Demand-Driven Scheduling: Enhancing Efficiency and Responsiveness
A supply chain manager’s success is heavily reliant on optimizing production schedules in a way that aligns with real-time demand. The industry’s characteristic complexities — from stringent regulatory requirements to volatile raw material availability — make it vital to use cutting-edge technology to streamline operations. Demand-driven scheduling offers an innovative approach by ensuring that production schedules are continuously updated based on fluctuating market needs.
When coupled with advanced scheduling and planning software like PlanetTogether, integrated with ERP systems like SAP, Oracle, Microsoft Dynamics, Kinaxis, or Aveva, the possibilities for demand responsiveness, cost efficiency, and supply chain resilience are greatly amplified.

What is Demand-Driven Scheduling?
Demand-driven scheduling is a methodology that prioritizes production based on real-time demand data, instead of relying solely on traditional forecast-based planning. This approach allows manufacturers to adjust production schedules promptly, reducing inventory overhead, minimizing lead times, and ensuring that output directly aligns with customer needs.
In a typical forecast-driven model, chemical manufacturing facilities often operate on static production plans, which are set weeks or even months in advance. These plans, while informed by forecasts and historical demand, lack the flexibility to respond to sudden market shifts or unanticipated supply chain disruptions. Demand-driven scheduling, on the other hand, uses real-time demand signals and sophisticated algorithms to continuously adjust the production schedule, thereby making the supply chain more agile and responsive.
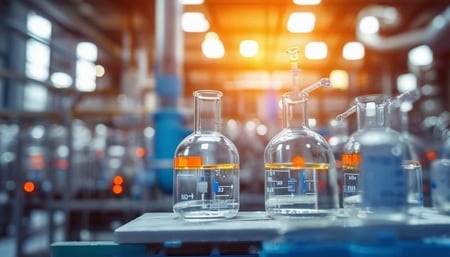
The Benefits of Demand-Driven Scheduling in Chemical Manufacturing
The benefits of implementing a demand-driven approach in chemical manufacturing are vast, ranging from improved customer satisfaction to streamlined operations. Key advantages include:
Enhanced Agility and Responsiveness: Demand-driven scheduling enables manufacturers to adjust production based on actual demand fluctuations, ensuring that resources are optimally allocated to meet customer requirements without excess production.
Inventory Optimization: By producing only what is needed when it's needed, chemical manufacturers can reduce inventory costs. This minimizes the need for large safety stocks, freeing up capital and storage space that can be better utilized elsewhere.
Improved Service Levels: Matching production output with real-time demand improves on-time delivery rates, helping to build stronger relationships with customers and enhancing overall service quality.
Reduced Waste and Operational Costs: Demand-driven scheduling reduces the risks associated with overproduction, such as waste disposal costs and resource inefficiencies. This is especially critical in the chemical industry, where waste management can be costly and tightly regulated.
Resilience to Market Shifts: With demand-driven scheduling, manufacturers can respond more effectively to market changes, making them better equipped to handle both sudden demand spikes and downturns without major disruptions to their operations.

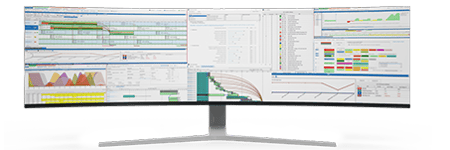
Integration of PlanetTogether with ERP Systems for Demand-Driven Scheduling
For a demand-driven scheduling model to function effectively, robust software that can process real-time data and translate it into actionable production plans is essential. PlanetTogether, an advanced planning and scheduling (APS) software, serves this purpose by helping supply chain managers create agile, demand-responsive schedules.
Integrating PlanetTogether with established ERP systems such as SAP, Oracle, Microsoft Dynamics, Kinaxis, or Aveva amplifies its capabilities by providing a seamless flow of data across the organization. Here’s how such an integration supports demand-driven scheduling:
Real-Time Data Synchronization
PlanetTogether’s integration with ERP systems enables real-time data exchange across the supply chain. For instance, if SAP or Oracle ERP systems detect a surge in customer orders, this information is immediately relayed to PlanetTogether, which can then adjust production schedules accordingly. This level of synchronization helps ensure that production aligns with customer demand down to the minute.
Inventory and Resource Optimization
With ERP systems like Microsoft Dynamics or Aveva providing data on inventory levels and resource availability, PlanetTogether can effectively prioritize production orders based on available resources. This integration allows manufacturers to run demand-driven schedules without exceeding capacity constraints or depleting critical inventory.
For example, in chemical manufacturing, some materials might have short shelf lives or need specific storage conditions. By optimizing production schedules to utilize these materials efficiently, PlanetTogether ensures that resources are used without waste or unnecessary storage costs.
Enhanced Production Visibility
A seamless integration between PlanetTogether and an ERP system offers full visibility into the entire production process. Supply chain managers can view production schedules in real-time, identify potential bottlenecks, and proactively address any issues before they impact customer orders. Additionally, this visibility allows for better collaboration across departments, as teams have a shared, up-to-date view of production priorities and can coordinate their efforts more effectively.
Automated Demand Forecasting and Adjustment
While demand-driven scheduling focuses on current demand signals, forecasting remains a crucial part of planning. Integration with a platform like Kinaxis, which specializes in demand planning and forecasting, enables PlanetTogether to incorporate demand projections into the scheduling algorithm. This capability allows for a balanced approach that combines real-time demand data with forecast insights, enhancing both short-term responsiveness and long-term planning accuracy.
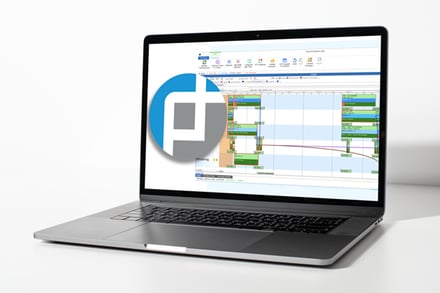
Case Example: PlanetTogether and SAP Integration in a Chemical Manufacturing Facility
Consider a hypothetical chemical manufacturer producing adhesives for a diverse set of industries. Demand for these adhesives can fluctuate based on market conditions, seasonal trends, and shifts in customer needs. Without a demand-driven approach, the facility would likely produce adhesives based on projected demand, potentially leading to overproduction or shortages.
By integrating PlanetTogether with their SAP ERP system, the manufacturer achieves a demand-driven scheduling setup that continuously adjusts to market needs. Here’s how this integration plays out in daily operations:
Real-Time Demand Capture: Customer orders captured in SAP automatically flow into PlanetTogether. When a large order from a construction client comes through, PlanetTogether identifies it and adjusts the production schedule to prioritize adhesive batches for construction applications.
Inventory Management and Resource Allocation: SAP provides PlanetTogether with an overview of current inventory and available resources. Since certain adhesives require specific chemicals that have limited availability, PlanetTogether prioritizes production runs that make the best use of available stock without overcommitting resources.
Enhanced Scheduling Flexibility: As new orders come in or demand shifts, PlanetTogether adjusts the schedule in real time. The integration with SAP ensures that production remains agile, scaling up or down as demand dictates. This responsiveness not only improves on-time delivery rates but also minimizes excess production, reducing costs and waste.
Performance Monitoring: With production schedules in place, SAP and PlanetTogether provide data that supply chain managers use to monitor key performance indicators (KPIs) such as order fulfillment rates, inventory turnover, and lead times. This ongoing analysis allows for continuous improvement and fine-tuning of scheduling strategies.
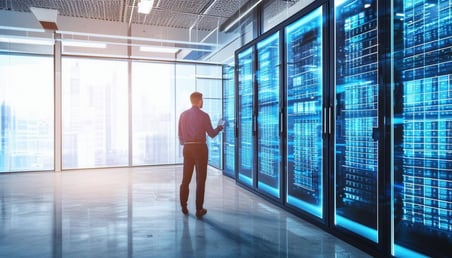
Implementation Considerations for a Demand-Driven Approach
Transitioning to demand-driven scheduling in chemical manufacturing requires careful planning and a phased implementation to minimize disruption. Here are some best practices for implementing PlanetTogether with an ERP system:
Start with a Pilot: Begin by implementing demand-driven scheduling in a specific product line or facility to assess its impact on operations. This approach allows for adjustments based on real-world challenges before scaling up.
Invest in Training and Change Management: Employees will need training to effectively use new software and adapt to a more agile scheduling approach. Change management practices, including transparent communication and ongoing support, can facilitate smoother adoption.
Prioritize Data Quality: The success of demand-driven scheduling relies heavily on the accuracy of real-time data. Invest in systems that ensure data integrity, and regularly audit data sources to maintain high standards.
Monitor and Adjust KPIs: Set clear KPIs aligned with demand-driven goals and monitor them closely. Adjust targets as necessary to reflect the evolving needs of the business and maintain a commitment to continuous improvement.
Demand-driven scheduling, enabled by the integration of PlanetTogether with ERP systems like SAP, Oracle, Microsoft Dynamics, Kinaxis, or Aveva, offers chemical manufacturers a transformative approach to production planning. By aligning production with real-time demand signals, supply chain managers can enhance responsiveness, reduce inventory costs, and improve overall service levels.
The demand for greater agility and efficiency will only increase. Embracing a demand-driven approach not only prepares chemical manufacturers to meet current challenges but also positions them as leaders in an increasingly competitive marketplace. The synergy between PlanetTogether’s advanced scheduling capabilities and a robust ERP system will play a critical role in helping chemical manufacturers stay agile, responsive, and resilient in the face of an ever-changing market landscape.
Are you ready to take your manufacturing operations to the next level? Contact us today to learn more about how PlanetTogether can help you achieve your goals and drive success in your industry.