Downtime Reduction Strategies in Production Scheduling
In today's fiercely competitive industrial manufacturing landscape, minimizing downtime is vital for success. Production schedulers play a pivotal role in this endeavor. They are responsible for orchestrating the complex dance of machinery, labor, and materials to ensure that production runs smoothly, efficiently, and with minimal disruptions.
In this blog, we will look into the world of downtime reduction strategies within production scheduling, with a special focus on how integrating PlanetTogether with leading Enterprise Resource Planning (ERP), Supply Chain Management (SCM), and Manufacturing Execution Systems (MES) can help industrial manufacturers achieve this goal.
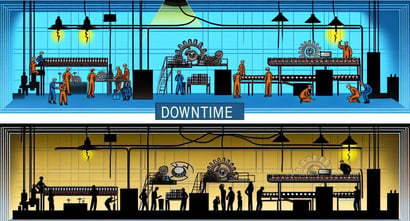
The Impact of Downtime
Downtime, whether planned or unplanned, can have a significant impact on a manufacturing facility's bottom line. Here are some of the key consequences of excessive downtime:
Reduced Productivity: Downtime directly translates to lost production time, resulting in lower output and missed delivery deadlines.
Increased Costs: Labor, energy, and maintenance costs continue to accrue during downtime, driving up the overall production cost.
Quality Issues: Frequent stoppages can lead to inconsistency in product quality due to equipment variations and interruptions in the production process.
Customer Dissatisfaction: Missed delivery schedules can lead to unhappy customers and a tarnished reputation in the market.
Lost Revenue: Reduced production capacity means lost revenue opportunities, which can be especially detrimental in competitive industries.

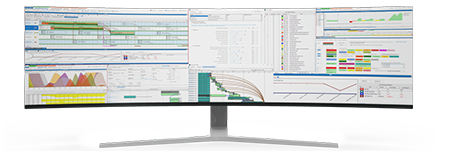
Effective Strategies for Reducing Downtime in Production Scheduling
Predictive Maintenance
Predictive maintenance leverages data from sensors and equipment monitoring systems to anticipate when machinery is likely to fail. By integrating PlanetTogether with ERP systems such as SAP, Oracle, or Microsoft Dynamics, production schedulers can access real-time data on machine health and plan maintenance activities proactively.
This predictive approach allows manufacturers to schedule maintenance during planned downtimes, preventing costly unplanned stoppages. It also extends the lifespan of equipment, reducing the need for frequent replacements.
Real-Time Monitoring
PlanetTogether's integration with MES systems like Aveva or Wonderware enables real-time monitoring of production processes. With access to up-to-the-minute data on machine performance, quality, and work-in-progress, production schedulers can make informed decisions to optimize production flows and reduce downtime.
Advanced Scheduling Algorithms
Modern production scheduling tools like PlanetTogether employ advanced algorithms to create optimal production schedules. By considering factors like machine availability, resource constraints, and order priorities, these tools can generate schedules that minimize downtime while maximizing efficiency.
Integration with SCM systems like Kinaxis ensures that production schedules are synchronized with supply chain demands, reducing the risk of material shortages or overstock situations that can lead to downtime.
Cross-Functional Collaboration
Effective communication and collaboration between different departments in a manufacturing facility are essential for downtime reduction. ERP systems facilitate this by providing a centralized platform for sharing information across the organization.
Through integration with ERP systems, production schedulers can access real-time inventory data, order status, and customer demand forecasts. This visibility allows them to make data-driven decisions that prevent downtime caused by material shortages or production bottlenecks.
Demand Forecasting
Accurate demand forecasting is crucial for optimizing production schedules. Integration between PlanetTogether and ERP systems enables production schedulers to incorporate demand forecasts into their scheduling decisions.
By aligning production with expected customer orders, manufacturers can avoid overproduction, reduce excess inventory, and minimize the risk of downtime due to mismatches between supply and demand.
Employee Training and Skill Development
A well-trained and skilled workforce can help minimize downtime caused by operator errors or inefficiencies. ERP systems can be integrated with Human Resource Management modules to track employee training records and certifications.
By identifying skill gaps and providing targeted training, manufacturers can ensure that their operators are proficient in equipment operation and troubleshooting, reducing downtime associated with human errors.
Root Cause Analysis
When downtime does occur, it's essential to conduct root cause analysis to identify the underlying issues and prevent recurrence. MES systems integrated with PlanetTogether can help capture detailed data on downtime events, enabling production schedulers to analyze patterns and trends.
This data-driven approach can lead to process improvements, equipment upgrades, and preventive measures that reduce downtime in the long run.
Downtime reduction strategies in production scheduling are critical for maintaining competitiveness and profitability in industrial manufacturing. By integrating PlanetTogether with leading ERP, SCM, and MES systems such as SAP, Oracle, Microsoft Dynamics, Kinaxis, Aveva, and others, production schedulers can leverage advanced tools and data-driven insights to minimize downtime effectively.
Predictive maintenance, real-time monitoring, advanced scheduling algorithms, cross-functional collaboration, demand forecasting, employee training, and root cause analysis are just some of the key strategies that can be enhanced through integration.
By adopting these strategies and harnessing the power of integration, manufacturing facilities can optimize production schedules, increase efficiency, and ultimately reduce downtime, leading to improved competitiveness and profitability in today's challenging market environment.
Are you ready to take your manufacturing operations to the next level? Contact us today to learn more about how PlanetTogether can help you achieve your goals and drive success in your industry.
LEAVE A COMMENT