Digital Transformation Supercharges Manufacturing Sales and Orders
Optimizing sales and order processes is vital in medical manufacturing. As a Supply Chain Manager, you're tasked with ensuring seamless operations, timely delivery of products, and maintaining stringent quality standards. In this era of digital transformation, harnessing the power of advanced technologies becomes imperative. One such transformative tool is the integration between PlanetTogether and ERP, SCM, and MES systems.
In this blog, we look into the significance of digital transformation initiatives, explore the benefits of integrating PlanetTogether with various systems, and discuss strategies for optimizing manufacturing sales and orders.
The Importance of Digital Transformation
Digital transformation is revolutionizing the landscape of manufacturing industries worldwide. It encompasses the integration of digital technologies into all aspects of business operations, fundamentally changing how organizations operate and deliver value to customers.
In the medical manufacturing sector, where precision, efficiency, and compliance are non-negotiable, embracing digital transformation initiatives is crucial for staying competitive and meeting evolving market demands.
At the heart of digital transformation lies the synergy between people, processes, and technologies. By leveraging advanced technologies such as artificial intelligence, data analytics, and automation, manufacturers can streamline operations, enhance decision-making capabilities, and drive innovation across the entire supply chain.
Integration between PlanetTogether and ERP, SCM, and MES Systems
PlanetTogether is a powerful production planning and scheduling software that enables manufacturers to optimize their production processes, minimize lead times, and maximize resource utilization. However, its true potential is unlocked when seamlessly integrated with Enterprise Resource Planning (ERP), Supply Chain Management (SCM), and Manufacturing Execution Systems (MES).
Integration with ERP Systems: ERP systems serve as the backbone of manufacturing operations, providing a centralized platform for managing various business processes such as inventory management, procurement, finance, and human resources.
By integrating PlanetTogether with ERP systems like SAP, Oracle, or Microsoft Dynamics, Supply Chain Managers can achieve real-time visibility into sales forecasts, inventory levels, and production schedules. This integration facilitates accurate demand planning, inventory optimization, and ensures alignment between production capacities and customer demand.
Integration with SCM Systems: Supply Chain Management (SCM) systems play a pivotal role in orchestrating the flow of materials, information, and finances across the entire supply chain network.
Integrating PlanetTogether with SCM systems enhances end-to-end visibility, enables proactive risk management, and fosters collaboration with suppliers and distributors. Whether it's demand sensing, supplier collaboration, or transportation management, the synergy between PlanetTogether and SCM systems such as Kinaxis or Aveva enables Supply Chain Managers to respond swiftly to market dynamics and optimize manufacturing sales and orders.
Integration with MES Systems: Manufacturing Execution Systems (MES) bridge the gap between production planning and shop floor execution, providing real-time insights into production activities, quality control, and performance monitoring.
By integrating PlanetTogether with MES systems, such as Wonderware or FactoryTalk, Supply Chain Managers can synchronize production schedules with shop floor operations, track work-in-progress (WIP) inventory, and enforce quality standards throughout the manufacturing process. This integration ensures seamless coordination between planning and execution, minimizes production delays, and enhances overall operational efficiency.
Benefits of Integration
The integration between PlanetTogether and ERP, SCM, and MES systems offers a plethora of benefits for medical manufacturing facilities:
Enhanced Visibility and Control: By consolidating data from disparate systems into a unified platform, Supply Chain Managers gain unprecedented visibility into sales forecasts, inventory levels, production schedules, and resource capacities. This enhanced visibility enables proactive decision-making, better resource allocation, and improved inventory management, ultimately leading to enhanced operational control and agility.
Improved Demand Planning and Forecasting: Integrating PlanetTogether with ERP and SCM systems facilitates seamless data exchange between sales forecasts, production schedules, and inventory levels. This integration enables Supply Chain Managers to conduct accurate demand planning, anticipate market fluctuations, and align production capacities with customer demand. As a result, manufacturers can minimize stockouts, reduce excess inventory, and optimize production schedules to meet customer requirements efficiently.
Streamlined Production Processes: The integration between PlanetTogether and MES systems ensures seamless coordination between production planning and shop floor execution. Real-time data exchange between planning systems and manufacturing operations enables agile decision-making, optimized resource utilization, and minimized production lead times. Additionally, MES integration enables automated data capture, quality control, and performance monitoring, thereby streamlining production processes and enhancing overall efficiency.
Enhanced Collaboration and Communication: Integrating PlanetTogether with ERP, SCM, and MES systems fosters collaboration and communication across departments, suppliers, and partners. With a unified platform for sharing critical information and insights, Supply Chain Managers can facilitate cross-functional collaboration, streamline communication channels, and foster a culture of continuous improvement. Whether it's coordinating production schedules, resolving supply chain disruptions, or addressing quality issues, effective collaboration becomes the cornerstone of operational excellence.
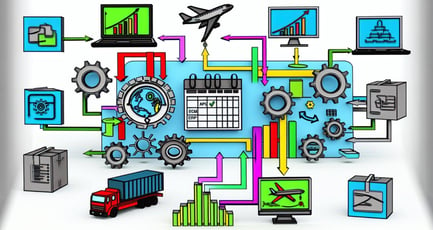
Strategies for Optimization
To maximize the benefits of integrating PlanetTogether with ERP, SCM, and MES systems, Supply Chain Managers can adopt the following strategies:
Invest in Robust Integration Solutions: Choose integration solutions that offer seamless connectivity between PlanetTogether and ERP, SCM, and MES systems. Look for vendors with proven expertise in integration technologies, robust APIs, and a track record of successful implementations in the manufacturing industry.
Prioritize Data Quality and Governance: Ensure data accuracy, consistency, and integrity across integrated systems by implementing robust data quality and governance measures. Establish data standards, validation rules, and governance processes to maintain data integrity and reliability, thereby enhancing the effectiveness of decision-making and planning processes.
Embrace Continuous Improvement: Digital transformation is an ongoing journey, not a one-time event. Embrace a culture of continuous improvement by leveraging data analytics, performance metrics, and feedback mechanisms to identify areas for optimization and innovation. Encourage cross-functional collaboration, empower employees to drive change, and embrace emerging technologies to stay ahead of the curve.
Monitor Key Performance Indicators (KPIs): Establish key performance indicators (KPIs) to monitor the effectiveness of integrated systems, measure performance against predefined benchmarks, and identify areas for improvement. Track metrics such as production lead times, on-time delivery, inventory turnover, and customer satisfaction to gauge the impact of digital transformation initiatives on manufacturing sales and orders.
Digital transformation initiatives hold the key to optimizing manufacturing sales and orders in the medical manufacturing sector. By integrating PlanetTogether with ERP, SCM, and MES systems, Supply Chain Managers can unlock new levels of efficiency, agility, and competitiveness. From enhanced visibility and control to streamlined production processes and improved collaboration, the benefits of integration are manifold.
By embracing digital transformation and adopting a holistic approach to technology integration, medical manufacturing facilities can navigate market uncertainties, meet customer demands, and drive sustainable growth in the digital age.
Are you ready to take your manufacturing operations to the next level? Contact us today to learn more about how PlanetTogether can help you achieve your goals and drive success in your industry.
Topics: Digital Transformation, PlanetTogether Software, Integrating PlanetTogether, Enhanced Visibility and Control, Enhanced Collaboration and Communication, Improved Demand Planning and Forecasting, Medical Manufacturing, Streamlined Production Processes
LEAVE A COMMENT