Advanced Composite Materials Recycling Technologies
For plant managers in chemical manufacturing facilities, the pressure to reduce waste, minimize environmental impact, and optimize resource utilization is greater than ever. One area where innovation is rapidly reshaping the industry is in advanced composite materials recycling technologies. These advancements not only address environmental concerns but also offer significant economic benefits.
In this blog, we’ll explore the cutting-edge solutions driving the shift towards sustainable chemical manufacturing, with a focus on integration between PlanetTogether and leading ERP, SCM, and MES systems like SAP, Oracle, Microsoft, Kinaxis, and Aveva.
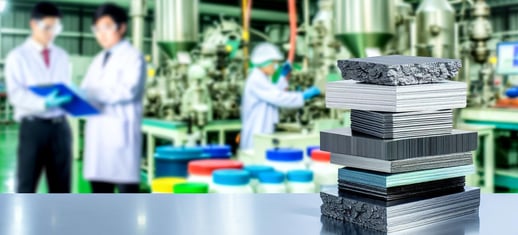
What are Advanced Composite Materials?
Advanced composites are engineered materials made from two or more constituent materials with significantly different physical or chemical properties. These materials are prized for their lightweight, high strength, and corrosion resistance properties, making them ideal for aerospace, automotive, construction, and other industries.
However, the same properties that make advanced composites desirable also complicate their end-of-life management. Traditional recycling methods struggle to effectively separate and recover the constituent materials, leading to high waste generation and limited reuse opportunities. This inefficiency poses environmental risks and undermines the economic viability of composite manufacturing.
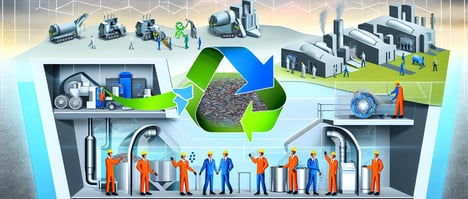
Enter Advanced Composite Materials Recycling Technologies
The quest for sustainable solutions has spurred innovation in advanced composite materials recycling technologies. These technologies leverage a combination of mechanical, chemical, and thermal processes to break down composite structures and recover valuable materials for reuse.
Let’s explore some of the most promising advancements in this field:
Mechanical Recycling: Mechanical recycling involves shredding composite materials into smaller pieces, followed by sorting and processing to separate the constituent materials. Innovations in shredding technology, such as high-speed rotary shearing and cryogenic grinding, enable more efficient breakdown of complex composite structures. Automated sorting systems utilizing advanced sensors and AI algorithms further enhance the recovery process by accurately identifying and segregating different materials.
Chemical Recycling: Chemical recycling techniques aim to chemically decompose composite materials into their original constituents or precursor molecules. Processes like pyrolysis, hydrolysis, and solvolysis break down polymers and resins, allowing for the recovery of valuable monomers and additives. Advancements in catalyst design and reaction kinetics enhance the efficiency and scalability of chemical recycling, making it a viable option for recovering high-purity materials from composite waste streams.
Thermal Recycling: Thermal recycling utilizes heat to break down composite materials and recover valuable components. Techniques such as thermal depolymerization and gasification subject composites to high temperatures in controlled environments, resulting in the conversion of polymers into gases, liquids, and solids. By carefully controlling reaction conditions and optimizing energy recovery systems, thermal recycling offers a sustainable pathway for transforming composite waste into useful products like fuels, chemicals, and feedstocks.
Integration with ERP, SCM, and MES Systems
Effective management of advanced composite materials recycling requires seamless integration between manufacturing operations and enterprise systems. By integrating PlanetTogether with leading ERP, SCM, and MES platforms like SAP, Oracle, Microsoft, Kinaxis, and Aveva, plant managers can unlock a host of benefits:
Real-Time Visibility: Integration enables real-time visibility into production schedules, inventory levels, and material flows across the supply chain. Plant managers can monitor composite waste generation, track recycling processes, and optimize resource allocation to minimize waste and maximize recovery.
Predictive Analytics: Advanced analytics capabilities provided by integrated systems allow plant managers to forecast demand, anticipate material requirements, and optimize recycling operations. Predictive maintenance algorithms help prevent downtime and ensure the reliability of recycling equipment, maximizing throughput and efficiency.
Seamless Workflow Automation: Integration streamlines workflow automation by connecting production planning, scheduling, and execution processes. Automated data exchange between PlanetTogether and ERP, SCM, and MES systems eliminates manual errors, reduces lead times, and improves overall operational efficiency.
Compliance and Reporting: Integrated systems facilitate compliance with regulatory requirements and sustainability standards by providing accurate data capture and reporting capabilities. Plant managers can easily track environmental metrics, demonstrate compliance with recycling targets, and communicate transparently with stakeholders.
The adoption of advanced composite materials recycling technologies represents a significant step towards achieving sustainability goals in chemical manufacturing. By leveraging innovative recycling processes and integrating PlanetTogether with leading ERP, SCM, and MES systems, plant managers can drive efficiency, reduce waste, and create value from composite waste streams.
As the industry continues to embrace sustainability as a core principle, investing in advanced recycling technologies and seamless integration will be essential for staying competitive and future-proofing operations. Together, we can build a more sustainable future for generations to come.
Are you ready to take your manufacturing operations to the next level? Contact us today to learn more about how PlanetTogether can help you achieve your goals and drive success in your industry.