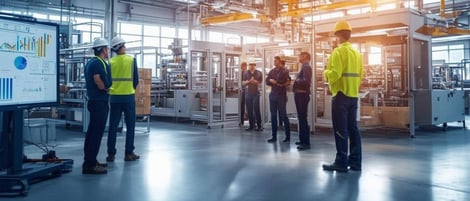
Dealing with Unplanned Downtime in Scheduling: A Strategic Approach for Packaging Manufacturing
In packaging manufacturing, maintaining an efficient and uninterrupted production flow is critical. Supply Chain Managers face a myriad of challenges, and among the most disruptive is unplanned downtime. When machinery fails, or unforeseen supply chain issues arise, the ripple effects can be felt throughout the entire operation, jeopardizing deadlines, increasing costs, and frustrating customers. Leveraging advanced scheduling tools like PlanetTogether, integrated with robust enterprise solutions such as SAP, Oracle, Microsoft, Kinaxis, or Aveva, can be transformative in minimizing the impact of such disruptions.
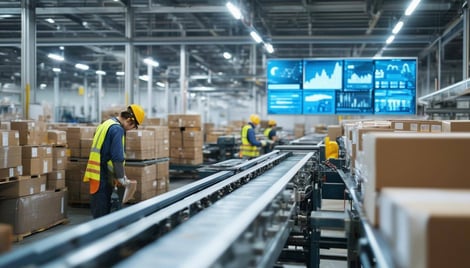
The Cost of Unplanned Downtime
Unplanned downtime in packaging manufacturing doesn't just stall production; it often results in significant financial and operational consequences. The cost implications include:
Lost Revenue: Idle machines mean unfulfilled orders, which can lead to lost sales and strained customer relationships.
Increased Operational Costs: Emergency repairs, expedited shipping, and overtime labor can quickly inflate costs.
Supply Chain Disruptions: A single downtime event can delay downstream processes, creating a domino effect that disrupts the entire supply chain.
Reputation Damage: Consistently failing to meet delivery timelines can erode trust with clients, impacting long-term business prospects.
Given these stakes, mitigating unplanned downtime is not just a maintenance issue—it’s a strategic priority.
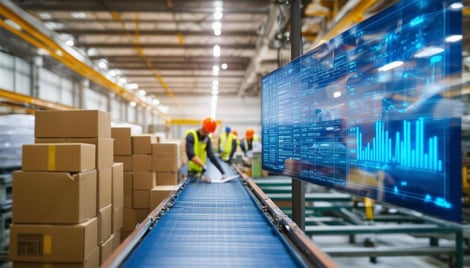
Root Causes of Unplanned Downtime
To address unplanned downtime effectively, it’s essential to understand its root causes. These typically include:
Equipment Failures: Machines in high-demand environments like packaging manufacturing are prone to breakdowns if not properly maintained.
Supply Chain Interruptions: Delays in raw materials or packaging components can halt production lines.
Scheduling Inefficiencies: Poorly planned schedules can overburden equipment or fail to account for maintenance windows, leading to unanticipated failures.
Human Error: Mistakes in setup, operation, or maintenance can result in operational halts.

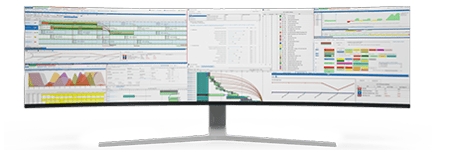
The Role of Advanced Scheduling Tools
Tools like PlanetTogether, when integrated with enterprise systems such as SAP or Kinaxis, can provide a comprehensive solution to deal with unplanned downtime. These platforms facilitate dynamic scheduling, real-time visibility, and predictive analytics that enable better decision-making.
Real-Time Visibility
Integration with systems like SAP or Microsoft Dynamics provides a single source of truth for production data. With PlanetTogether’s scheduling capabilities, Supply Chain Managers gain real-time insights into machine availability, order status, and inventory levels. This visibility allows teams to:
Quickly identify bottlenecks.
Reschedule production to minimize delays.
Communicate accurate timelines to stakeholders.
Dynamic Rescheduling
When downtime occurs, a static schedule can exacerbate delays. PlanetTogether’s dynamic rescheduling feature, supported by integration with ERP systems like Oracle or Aveva, enables teams to:
Automatically adjust schedules to prioritize high-value orders.
Reassign resources to underutilized machines.
Simulate different scenarios to choose the optimal recovery strategy.
Predictive Maintenance and Analytics
Through integration with IoT-enabled systems, advanced scheduling platforms can leverage predictive maintenance insights. For example:
SAP’s predictive analytics tools can identify patterns in machine performance, alerting managers to potential failures before they occur.
PlanetTogether can incorporate these insights into scheduling algorithms, ensuring that maintenance activities are seamlessly integrated into production plans.
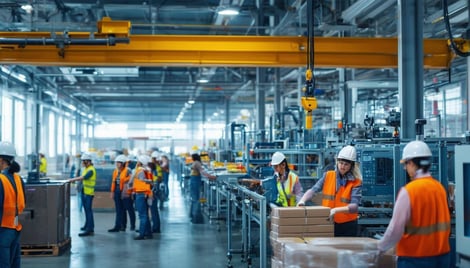
Strategies to Mitigate Unplanned Downtime
Proactive Maintenance Scheduling
Integrating maintenance schedules into production planning ensures that necessary repairs and upkeep don’t conflict with production demands. With tools like PlanetTogether, integrated with ERP systems, Supply Chain Managers can:
Schedule maintenance during low-demand periods.
Track equipment usage to predict wear and tear.
Reduce reliance on reactive repairs, which are often costlier and more disruptive.
Buffering Inventory and Capacity
Maintaining safety stock and reserving a buffer in production capacity can help absorb the impact of downtime. Integration with platforms like Kinaxis enables smarter inventory planning by aligning stock levels with dynamic production schedules.
Enhanced Collaboration Across Teams
Unplanned downtime often requires a coordinated response from multiple departments. Integrated platforms enable:
Seamless communication between production, maintenance, and supply chain teams.
A unified dashboard to track recovery efforts in real time.
Improved accountability and faster resolution times.
Leveraging Historical Data for Better Planning
By analyzing historical downtime data, Supply Chain Managers can identify patterns and implement preventive measures. Tools like Aveva’s manufacturing execution system (MES) can provide valuable insights, which can then be integrated with PlanetTogether for improved scheduling accuracy.
For Supply Chain Managers in packaging manufacturing, unplanned downtime is a challenge that can no longer be left to chance. By adopting advanced scheduling tools like PlanetTogether and integrating them with robust enterprise systems such as SAP, Oracle, Microsoft, Kinaxis, or Aveva, manufacturers can minimize downtime’s impact and build more resilient operations.
These tools provide the agility to respond to disruptions, the insights to prevent future occurrences, and the collaboration capabilities to align teams toward shared goals. As the packaging industry becomes increasingly competitive, embracing these technologies is not just a tactical move but a strategic necessity.
By prioritizing effective scheduling and integration, you can turn unplanned downtime from a major obstacle into a manageable challenge, ensuring that your supply chain remains a model of efficiency and reliability.
Are you ready to take your manufacturing operations to the next level? Contact us today to learn more about how PlanetTogether can help you achieve your goals and drive success in your industry.
LEAVE A COMMENT