
Driving Growth and Efficiency
The food and beverage industry faces a unique set of challenges. Consumer preferences evolve rapidly, regulatory requirements tighten, and supply chains become increasingly complex. In this environment, the role of a production planner is critical. Tasked with balancing efficiency, cost, and quality, production planners are the linchpin of manufacturing success.
Integrating advanced tools like PlanetTogether with enterprise systems such as SAP, Oracle, Microsoft Dynamics, Kinaxis, or Aveva is a game-changer, enabling planners to drive growth and efficiency simultaneously.
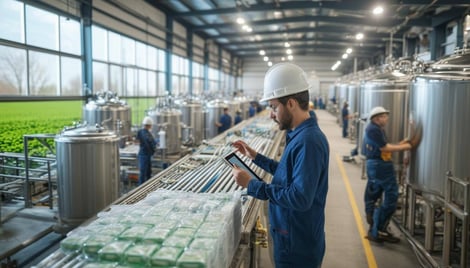
The Growing Complexity of Food & Beverage Manufacturing
Globalization and shifting consumer demands have added layers of complexity to food and beverage manufacturing. Today’s planners contend with:
Shorter Product Lifecycles: Seasonal products, limited-edition flavors, and health-conscious trends require rapid adjustments in production.
Stringent Quality Standards: Ensuring compliance with food safety regulations across regions is non-negotiable.
Volatile Supply Chains: Unpredictable raw material availability, fluctuating costs, and logistical bottlenecks demand agile planning.
Sustainability Pressures: Reducing waste, optimizing energy use, and ensuring ethical sourcing are critical to meeting both regulatory and consumer expectations.
To navigate these challenges, production planners need real-time visibility, streamlined workflows, and robust decision-making tools.

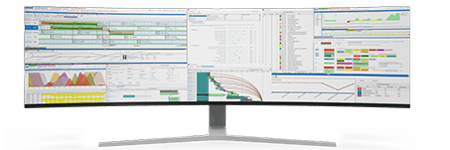
The Power of Integrated Systems: PlanetTogether and ERP/APS Synergy
Production planners often work with multiple systems to coordinate resources, track performance, and forecast demand. However, disconnected tools can lead to inefficiencies, data silos, and suboptimal decisions. This is where integrating PlanetTogether, an advanced planning and scheduling (APS) system, with enterprise resource planning (ERP) platforms like SAP, Oracle, Microsoft Dynamics, Kinaxis, or Aveva can create a seamless ecosystem.
Benefits of Integration for Production Planners:
Real-Time Data Visibility
Integration ensures that all stakeholders, from procurement to production, work with accurate, up-to-date information. For instance, connecting PlanetTogether with SAP provides a unified view of inventory levels, resource availability, and demand forecasts, reducing the risk of overproduction or stockouts.
Optimized Scheduling
Advanced scheduling capabilities in PlanetTogether, coupled with the robust data handling of Oracle, allow planners to simulate multiple scenarios. This enables them to choose the most efficient production plan while accounting for constraints like machine capacity, labor shifts, and raw material availability.
Enhanced Collaboration
With Microsoft Dynamics, integration fosters collaboration across departments. Production planners can easily align with sales and marketing teams to adjust schedules based on promotional campaigns or sudden market shifts.
Reduced Waste and Cost Savings
By leveraging tools like Kinaxis for supply chain optimization and PlanetTogether for precise scheduling, planners can minimize raw material waste and reduce energy consumption, contributing to both cost savings and sustainability goals.
Improved Decision-Making with Predictive Analytics
Integrating Aveva’s advanced analytics with PlanetTogether allows production planners to anticipate potential bottlenecks or delays, enabling proactive adjustments that maintain on-time delivery.
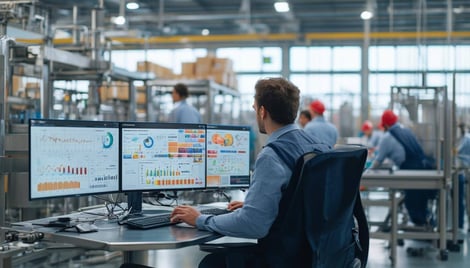
Steps to Drive Growth and Efficiency
Adopt an Integrated Planning Framework
Invest in systems like PlanetTogether and ensure seamless integration with your ERP platform. This unified approach eliminates data silos and enhances operational visibility.
Leverage Predictive and Prescriptive Analytics
Use predictive tools to forecast demand and identify risks. Prescriptive analytics can then suggest the most efficient course of action, aligning production schedules with business goals.
Focus on Continuous Improvement
Implement metrics to measure key performance indicators (KPIs) like order fulfillment rate, inventory turnover, and production cycle time. Use insights from PlanetTogether dashboards to identify and address inefficiencies.
Build Cross-Functional Collaboration
Foster collaboration between production, procurement, and sales teams. Tools like Microsoft Dynamics can facilitate communication and ensure alignment across departments.
Prioritize Employee Training
Equip your team with the skills to maximize the potential of integrated systems. Regular training sessions can help employees stay updated on the latest features and best practices.
Driving growth and efficiency in food and beverage manufacturing requires more than just hard work—it demands smart work. Integration between PlanetTogether and leading ERP platforms empowers production planners to optimize operations, reduce waste, and meet consumer demands with agility. By adopting this integrated approach, planners can not only tackle today’s challenges but also seize tomorrow’s opportunities.
Start your journey towards smarter production planning today—because in the fast-paced world of food and beverage manufacturing, efficiency and growth go hand in hand.
Are you ready to take your manufacturing operations to the next level? Contact us today to learn more about how PlanetTogether can help you achieve your goals and drive success in your industry.
LEAVE A COMMENT