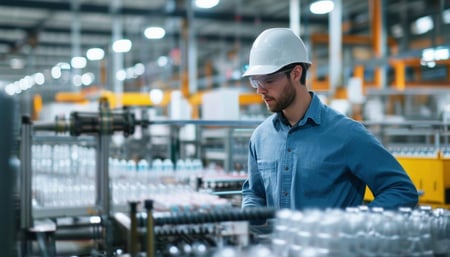
The Role of a Production Scheduler in Order Processing
A production scheduler in a packaging facility is responsible for creating a detailed production plan based on customer orders. They must ensure that all orders are processed efficiently, taking into account:
Machine capacity: Each machine's production capacity, availability, and maintenance schedules.
Material availability: Ensuring that raw materials are available at the right time and in the correct quantities.
Labor allocation: Proper workforce scheduling to meet production requirements.
Order prioritization: Managing priority orders while maintaining regular production schedules.
In a packaging facility, product variety, order customization, and tight deadlines further complicate scheduling. Without the right tools in place, the risk of delays, missed deadlines, excess inventory, and overburdened machinery increases significantly.
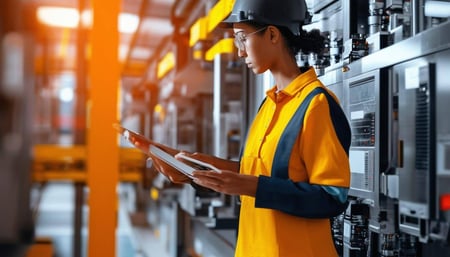
Challenges in Traditional Order Processing
Traditional order processing in packaging manufacturing often involves a lot of manual steps, siloed information, and delays in communication. Production schedulers might receive order information via email or spreadsheets, which need to be manually checked against inventory, machine capacity, and available labor. This process is prone to errors, such as double-booking machines, scheduling downtime during peak production times, or failing to account for delays in material deliveries.
Some common challenges faced include:
Limited visibility across departments: Without real-time integration between production scheduling tools and ERP systems, production schedulers often work with incomplete or outdated information.
Manual data entry errors: Manually transferring data from sales orders to production schedules increases the likelihood of errors.
Inconsistent communication: Different departments, such as procurement, production, and logistics, may not be on the same page regarding priorities and deadlines.
Difficulty in prioritizing orders: In the absence of a system that can dynamically adjust to changing conditions, such as urgent orders or machine breakdowns, schedulers might struggle to adjust priorities.
These challenges emphasize the need for a digital transformation in packaging facilities where real-time data, automated scheduling, and effective communication between systems can enhance order processing.

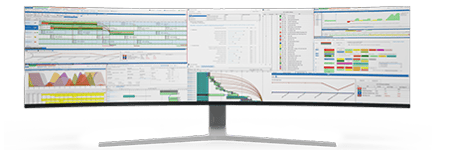
Integrating PlanetTogether with ERP Systems: A Game Changer for Order Processing
The key to overcoming these challenges lies in integrating advanced scheduling systems like PlanetTogether with enterprise-wide platforms such as SAP, Oracle, Microsoft Dynamics, Kinaxis, or Aveva. When these systems are integrated, they enable real-time data exchange between the production floor and business operations, creating a more cohesive and responsive order processing environment.
Real-Time Data Synchronization
One of the biggest advantages of integrating PlanetTogether with an ERP system is real-time data synchronization. When a customer order is placed in the ERP system (e.g., SAP or Oracle), the order details—such as product specifications, quantity, and delivery deadlines—are automatically pushed to PlanetTogether for scheduling. The scheduler no longer needs to manually input the order data or worry about discrepancies between the ERP and production scheduling systems.
In a packaging facility where order volumes can fluctuate daily, real-time data synchronization ensures that schedulers are always working with the most up-to-date information. This means:
Fewer delays due to manual data entry errors.
Automatic adjustments in production schedules based on order changes.
Faster response times to urgent orders or changes in customer demand.
Improved Order Prioritization and Sequencing
Integrating PlanetTogether with ERP systems allows production schedulers to automatically prioritize orders based on predefined criteria, such as customer importance, delivery deadlines, or machine availability. This is particularly important in packaging facilities where some products might need to be prioritized due to shorter shelf lives or customer-specific customization requirements.
For instance, when PlanetTogether is integrated with SAP or Oracle, it can pull data on sales orders, customer contracts, and inventory availability directly from the ERP system. Based on this data, PlanetTogether can intelligently adjust the production sequence, ensuring that high-priority orders are scheduled first while still maximizing machine efficiency.
This capability eliminates the need for manual intervention to adjust production schedules when priorities shift, making the order processing workflow smoother and more efficient.
Enhanced Visibility Across the Supply Chain
A key challenge in order processing is the lack of visibility across the supply chain. For example, if raw material deliveries are delayed or a machine unexpectedly breaks down, it can significantly impact production schedules. By integrating PlanetTogether with ERP systems such as Kinaxis or Aveva, production schedulers gain real-time visibility into the entire supply chain.
This means that if there is a disruption, the scheduler can immediately see how it will affect order processing and adjust the production plan accordingly. For example, if the ERP system flags a material shortage for a high-priority order, PlanetTogether can reschedule other orders to optimize machine usage until the material becomes available.
This end-to-end visibility reduces the risk of downtime, ensures that production schedules are always feasible, and improves overall responsiveness to supply chain disruptions.
Automation of Routine Tasks
Another benefit of integrating PlanetTogether with systems like Microsoft Dynamics is the automation of routine scheduling tasks. In traditional scheduling, production schedulers often spend significant time manually assigning machines, adjusting schedules for maintenance, or reallocating labor based on changing demand.
With an integrated system, tasks such as machine assignments, labor allocation, and production sequencing can be automated based on real-time data from the ERP system. This frees up schedulers to focus on more strategic activities, such as optimizing production efficiency and improving on-time delivery rates.
Improved Decision Making Through Analytics
When PlanetTogether is integrated with ERP systems, it not only enhances real-time operations but also provides powerful analytics for long-term decision making. With data flowing seamlessly between the production scheduling and ERP systems, production schedulers can access detailed reports on key performance indicators (KPIs) such as:
Order lead times
Machine utilization rates
On-time delivery performance
Labor efficiency
By analyzing this data, schedulers can identify bottlenecks, underutilized resources, or recurring issues in the order processing workflow. These insights allow for continuous improvement in production scheduling, helping packaging facilities stay competitive in an increasingly demanding market.
In packaging manufacturing, production schedulers need tools that allow them to make informed, real-time decisions. By integrating PlanetTogether with ERP systems like SAP, Oracle, Microsoft Dynamics, Kinaxis, or Aveva, schedulers can eliminate inefficiencies, reduce lead times, and improve on-time delivery performance.
The result is a more responsive, agile, and efficient order processing system that can keep up with the ever-changing demands of the packaging industry. For production schedulers, this integration provides the visibility, automation, and decision-making power needed to optimize every aspect of the production process—from the moment an order is received to the time it is shipped out the door.
By embracing these advanced technologies, packaging manufacturers can not only meet customer expectations but exceed them, driving long-term success in a competitive market.
Are you ready to take your manufacturing operations to the next level? Contact us today to learn more about how PlanetTogether can help you achieve your goals and drive success in your industry.