Deep Reinforcement Learning for Sustainable Resource Utilization
Plant managers constantly seek innovative ways to optimize resource utilization while maintaining sustainability practices. Traditional methods have served well, but with the advent of deep reinforcement learning (DRL), a new era of resource management has emerged.
In this blog, we'll look into the application of DRL in medical manufacturing facilities, specifically focusing on its integration with enterprise resource planning (ERP), supply chain management (SCM), and manufacturing execution systems (MES), such as PlanetTogether and major players like SAP, Oracle, Microsoft, Kinaxis, and Aveva. Let's explore how DRL is revolutionizing sustainable resource utilization.
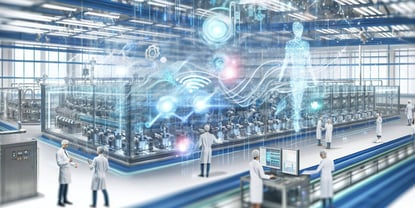
Deep Reinforcement Learning
Deep reinforcement learning is a subset of machine learning that combines deep learning techniques with reinforcement learning principles. It involves training an artificial agent to make sequential decisions in an environment to maximize cumulative rewards. Unlike traditional optimization methods, DRL learns directly from data and interactions with the environment, enabling it to adapt and optimize dynamically.
Challenges in Medical Manufacturing
Medical manufacturing facilities face unique challenges in resource utilization. These include:
- Variability in demand: Fluctuating demand for medical products requires flexible production schedules and resource allocation.
- Complex supply chains: Medical manufacturing relies on intricate supply chains with multiple suppliers, making coordination and inventory management challenging.
- Regulatory compliance: Strict regulations govern the production of medical devices and pharmaceuticals, necessitating meticulous tracking of resources and processes.
- Sustainability goals: With increasing emphasis on sustainability, manufacturers must minimize waste and energy consumption while maximizing resource efficiency.
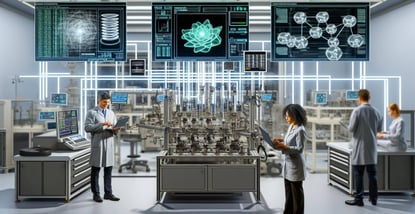
Integration of DRL with ERP, SCM, and MES Systems
To address these challenges, plant managers are integrating DRL with their existing ERP, SCM, and MES systems. This integration offers several benefits:
- Real-time decision-making: By leveraging DRL's ability to learn from real-time data, manufacturers can make proactive decisions to optimize resource utilization and respond swiftly to changes in demand or supply chain conditions.
- Adaptive planning: DRL enables adaptive planning by continuously learning and adjusting production schedules based on evolving conditions, improving responsiveness and efficiency.
- Enhanced forecasting: Integrating DRL with ERP and SCM systems enhances demand forecasting accuracy, enabling better allocation of resources and inventory management.
- Sustainable operations: DRL algorithms can optimize processes to minimize waste, energy consumption, and environmental impact, aligning with sustainability goals.
- Autonomous optimization: With DRL, systems can autonomously optimize resource allocation and production schedules, reducing the need for manual intervention and streamlining operations.
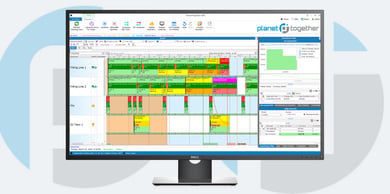
Optimizing Production with DRL and PlanetTogether Integration
By combining DRL's adaptive optimization capabilities with PlanetTogether's advanced scheduling algorithms, facilities achieved remarkable results:
- Improved production efficiency: DRL continuously optimized production schedules based on real-time data, leading to a significant increase in overall equipment effectiveness (OEE) and production throughput.
- Reduced lead times: Dynamic scheduling enabled by DRL and PlanetTogether integration minimized lead times, allowing the facilities to fulfill orders more quickly and meet customer demands effectively.
- Enhanced resource utilization: By optimizing resource allocation and minimizing downtime, facilities maximized the utilization of equipment, labor, and materials, leading to cost savings and improved profitability.
- Sustainable practices: DRL algorithms prioritized sustainable practices by minimizing energy consumption, reducing waste, and optimizing inventory levels, aligning with the facility's environmental goals.
Deep reinforcement learning holds immense potential for revolutionizing resource utilization in medical manufacturing facilities. By integrating DRL with ERP, SCM, and MES systems such as PlanetTogether, manufacturers can achieve unprecedented levels of efficiency, responsiveness, and sustainability.
Plant managers must embrace this transformative technology to stay competitive in an ever-evolving industry landscape. As we move towards a future of intelligent manufacturing, DRL will continue to play a pivotal role in shaping sustainable and efficient operations.
Are you ready to take your manufacturing operations to the next level? Contact us today to learn more about how PlanetTogether can help you achieve your goals and drive success in your industry.