Cyber-Physical Systems in Production Planning
The integration of technology has become essential for achieving efficiency, accuracy, and agility in chemical manufacturing. One of the most transformative advancements in recent years has been the advent of Cyber-Physical Systems (CPS) in production planning.
In this blog, we look into the significance of CPS in the context of chemical manufacturing facilities, exploring how they streamline operations and enhance decision-making. Furthermore, we'll examine the integration between PlanetTogether, a leading production planning software, and various ERP, SCM, and MES systems like SAP, Oracle, Microsoft, Kinaxis, and Aveva, elucidating the benefits it brings to the manufacturing IT ecosystem.
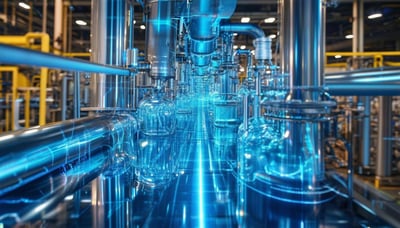
Understanding Cyber-Physical Systems (CPS)
CPS refers to the integration of computational algorithms and physical processes, creating interconnected networks that enable real-time monitoring, control, and optimization of manufacturing operations. This integration bridges the gap between the virtual and physical worlds, revolutionizing traditional production paradigms.
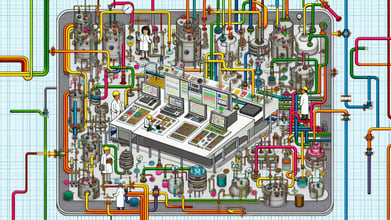
The Role of CPS in Chemical Manufacturing
Chemical manufacturing, with its intricate processes and stringent safety standards, stands to benefit immensely from CPS implementation. Here's how:
Real-Time Monitoring and Control: CPS enables continuous monitoring of critical parameters such as temperature, pressure, and chemical compositions. By integrating sensors and actuators with production equipment, manufacturers can detect anomalies in real-time and initiate corrective actions promptly, minimizing downtime and reducing the risk of costly errors.
Predictive Maintenance: Predictive maintenance is essential in chemical manufacturing to prevent equipment failures and ensure uninterrupted production. CPS utilizes machine learning algorithms to analyze equipment data and predict maintenance requirements accurately. By identifying potential issues before they escalate, manufacturers can schedule maintenance proactively, optimizing asset utilization and extending equipment lifespan.
Optimized Resource Allocation: CPS facilitates dynamic resource allocation based on real-time demand fluctuations and production constraints. By leveraging advanced optimization algorithms, manufacturers can optimize production schedules, allocate resources efficiently, and minimize wastage, resulting in significant cost savings and improved productivity.
Enhanced Decision-Making: CPS provides decision-makers with real-time insights into production performance, enabling data-driven decision-making. By integrating historical data, production forecasts, and market trends, manufacturers can make informed decisions regarding inventory management, production planning, and supply chain optimization, ensuring alignment with business objectives and market demands.

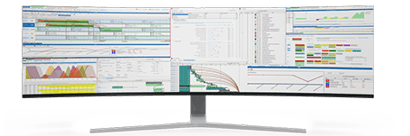
Integration between PlanetTogether and ERP, SCM, and MES Systems
The seamless integration between production planning software like PlanetTogether and ERP, SCM, and MES systems is instrumental in harnessing the full potential of CPS in chemical manufacturing facilities. Let's explore how this integration enhances manufacturing IT capabilities:
Data Synchronization: Integration enables seamless data exchange between production planning software and ERP, SCM, and MES systems, ensuring consistency and accuracy across the manufacturing ecosystem. This eliminates data silos and enables stakeholders to access real-time information for informed decision-making.
End-to-End Visibility: By integrating production planning with ERP, SCM, and MES systems, manufacturers gain end-to-end visibility into production processes, supply chain operations, and business workflows. This visibility enables proactive monitoring and control, facilitating timely interventions to address bottlenecks and optimize resource utilization.
Streamlined Workflows: Integration streamlines workflows by automating data transfer and synchronization between disparate systems. This reduces manual effort, minimizes errors, and accelerates decision-making processes, enhancing operational efficiency and agility.
Enhanced Analytics: Integrated systems enable comprehensive data analytics by consolidating production, inventory, and supply chain data from multiple sources. This empowers manufacturers to derive actionable insights, identify performance trends, and uncover optimization opportunities, driving continuous improvement and innovation.
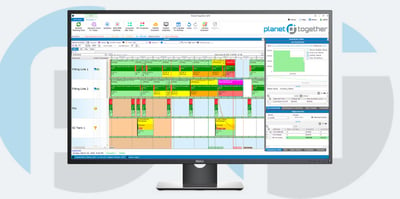
Optimizing Production Planning with PlanetTogether Integration
Let's consider a hypothetical scenario where a chemical manufacturing facility integrates PlanetTogether with SAP, a leading ERP system. By leveraging this integration, the facility achieves the following outcomes:
Improved Demand Forecasting: Integration with SAP enables PlanetTogether to access real-time demand forecasts and customer orders, facilitating accurate production planning and inventory management.
Dynamic Production Scheduling: PlanetTogether dynamically adjusts production schedules based on SAP data, such as raw material availability, equipment capacity, and production priorities, optimizing resource allocation and minimizing lead times.
Enhanced Supply Chain Collaboration: Integration with SAP enhances supply chain collaboration by synchronizing production schedules with procurement, logistics, and distribution processes, ensuring timely delivery of raw materials and finished products.
Real-Time Performance Monitoring: PlanetTogether provides real-time performance metrics and KPIs, allowing stakeholders to monitor production progress, identify deviations, and take corrective actions promptly to ensure production targets are met.
Cyber-Physical Systems (CPS) are revolutionizing production planning in chemical manufacturing facilities, enabling real-time monitoring, predictive analytics, and data-driven decision-making. The integration between production planning software like PlanetTogether and ERP, SCM, and MES systems amplifies the benefits of CPS, fostering operational excellence, agility, and innovation. By embracing CPS and leveraging integration capabilities, chemical manufacturers can stay ahead of the curve in an increasingly competitive and dynamic market landscape.
As manufacturing IT professionals, it's imperative to recognize the transformative potential of CPS and seize the opportunities it presents to drive business growth and competitive advantage. Embrace the future of production planning with CPS and integrated systems, and unlock new possibilities for your chemical manufacturing facility.
Are you ready to take your manufacturing operations to the next level? Contact us today to learn more about how PlanetTogether can help you achieve your goals and drive success in your industry.