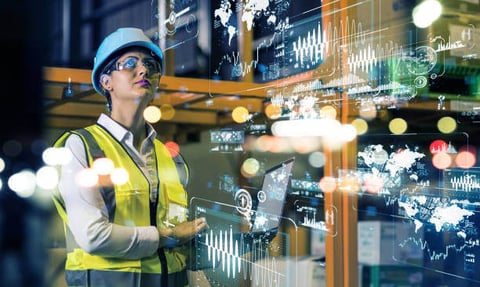
Digital Workflow and Data Interconnection: Revolutionizing Supply Chains in Food & Beverage Manufacturing
The ability to streamline workflows, interconnect data across platforms, and make real-time decisions can be the difference between maintaining a competitive edge and falling behind. Digital workflow and data interconnection—especially through the integration of advanced planning and scheduling (APS) solutions like PlanetTogether with enterprise resource planning (ERP) systems such as SAP, Oracle, Microsoft, Kinaxis, or Aveva—offer a transformative approach to modern supply chain management.
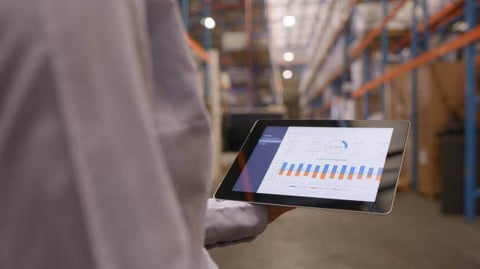
The Need for Digital Workflow and Data Interconnection in F&B Manufacturing
Food and beverage supply chains are uniquely complex. They must navigate perishability, regulatory compliance, fluctuating demand, and ingredient sourcing challenges. Traditionally, siloed operations and manual interventions have hindered efficiency, leading to increased costs, delays, and waste. However, digital transformation is rapidly shifting the landscape, enabling manufacturers to leverage interconnected data streams and automate workflows for better visibility, agility, and decision-making.
By integrating an APS like PlanetTogether with a leading ERP system, manufacturers can:
Enhance operational visibility by centralizing real-time data from production, procurement, logistics, and inventory management.
Automate decision-making through AI-driven analytics, reducing manual errors and improving response times.
Optimize scheduling and production planning, reducing downtime and maximizing resource utilization.
Improve traceability and compliance, ensuring food safety standards are met seamlessly.
Enhance collaboration across departments and suppliers, creating a more responsive and resilient supply chain.

How PlanetTogether and ERP Integration Enhances Supply Chain Operations
Seamless Data Synchronization for Real-Time Insights
In a traditional setup, production schedules, inventory levels, and procurement data often exist in disparate systems, requiring manual reconciliation. Integrating PlanetTogether with an ERP system such as SAP, Oracle, Microsoft, Kinaxis, or Aveva eliminates these inefficiencies by enabling real-time data synchronization.
For example, when production schedules in PlanetTogether are updated, the ERP system automatically adjusts procurement orders, ensuring just-in-time inventory management. This prevents overstocking and stockouts, ultimately reducing waste and improving profitability.
Optimized Production Planning and Scheduling
Food and beverage manufacturers face frequent changes in order volumes, batch sizes, and recipe formulations. Without a dynamic scheduling system, planners struggle to adjust production in response to these changes.
PlanetTogether’s APS leverages machine learning and AI algorithms to optimize scheduling based on real-time demand forecasts, ingredient availability, and equipment capacity. When integrated with an ERP system, this ensures that all departments—from procurement to logistics—are working with the most up-to-date information, improving efficiency across the supply chain.
Improved Supplier Collaboration and Procurement Efficiency
Supply chain disruptions have become increasingly common, making supplier collaboration essential. Digital workflows supported by interconnected data enable manufacturers to maintain proactive supplier relationships.
With an integrated APS-ERP solution, procurement teams gain visibility into real-time ingredient requirements, enabling them to negotiate better terms and ensure timely deliveries. Supplier performance metrics can also be tracked in real-time, helping organizations choose the most reliable vendors.
Reducing Waste and Enhancing Sustainability Goals
Sustainability is a growing priority in food and beverage manufacturing. Digital workflow and data interconnection help companies minimize waste by optimizing production runs and inventory levels.
For example, PlanetTogether can analyze demand patterns and recommend production schedules that reduce excess inventory and ingredient spoilage. When paired with an ERP system’s waste tracking capabilities, manufacturers can implement sustainable practices more effectively, meeting both regulatory requirements and corporate social responsibility goals.
Advanced Traceability and Compliance Management
With stringent food safety regulations, traceability is non-negotiable. Integrated APS-ERP solutions enhance traceability by capturing data at every stage of the supply chain, from sourcing to final delivery.
In the event of a recall, manufacturers can quickly trace affected products back to their source, mitigating risks and ensuring regulatory compliance. This level of transparency not only protects consumers but also strengthens brand trust and operational resilience.
Overcoming Challenges in Digital Workflow Adoption
While the benefits of digital workflow and data interconnection are clear, implementing these solutions comes with challenges. Some common hurdles include:
System Integration Complexity: Ensuring seamless integration between PlanetTogether and an ERP system requires careful planning and customization.
Change Management: Employees accustomed to manual processes may resist digital transformation, necessitating proper training and change management strategies.
Data Security and Compliance: With increased data sharing, cybersecurity measures must be reinforced to protect sensitive supply chain information.
For food and beverage manufacturers, digital workflow and data interconnection are no longer optional—they are essential for survival in an increasingly competitive industry. By integrating PlanetTogether with ERP systems like SAP, Oracle, Microsoft, Kinaxis, or Aveva, supply chain managers can unlock new levels of efficiency, agility, and visibility.
The journey toward digital transformation may have its challenges, but the rewards—enhanced productivity, reduced waste, better compliance, and improved profitability—far outweigh the costs. Now is the time for supply chain managers to embrace interconnected data solutions and build a smarter, more resilient supply chain for the future.
Are you ready to take your manufacturing operations to the next level? Contact us today to learn more about how PlanetTogether can help you achieve your goals and drive success in your industry.
LEAVE A COMMENT